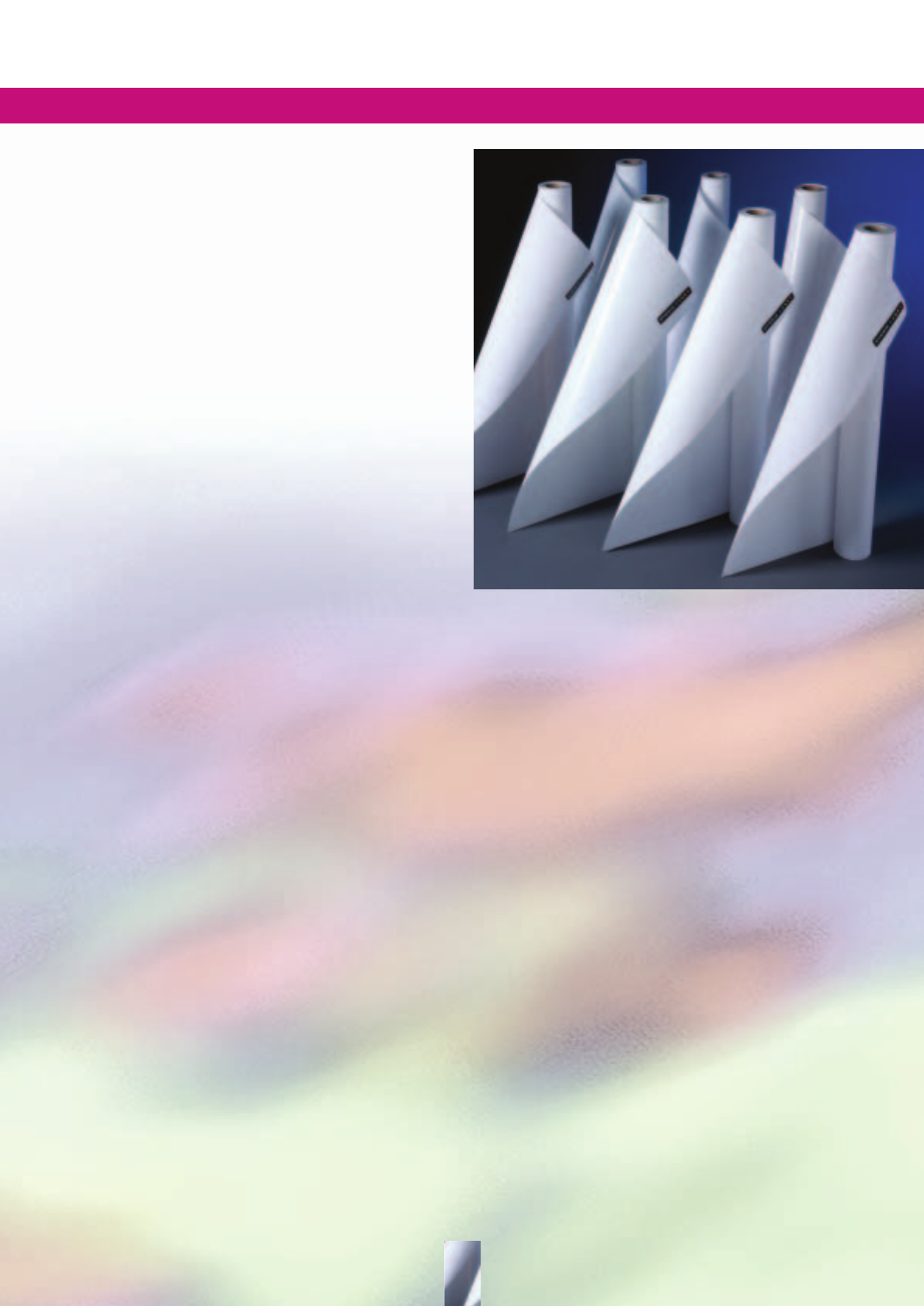
Designs on
Inkjet Paper
•
Optimum print colour density (good fixation);
•
Fast drying time without paper curl or cockle (fast
absorption);
•
High brightness;
•
Lightfast and waterfast qualities;
•
Wet rub and scuff resistance (no ink smearing);
•
Lateral ink spread to enhance text resolution and
colour-to-colour bleed by controlling the dot diameter.
(The resolution specified by a printer can only be
achieved through using the right substrate);
•
Sufficient stiffness for feeding through printer.
Of these: printed colour density, ink drying time and
colour bleed all depend heavily on the coating structure
of the paper. Paper or other media with a coated water-
receiving layer can greatly improve both colour density
and resolution by controlling the ink spreading and
penetration at the coated layer.
For this reason, within the past few years, the market for
specialty-coated inkjet media has exploded, especially in
the home photo quality and large-format inkjet printing
areas.
Another important factor in achieving quality prints is
resolution. This relates to how much pictorial
information a file holds. The DPI (dots per inch), tells us
the resolution of an image; the higher the dpi, the higher
the resolution and hence the finer the detail of the
printed image. High resolution is generally considered to
be 1200-5000 dpi.
In conventional printing, variable sized dots are set down
in fixed patterns that in CMYK form 'rosettes'. These are
formed because the screen is orientated differently for
each colour. So screen angle, dpi and dot size all affect
the way that the transparent inks overlap and make
colours and images in conventional printing. Screen
angles are optimised for specific plates, presses,
processes, etc., to prevent moiré and maximize
sharpness and vibrance.
Unlike commercial four-colour process, most inkjet
printing forms images by printing small dots of the
same size at varying distances from each other – often
overlapping so dot gain is more critical (This is known as
stochastic screening). Dot gain relates to the tendency of
the dots to print larger than they appear on the original.
A drop in print contrast indicates that dot gain is too
great – the dots merge and the image loses definition.
On press dot gain is normally due to ink spreading as it
hits the paper, and is affected by many factors; ink
viscosity, substrate absorbency, paper coating and half
tone screen ruling (fine and stochastic screen give
higher dot gain)
IF WHAT INK IS USED FOR INKJET PRINTING IS
IMPORTANT
, SO IS THE CHOICE OF STOCK. THE
IDEAL WISH
-LIST WHEN LOOKING AT DESIRED
PROPERTIES OF PAPER USED IN INKJET PRINTING
,
WOULD INCLUDE:
11