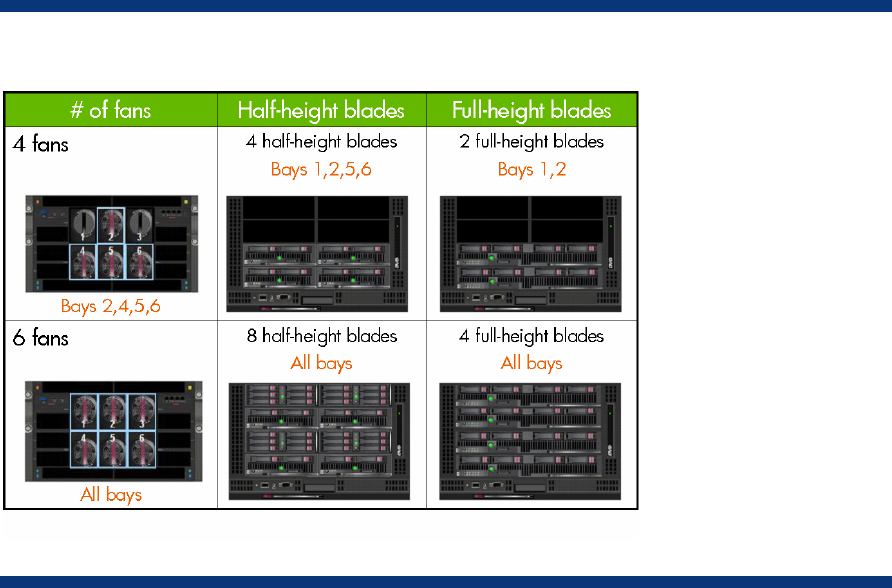
Figure 5. The c3000 Enclosure fan bay and device bay population guidelines
Thermal Logic for the server blade and enclosure
The server blade design uses precise ducting throughout the server blade to manage airflow and
temperature based on the unique thermal requirements of all the critical components. The airflow is
tightly ducted to ensure that no air bypasses the server blade and to obtain the most thermal work
from the least amount of air. This concept allows much more flexibility in heat sink design choice. The
heat sink design closely matches the requirements of the server blade and processor architecture. For
example, in the Intel® Xeon® based HP BladeSystem BL460c server blade, HP was able to use a
smaller, high-power processor heat sink than in rack-mount servers. These heat sinks have vapor
chamber bases, thinner fins, and tighter fin pitch than previous designs. This allows creating the
largest heat transfer surface in the smallest possible package (Figure 6). The smaller heat sink allows
more space for full-size DIMM sockets and hot plug hard drives on the server blades.
Ducting produces high pressure, so the server blade uses less airflow and that reduces fan power
requirements. The lower airflow requirement has the added benefit of optimizing available data
center cooling capacity, which is one of the main issues facing IT facilities today and in the future.
Each device (server blades, interconnect modules, and enclosure subsystems) includes temperature
sensors that monitor heat. If high temperature levels occur, the Integrated Lights-Outs (iLO) and
Onboard Administrator modules provide alerts to various management tools such as Insight Control
and HP Insight Manager. In addition, built-in failsafes will shut down devices in the enclosure if
temperature levels exceed specified parameters. This prevents permanent damage to any devices
within the enclosure.
7