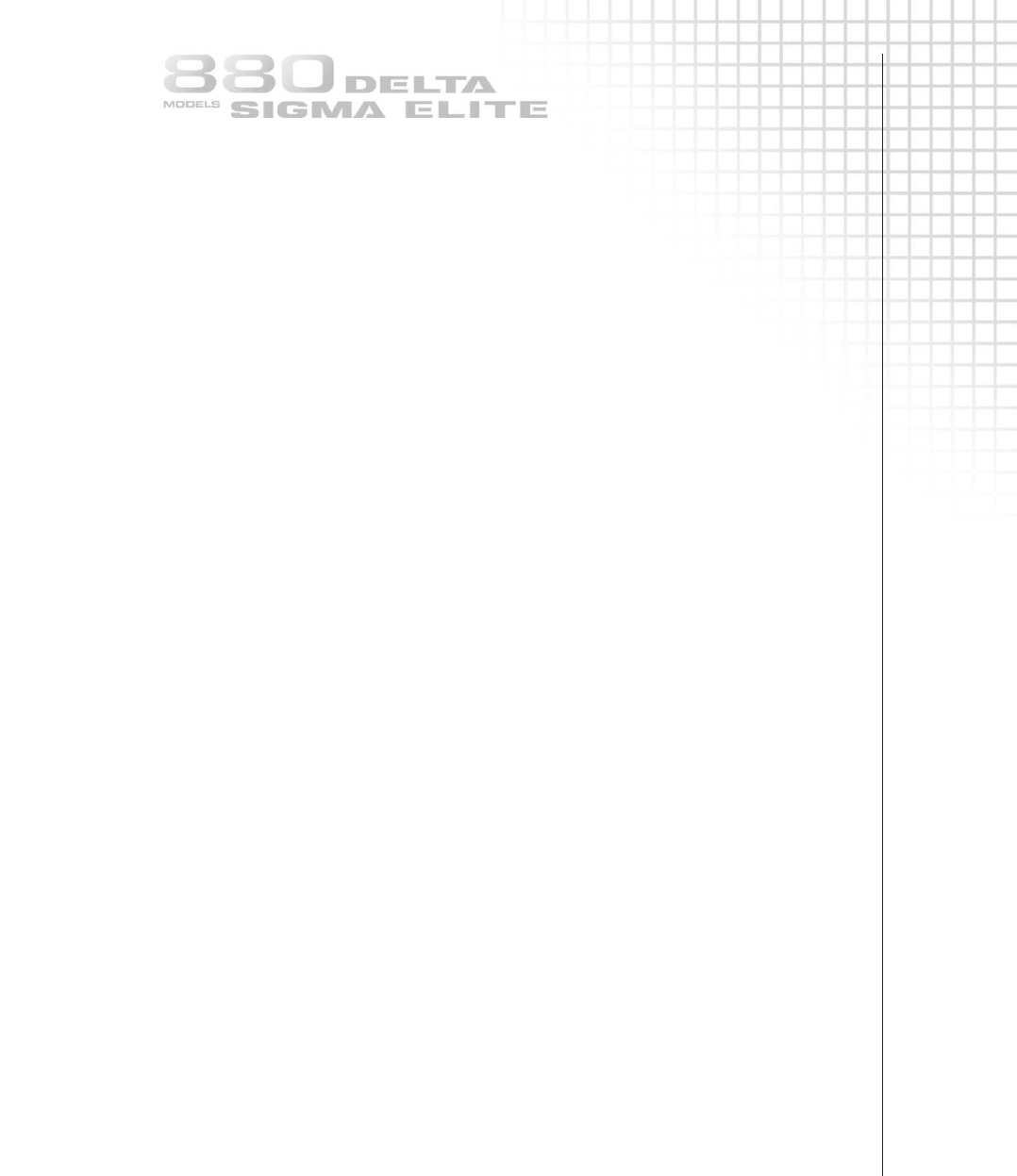
4.11
MAINTENANCE INSTRUCTIONS
7 Perform the following inspections of the control cable.
Use the Model 550 NO GO gauge to inspect the control cable connector for wear. Closely
inspect the connector for bends or cracks in the neck (shank) area and dented areas on the
ball of the connector. Remove the control cable from service if any cracks or bends in the
shank or dents in the ball of the male connector are found during this inspection. The male
connector should not be bent at an angle greater than 15 degrees from the axis of the
control cable in the area where it is crimped. Using your hands, attempt to twist or rotate
the male connector off the control cable. If any movement is possible during this test,
the control cable must be removed from service and the male connector must be replaced.
Carefully inspect the control cable directly behind the remote control cable connector
and approximately 12in (305mm) beyond the male connector looking for the
following anomalies:
●
Cuts, breaks, nicks or fraying in the spiral windings of the cable.
●
Kinks or permanent bends.
●
Rust (red oxide) on the inner and outer core of the cable.
●
Uniformity of the spacing between the outer helical windings of the cable.
Check for flattened areas and excessive wear that reduces the cable's outer
diameter less than 0.183in (4.7mm).
●
Perform a flexibility (spring) test of the cable by bending the connector end
of the cable into a ‘U’ shape and then releasing it. A cable that is bent/released and
does not spring back into an essentially straight shape is indicative of internal
corrosion of the cable. The cable must be removed from service.
●
Carefully examine the cable in the area of the control crank assembly looking for
cuts, breaks, fraying, rust, unusual stiffness and uniformity of the spacing between
the outer spiral windings.
●
Examine the entire length of cable looking for defects described above.
If a control cable is deemed as defective during this inspection, remove it from service and
tag it with a label to prevent inadvertent use.
The control cable (Model 550 male) connector must be replaced at intervals not to exceed
five (5) years. Maintenance program administrators must maintain traceability records for
replacement of all ‘Safety Class A’ designated components.
8 Lightly lubricate the control cable using MIL-G-23827B or C, MIL-PRF-23827C grease or
equivalent. Apply additional grease to the first 3ft (approximately 1m) of control cable
(male connector end).
9 Clean the exterior of the remote control conduits using clean rags and a detergent.
Remove all dirt and grease from the yellow polyvinyl conduits and swaged fittings.
Carefully inspect the entire length of remote control conduits for cuts and melted areas.
Repairs to cut or melted areas can accomplished by taping the area with 3M™ yellow
polyvinyl tape (or black polyvinyl electrical tape). The tape will prevent the ingress of water
and other liquid that would cause corrosion of the remote control conduit's inner braids and
the remote control cable. Look and feel for dents and depressions in the remote control
conduits. Minor dents can be rounded out by gently tapping the area with a small hammer.
Examine the control conduits where they protrude from the swage fittings, looking for
bulges or cracks in the polyvinyl. Remote control conduits with large dented areas or
cracks/ bulges near the swage fittings should be sent to the manufacturer for repairs.