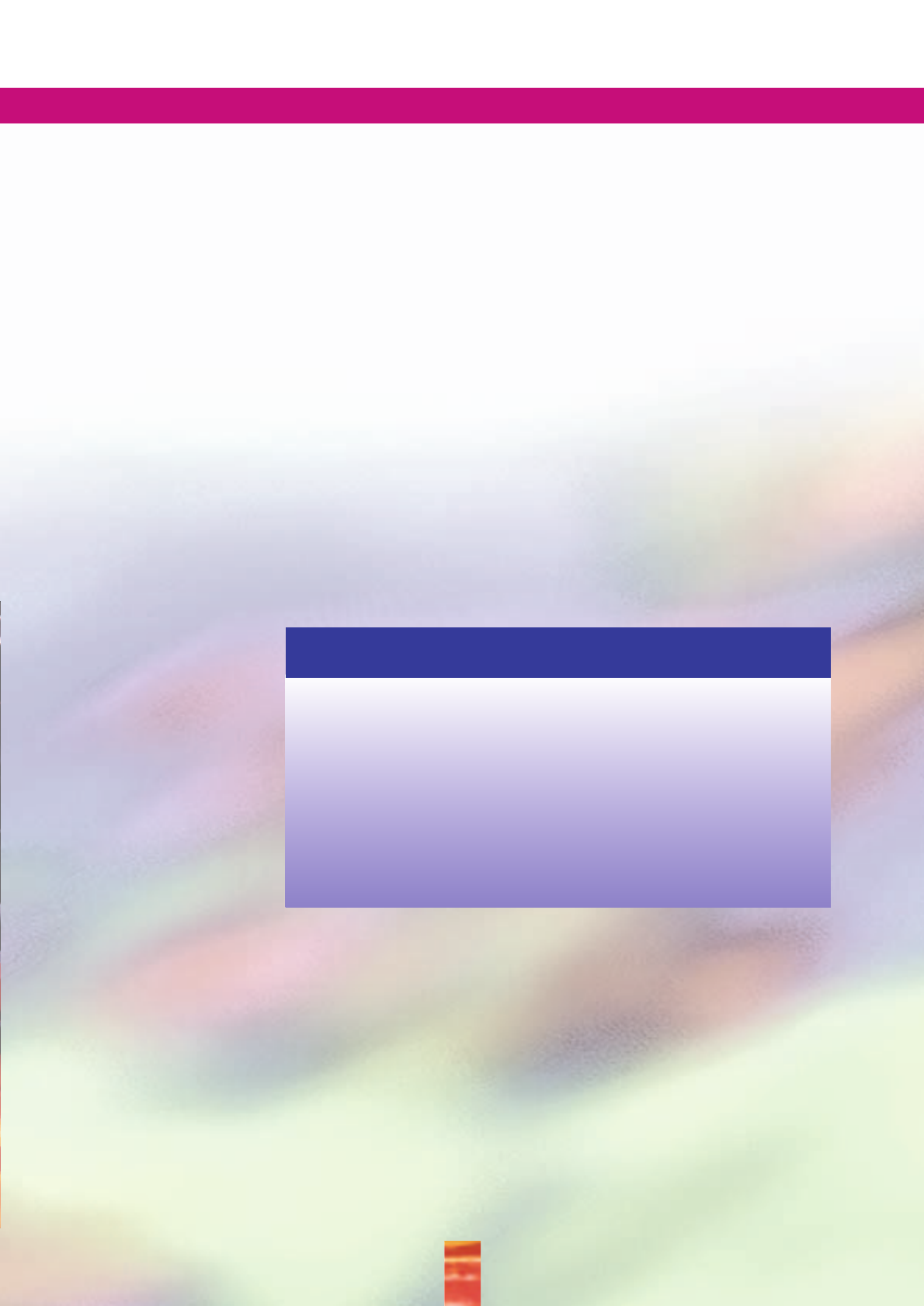
7
All of these designs and their drop performances
ultimately determine the quality and throughput of a
printed image. The trend in the industry is in jetting
smaller droplets for image quality, generating faster
drop frequency through a higher number of nozzles for
additional print speed, while inevitably trying to keep the
cost of manufacture down. In an attempt to achieve this,
what we have seen is the continued miniaturization of
the inkjet print head design, where consequently,
reliability issues have become even more critical.
The nozzle
Independent of a print head’s configuration, one of the
most critical components in a print head design is its
nozzle. Nozzle geometry such as diameter and thickness
directly effects drop
volume, velocity, and
trajectory angle.
Variations in the
manufacturing process of
a nozzle plate can
significantly reduce the
resultant print quality.
Image banding is a
common result from an
out-of-specification nozzle
plate. Various nozzle
geometries have been
designed for inkjet print
heads: the two most
widely used methods for making the orifice plates being
electroformed nickel and laser ablation on the polymide
(other known methods include electro-discharged
machining, micro-punching, and micro-pressing).
Because smaller ink drop volume is required to achieve
higher resolution printing, the nozzle diameter of print
heads has become increasingly small. With the trends
towards smaller diameters and lower cost, the laser
ablation method has become increasingly popular in the
manufacture of inkjet nozzles. This trend towards
smaller nozzles can more easily be achieved using piezo
technology.
Thermal Piezo
+ Less expensive technology + Wide range of inks useable
+ Modulate drop size ->
better resolution
- Limited inks useable + Higher drop rates
- Limitations on ink properties + Longevity
- Limited number of
nozzles per row
- Higher costs per nozzle
Thermal vs. Piezo Technology