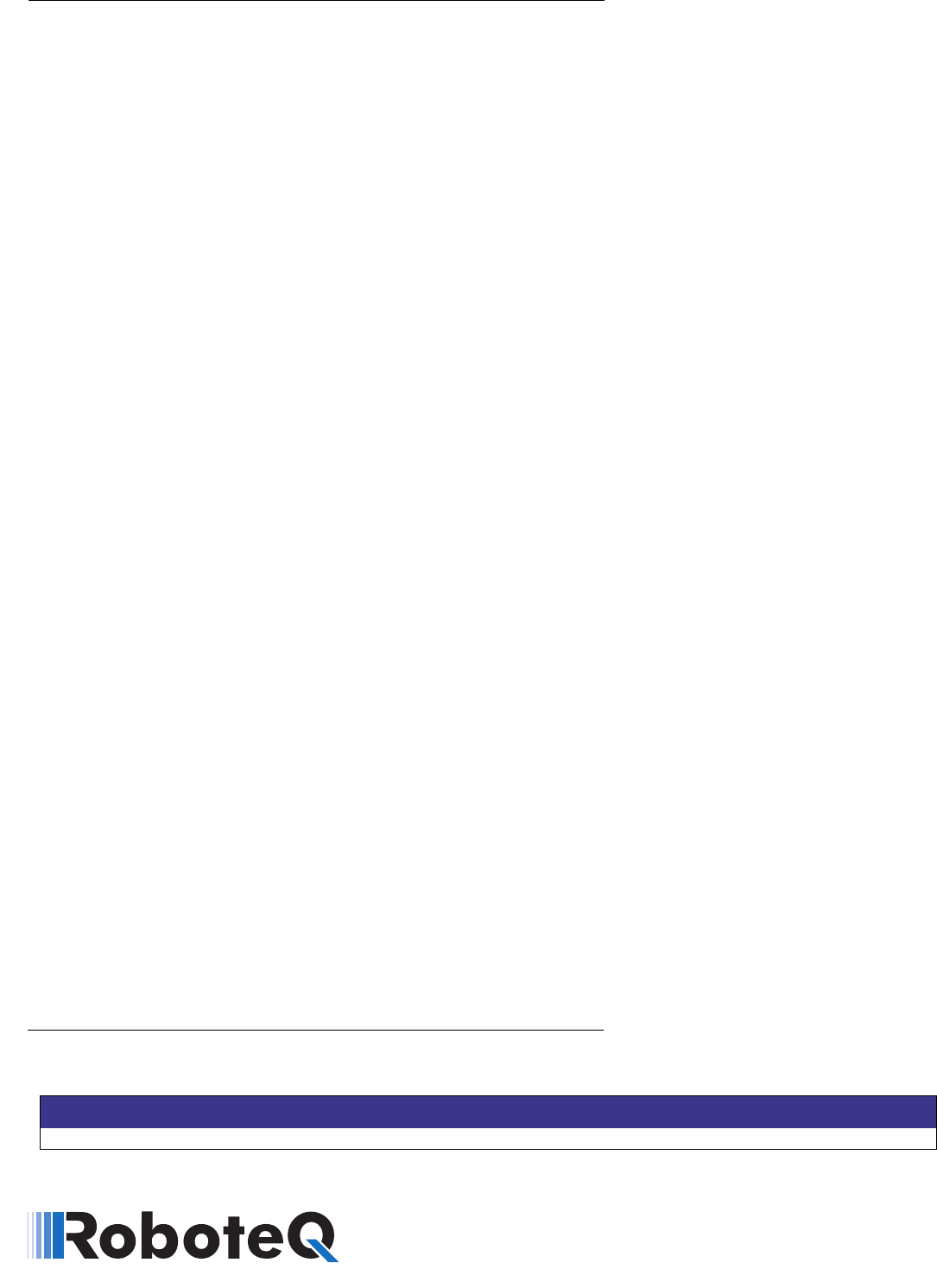
Model Description
AX3500 Dual Channel 60 SmartAmps DC Motor Controller with Optical encoder input
Microcomputer-based Digital Design
• Multiple operating modes
• Fully programmable using either built-in
switches and 7 segment LED display or
through connection to a PC
• Non-volatile storage of user configurable
settings. No jumpers needed
• Simple operation
• Software upgradable with new features
Multiple Command Modes
• Serial port (RS-232) input
• Radio-Control Pulse-Width input
• 0-5V Analog Voltage input
Multiple Motor Control modes
• Independent channel operation
• Mixed control (sum and difference) for
tank-like steering
• Open Loop or Closed Loop Speed mode
• Position control mode for building high
power position servos
• Modes can be set independently for each
channel
Optical Encoder Inputs
• Two Quadrature Optical Encoders inputs
• 250kHz max. frequency per channel
• 32-bit up-down counters
• Inputs may be shared with four optional
limit switches
Automatic Command Corrections
• Joystick min, max and center calibration
• Selectable deadband width
• Selectable exponentiation factors for each
joystick
• 3rd R/C channel input for accessory output
activation
Special Function Inputs/Outputs
• 2 Analog inputs. Used as
• Tachometer inputs for closed loop
speed control
• Potentiometer input for position (servo
mode)
• External temperature sensor inputs
• User defined purpose (RS232 mode
only)
• One Switch input configurable as
• Emergency stop command
• Reversing commands when running
vehicle inverted
• Up to 2 general purpose outputs for acces-
sories or weapon
• One 24V, 2A output
• One low-level digital output
• Up to 2 digital input signals
• 8 RC pulses outputs for connection to
additional Roboteq slave controllers or RC
servos
Built-in Sensors
• Voltage sensor for monitoring the main 12
to 40V battery
• Voltage monitoring of internal 12V
• Temperature sensors near each Power
Transistor bridge
Advanced Data Logging Capabilities
• 12 internal parameters, including battery
