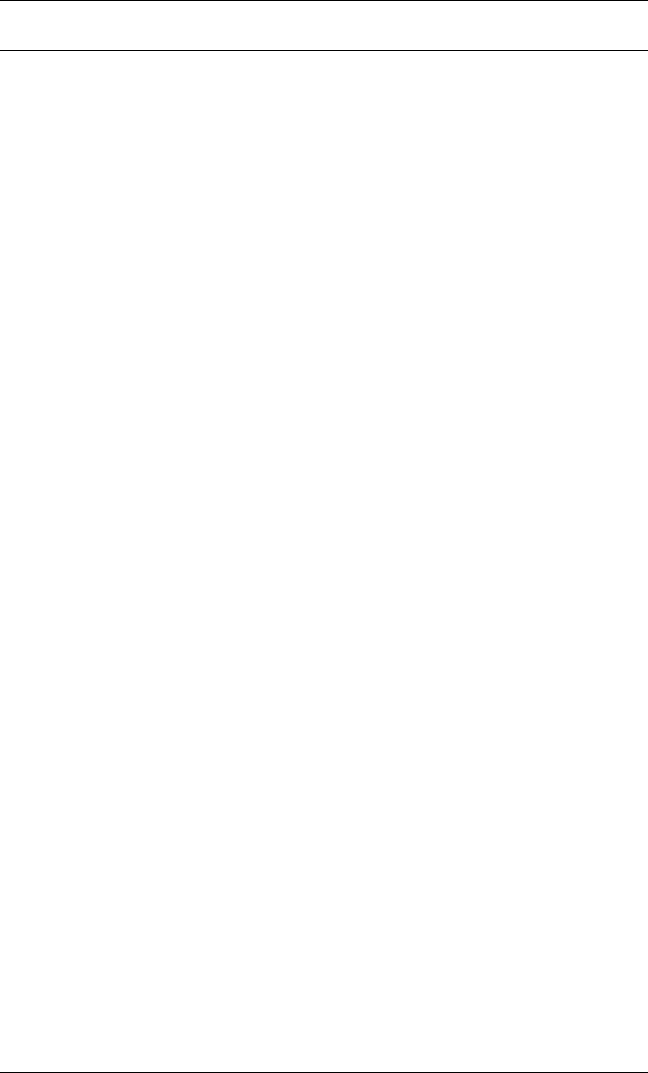
Modbus Communications and Connectivity
19
5.0 MODBUS COMMUNICATIONS AND CONNECTIVITY
This section describes the Modbus communications protocol as sup-
ported by the OpenComms NIC card. It includes information on how
to pass information to and from the OpenComms NIC card via Mod-
bus. It is also intended to help facilitate answering questions regard-
ing supported types, frame format, function code support etc.
5.1 Implementation Basics
Protocol controls the language structure or message format between
devices in other words, the rules for communication. The rules for
communication include how master and slave devices initiate commu-
nications, as well as unit identification, message handling and error
checking. Modbus protocol simply refers to the control of the query
and response cycles between master and slave devices.
The OpenComms NIC module is configured to act as a slave device on
a common network. The common network is a multi-drop or “daisy
chain” configuration over EIA-485, where multiple slaves reside on a
common wire or loop.
5.1.1 Constraints
The OpenComms NIC communicates with local database and there-
fore is subject to the time delay resulting from the local database
updating policies. Use of “Preset Multiple Holding Registers” and
“Preset a single Holding Register” functions requires accessing the
Liebert device connected and to the OpenComms NIC card database
service. Users should be aware that the Modbus application coexists
with other on-board application servers (HTTP and SNMP specifi-
cally) and competes for the database service and CPU time. This may
lead to uncertainty of responding time of the OpenComms NIC. The
user or third party integrator may have to compensate for the delay
time if HTTP, SNMP and Modbus are going to be utilized simulta-
neously.
5.2 Transmission Format
The OpenComms NIC module supports Modbus RTU (Remote Termi-
nal Unit) transmission modes. The OpenComms NIC communication
rate is fixed at 9600 baud, 8 data bits, No parity, 1 Stop bit. The com-
munication media is fixed using EIA-485 standards.