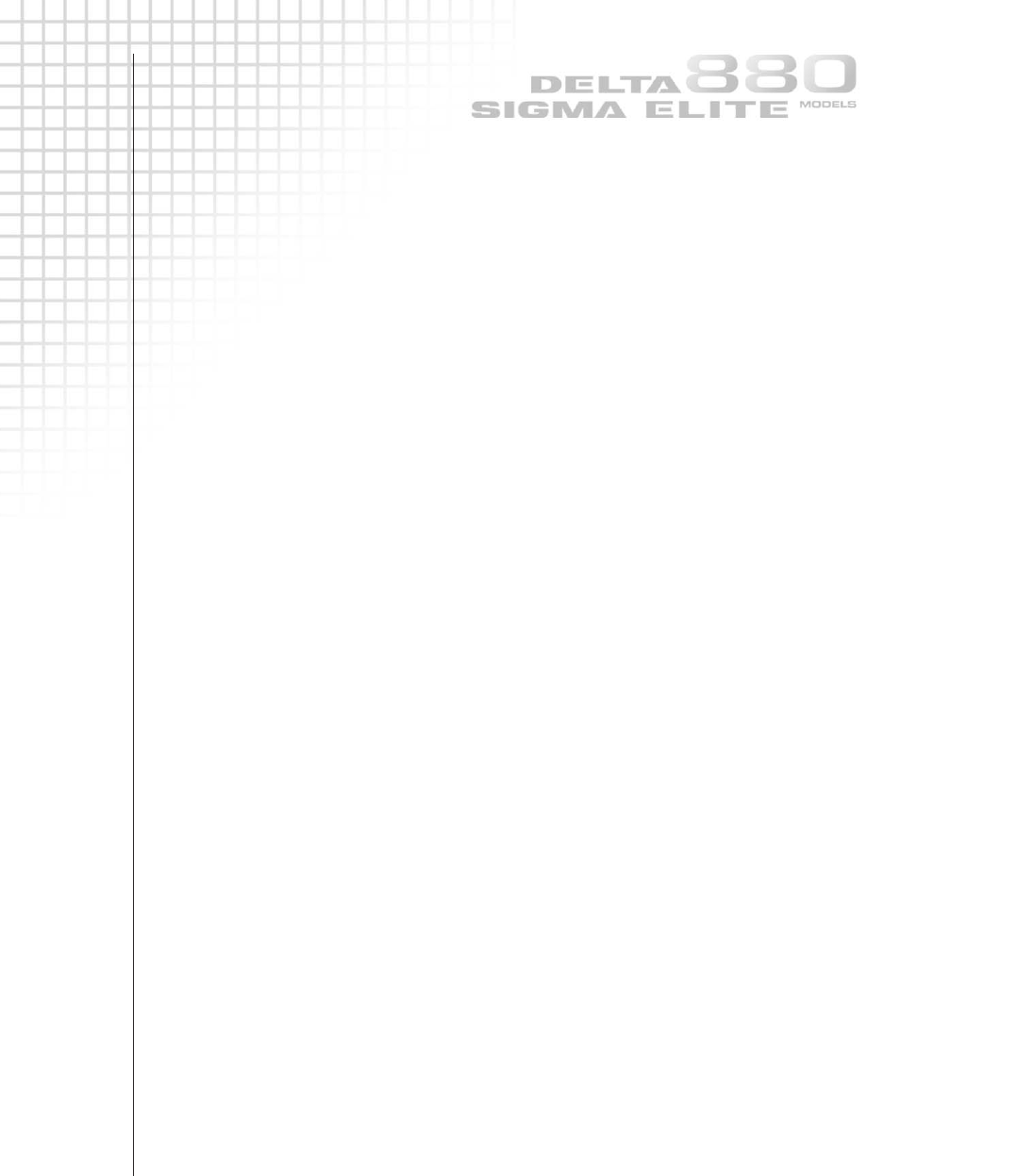
DAILY INSPECTION INSTRUCTIONS
3.8
1 Remote control inspection: Uncoil the remote controls at the site. Inspect the control
crank to assure all screws are present and tightened and that the crank handle is properly
secured. If the control crank is equipped with an odometer, zero the odometer while the
control cable is fully retracted. Verify the odometer is fully functional.
Ensure the instructions on the control crank's label are legible. These instructions are
important to safety, especially when assistants are being trained or during an emergency.
Without the instructions it is conceivable a radiographer could become confused as to which
direction the crank handle must be turned to retract or expose the source.
Ensure the brake is operational. Resistance should be felt while rotating the crank handle
with the brake in the ON position. Inspect the control conduit fittings to verify they are
secured to the control crank.
2 Control conduit inspection: Inspect the control conduit where it is swaged onto the
fittings that mount on the control crank. There should be no evidence of cracks or breaks in
the yellow PVC sheath. Also, look for bulges in that area that result from repeated flexing.
Visually inspect the entire length of both control conduits looking for dents, cuts and
thermally damaged areas. During this inspection, the radiographer should use his hands to
feel for inward dents. Cuts and melted areas found on the control conduits should be sealed
with PVC tape to prevent against the ingress of water.
Inspect the control conduits where they are swaged to the swage fittings that are mounted
to the connecting plug assembly. There should be no evidence of cracks, breaks or bulges in
the yellow PVC sheath.
Remove the protective cover from the connecting plug assembly. Inspect the connecting
plug assembly to verify the movable jaws are not excessively loose and the connector collar
pins are not excessively loose or bent. Check the control sheath swage fittings to verify they
are not loose where they are joined to the connecting plug assembly.
3 Control cable inspection: Inspect the control cable connector as it protrudes out of the
connecting plug assembly. The control cable connector should not be bent or at an angle
exceeding 15 degrees relative to the control cable centerline. If a control cable connector
is repeatedly bent at an angle greater than 15 degrees, damage to the control cable may
be introduced by straightening the bend. Inspect the control cable (male) connector to
verify that the stem and ball of the connector is not bent or cracked. Using hand pressure,
attempt to twist the control cable connector from the control cable. If the control cable
connector can be twisted using hand pressure or appears bent or cracked, remove from
service and label as defective.
Pull approximately 12in (30.5cm) of control cable out of the connecting plug assembly and
inspect for the following anomalies directly behind the connector:
●
Cuts, breaks, nicks or fraying of the spiral windings of the control cable.
●
Areas with kinks or permanent bends.
●
Rust (a red oxide) on the inner core of the control cable.
●
Uniformity of the spacing between the outer spiral windings. Also check for flattened
areas and wear.
●
Bend the connector section of control cable back towards itself and release the cable
to test for flexibility or ‘spring’ of the control cable. A cable that has been subjected to
the flexibility test and remains in the bent position after the test provides an indication
of internal corrosion and must be removed from service.
●
Verify that a light coating of mil-spec grease is present on the control cable. The light
coating of grease is necessary to prevent the penetration of water and chemicals that
can oxidize and permanently damage the control cable.