voltage, captured R/C command, tempera-
ture and Amps accessible via RS232 port
• Data may be logged in a PC or microcom-
puter
• Data Logging Software supplied for PC
Low Power Consumption
• On board DC/DC converter for single 12 to
40V battery system operation
• Optional 12V backup power input for pow-
ering safely the controller if the main
motor batteries are discharged
• 200mA at 12V or 100mA at 24V idle cur-
rent consumption
• Power Control wire for turning On or Off
the controller from external microcom-
puter or switch
• No consumption by output stage when
motors stopped
• Regulated 5V output for powering R/C
radio. Eliminates the need for separate R/C
battery.
High Efficiency Motor Power Outputs
• Two independent power output stages
• Dual H bridge for full forward/reverse oper-
ation
• Ultra-efficient 2.5 mOhm ON resistance
MOSFETs
• Four quadrant operation. Supports regen-
eration
• 12 to 40 V operation
• User programmable current limit up to 60A
depending on heatsink arrangement
• Single channel, 120A optional configura-
tion
• Standard Fast-on connectors for power
supply and motors
• 16 kHz Pulse Width Modulation (PWM)
output
• Aluminum heat sink. Optional conduction
cooling plate
Advanced Safety Features
• Safe power on mode
• Optical isolation on R/C control inputs
• Automatic Power stage off in case of elec-
trically or software induced program failure
• Overvoltage and Undervoltage protection
• Watchdog for automatic motor shutdown
in case of command loss (R/C and RS232
modes)
• Large and bright run/failure diagnostics on
7 segment LED display
• Programmable motors acceleration
• Built-in controller overheat sensors
• “Dead-man” switch input
• Emergency Stop input signal and button
Compact Design
• All-in-one, single board design
• Efficient heat sinking. Operates without a
fan in most applications.
• 6.75” (171.5mm) L, 4.2” W (107mm),
1. 2 5” (32mm) H
• -20o to +75o C operating environment
• 7.5oz (220g)
Technical Features
Ordering Information
www.roboteq.com
8180 E.Del Plomo Dr.
Scottsdale, AZ 85258 - USA
602-617-3931