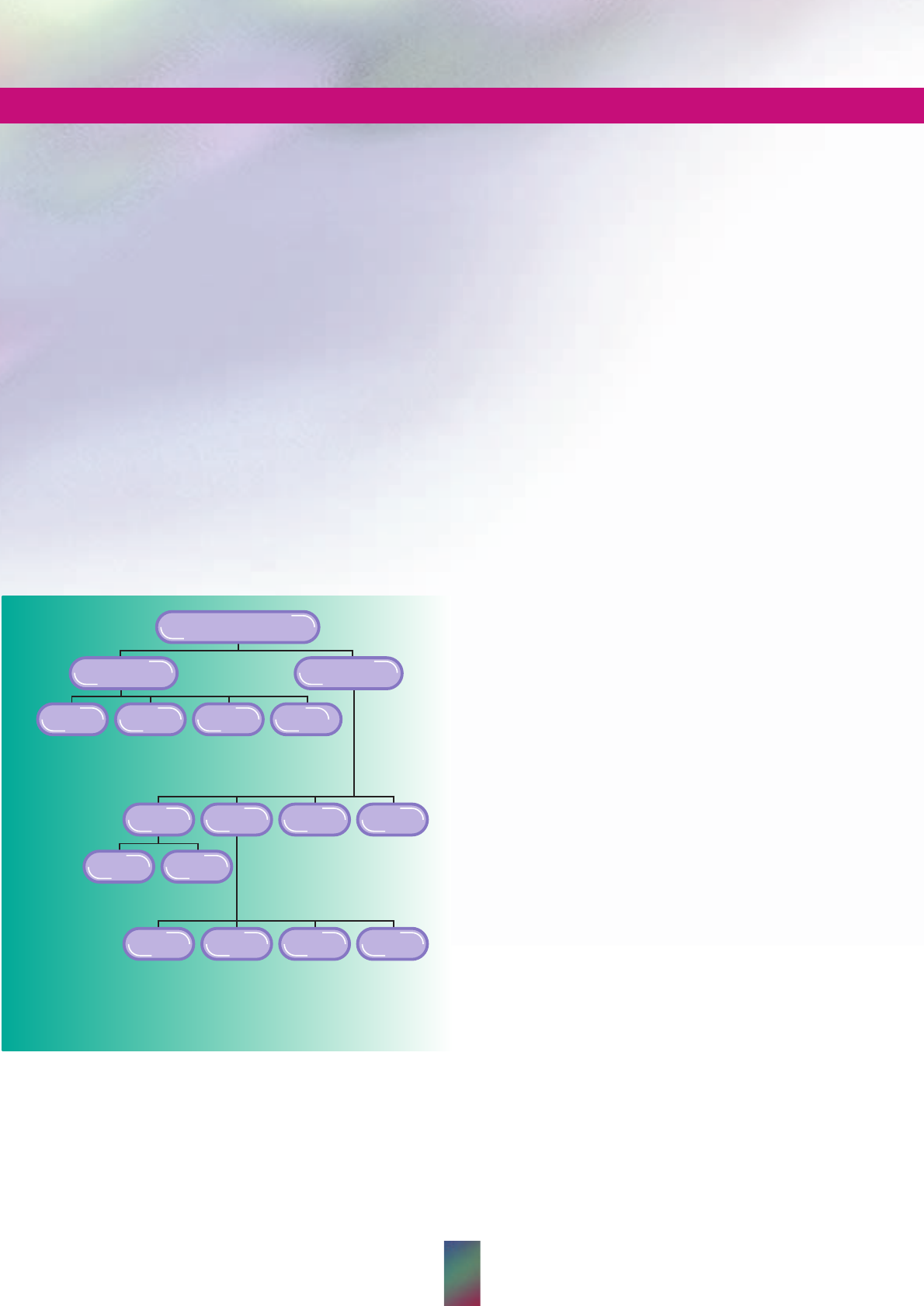
4
Continuous inkjet
Continuous inkjet – perhaps most widely used in the
industrial coding, marking and labelling markets - can
be designed using a binary or multiple deflection
system.
Put simply, with a binary deflection system some of the
ink-drops are charged and some are uncharged. It is the
charged drops that fly directly onto the media, while the
uncharged drops are ‘deflected’ into a gutter for
recirculation. Whereas with a multiple deflection system
(also known as raster imaging) the design is essentially
reversed, so while the uncharged ink-drops fly directly
into the gutter for recirculation, the charged drops are
‘deflected’ onto the media at different levels.
Meanwhile, another continuous inkjet concept - the Hertz
concept (named after Professor Hertz of the Lund
Institute of Technology in Sweden) - can be given
separate classification because of its unique way of
obtaining gray scale through a burst of small drops. By
varying the number of drops laid down, the amount of ink
volume in each pixel was controlled by Hertz, therefore
the density in each colour could be adjusted to create the
gray tone desired, making this ideal technology for high
quality colour images at a stage where drop-on-demand
quality could not really compete.
Drop-on-demand
But today, drop-on-demand technology can readily
compete, and the majority of activity in inkjet printing
currently available utilises one of two drop-on-demand
methods: thermal and piezo (or piezo-electric). That is to
say that the printing devices supplied by most of today’s
manufacturers are equipped with either thermal or piezo
print heads. This is mainly due to the cost effectiveness
of this technology over continuous inkjet.
Thermal inkjet print heads receive signals from the
control unit, which causes an internal heating device to
heat up rapidly and boil the ink present to form a bubble.
The heat increases until the bubble bursts and forces the
droplet out through the nozzle onto the substrate at high
speed. Droplet size may vary from half to full size by
heating one or two elements respectively.
Piezo processing on the other hand, works through the
piezoelectric effect. Here, currents pass through
piezoelectric crystals or ceramic chambers. This causes
the chambers to change shape, which squeezes ink from
the nozzles. To produce larger droplets the voltage must
be increased which displaces more ink, resulting in a
larger droplet. Manufacturers have also experimented
more recently with acoustic (also referred to as airbrush)
and electrostatic inkjet, but these technologies are still
very much in the developmental stage and few
commercial products employing them are yet available.
Chart 1
INK JET TECHNOLOGY
Continuous
Drop-on-Demand
Binary
Deflection
Elmjet
Scitex
Image
Hewlett-Packard
Olivetti
Lexmark
Canon
Xerox
Siemens
Gould
Tektronix
Sharp
Epson
On Target Tech.
Dataproducts
Epson
Trident
Spectra
Xaar
Nu-Kole
Brother
Microfab Tech.
Philips
Topaz Tech.
Videojet
Diconix
Domino Amjet
Linx
Iris Graphics Hitachi
Multiple
Deflection
Hertz
Microdot
Thermal
Roof-shooter Side-shooter
Squeeze Tube
Bend Mode Push Mode Shear Mode
Piezoelectric Electrostatic Accoustic