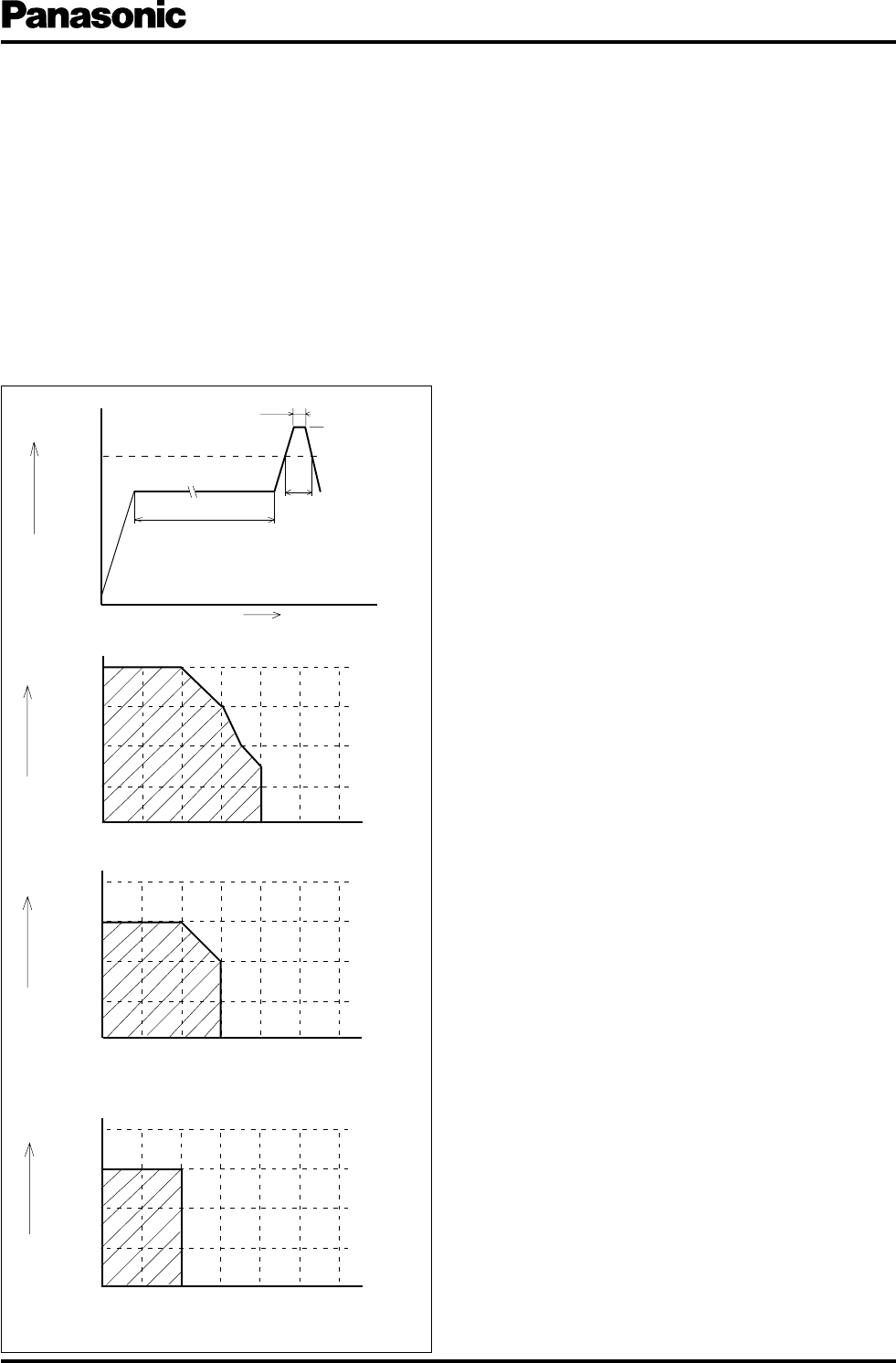
Aluminum Electrolytic Capacitor
Design, Specifications are subject to change without notice. Ask factory for technical specifications before purchase and/or use.
Whenever a doubt about safety arises from this product, please inform us immediately for technical consulation without fail.
– EE20 –
2.4 Flow Soldering
(1) Don not immerse the capacitor body into the
solder bath as excessive internal pressure could
result.
(2) Observe proper soldering conditions (temperature,
time, etc.). Do not exceed the specified limits.
(3) Do not allow other parts or components to touch
the capacitor during soldering.
2.5 Reflow Soldering for Chip Capacitors
(1) For reflow, use a thermal conduction system such
as infrared radiation (IR) or hot blast. Vapor heat
transfer systems (VPS) are not recommended.
(2) Observe proper soldering conditions (temperature,
time, etc.). Do not exceed the specified limits.
(3) Reflow should be performed one time. Consult us
for additional reflow restrictions.
2.7Capacitor Handling after Soldering
(1) Avoid movement of the capacitor after soldering
to prevent excessive stress on the leadwires
where they enter the seal.
(2) Do not use the capacitor as a handle when
moving the circuit board assembly.
(3) Avoid striking the capacitor after assembly to
prevent failure due to excessive shock.
2.8 Circuit Board Cleaning
(1) Circuit boards can be immersed or ultrasonically
cleaned using suitable cleaning solvents for up
to 5 minutes and up to 60° C maximum
temperatures. The boards should be thoroughly
rinsed and dried.
Recommended cleaning solvents include
Pine Alpha ST-100S, Sunelec B-12, DK Beclear
CW-5790, Aqua Cleaner 210SEP, Cold Cleaner
P3-375, Telpen Cleaner EC-7R, Clean-thru 750H,
Clean-thru 750L, Clean thru 710M, Techno
Cleaner 219, Techno Care FRW-17, Techno
Care FRW-1, Techno Care FRV-1, IPA (isopropyl
alcohol)
✽ The use of ozone depleting cleaning agents are
not recommended in the interest of protecting
the environment.
(2) Avoid using the following solvent groups unless
specifically allowed for in the specification;
● Halogenated cleaning solvents: except for solvent
resistant capacitor types, halogenated solvents
can permeate the seal and cause internal
capacitor corrosion and failure. For solvent
resistant capacitors, carefully follow the
temperature and time requirements of the
specificaion. 1-1-1 trichloroe thane should never
be used on any aluminium electrolytic capacitor.
● Alkali solvents: could attack and dissolve the
aluminum case.
● Petroleum based solvents: deterioration of the
rubber seal could result.
● Xylene: deterioration of the rubber seal could
result.
● Acetone: removal of the ink markings on the
vinyl sleeve could result.
Time in
200°C or more
250
200
150
100
50
120(s)
5(s)
Time
240
230
220
210
0 10 20 30 40 50 60
240
230
220
210
0 10 20 30 40 50 60
2.6Other Soldering Considerations
Rapid temperature rises during the preheat
operation and resin bonding operation can cause
cracking of the capacitor vinyl sleeve. For heat
curing, do not exceed 150°C for a maximum time of
2 minutes.
✽ Temperature measuring method: Measure
temperature in assuming quantitative production, by
sticking the thermo-couple to the capacitor upper
part with epoxy adhesives.
Peak
temperature
Parts upper part temperature (°C)
Chip capacitor reflow guaranteed condition
Time in 200°C or more (s)
(φ3 to 6.3φ)
Peak temperature (°C)
Peak temperature (°C)
Time in 200°C or more (s)
(φ8 to φ10)
160°C
240
230
220
210
0 10 20 30 40 50 60
EB Series
Peak temperature (°C)
Time in 200°C or more (s)
(φ10 to φ18)
Mar. 2005