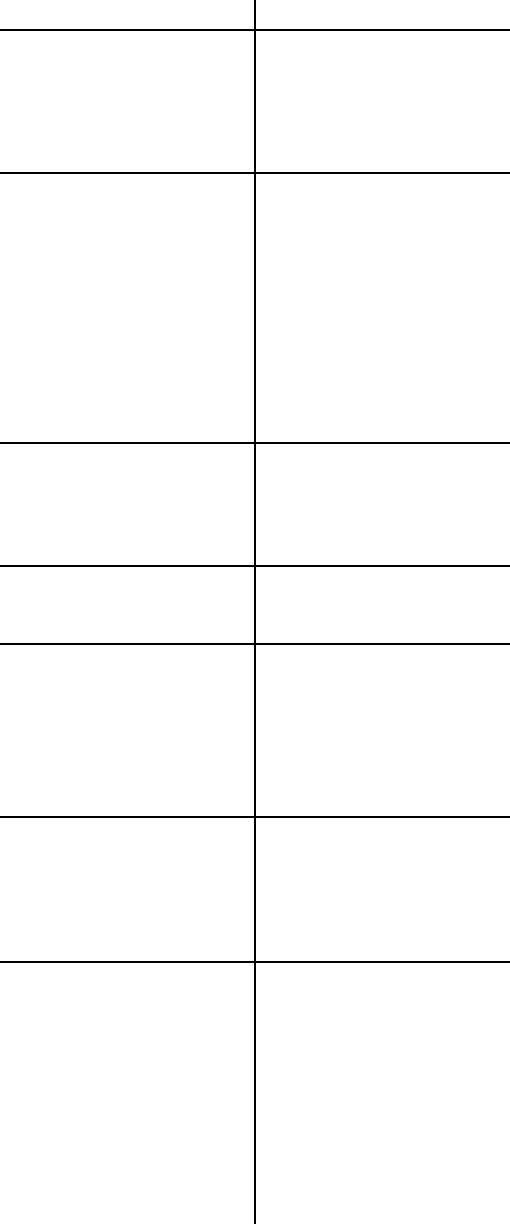
Instruction Leaflet
30-471 (E)
Page 14
Trouble Shooting Guide
Symptoms
• refusal to re-transfer to normal
source upon restoration
• will not transfer to emergency
source upon failure of normal
source
• transfer without a power failure
in the normal source
• no time delay when there
should be
• engine-generator starts when
the normal source has not
failed
• normal source has failed and
the transfer switch cycles
without stopping in emergency
• if the power is not available on
the load terminals with either
the normal or emergency
sources available and the
transfer switch will not operate
Possible Causes
• a voltage sensing relay did not
energize
• emergency to normal time delay
relay has failed
• a loose control connection
• engine-generator did not start
• generator not producing enough
voltage at a high enough
frequency
• a loose control connection
• normal to emergency time
delay, if supplied, has failed
• if voltage sensing modules
supplied in emergency, there
may be a failure of one
• a voltage sensing module has
failed
• emergency to normal time delay
has failed
• that particular time delay has
failed
• the engine start time delay has
failed
• a plant exerciser has been built
into the system
• a voltage sensing module has
failed
• the operating cam in the
mechanism has either broken
or come out of the breaker
handle
• ELS has failed to operate
• the breakers may be complete
with trip units and if there has
been a fault on the system, the
motor circuit has been opened
by either EAS and NAS.
Correct and manually reset the
breakers in the transfer switch
Recommended Maintenance
1. DO NOT perform dielectric tests on the equipment with the control
components in the circuit.
2. DO NOT use loctite.
3. Check lubricant in high speed bearings of the motor and the low
speed bearings of the gear box. For lubrication use Dow Corning
Silicon DC44 or equivalent on the high speed bearings and Aero
Shell No. 6 grease or equivalent in gear box after 5000 operations.
4. Check if control components are tight in sockets.
5. Periodically inspect all terminals (load, line and control) for tightness.
Retighten all bolts, nuts and accessible hardware. Clean or replace
any contact surfaces which are dirty, corroded or pitted.
6. Robonics should be in clean, dry and moderately warm locations. If
signs of moisture are present, dry and clean transfer switch. If there
is corrosion try to clean off, if cleaning is unsuitable replace the
corroded parts. Should dust and/or debris gather on the transfer
switch, brush, vacuum or wipe clean. DO NOT blow dirt into breaker
or terminals.
7. Test the transfer switch operation. While the Robonic is exercising,
check for freedom of movement, hidden dirt or corrosion and any
excessive wear on the mechanical operating parts. Clean, lubricate
or replace parts where necessary.
8. Check all adjustable control components (time delay and voltage
sensing relays) for correct settings.
9. If the type “RO” mechanism is removed be sure that the scribe lines
on the gears are in line. When reassembling the drive mechanisms
be sure that they are fastened to the correct holes in the frame and
that the breaker handles are between the cam fingers (one breaker
has to be on and the other off).
Note: When servicing logic control, or transformer module, disable the
motor circuit
Type LRO Robonics
CAUTION
DO NOT overtighten the pivot screw inside the operating arm. This
screw was correctly adjusted at the factory to provide low friction
movement of the operating arm without excessive play.
DO NOT overtighten the set screw holding the operating cam on the
motor shaft.