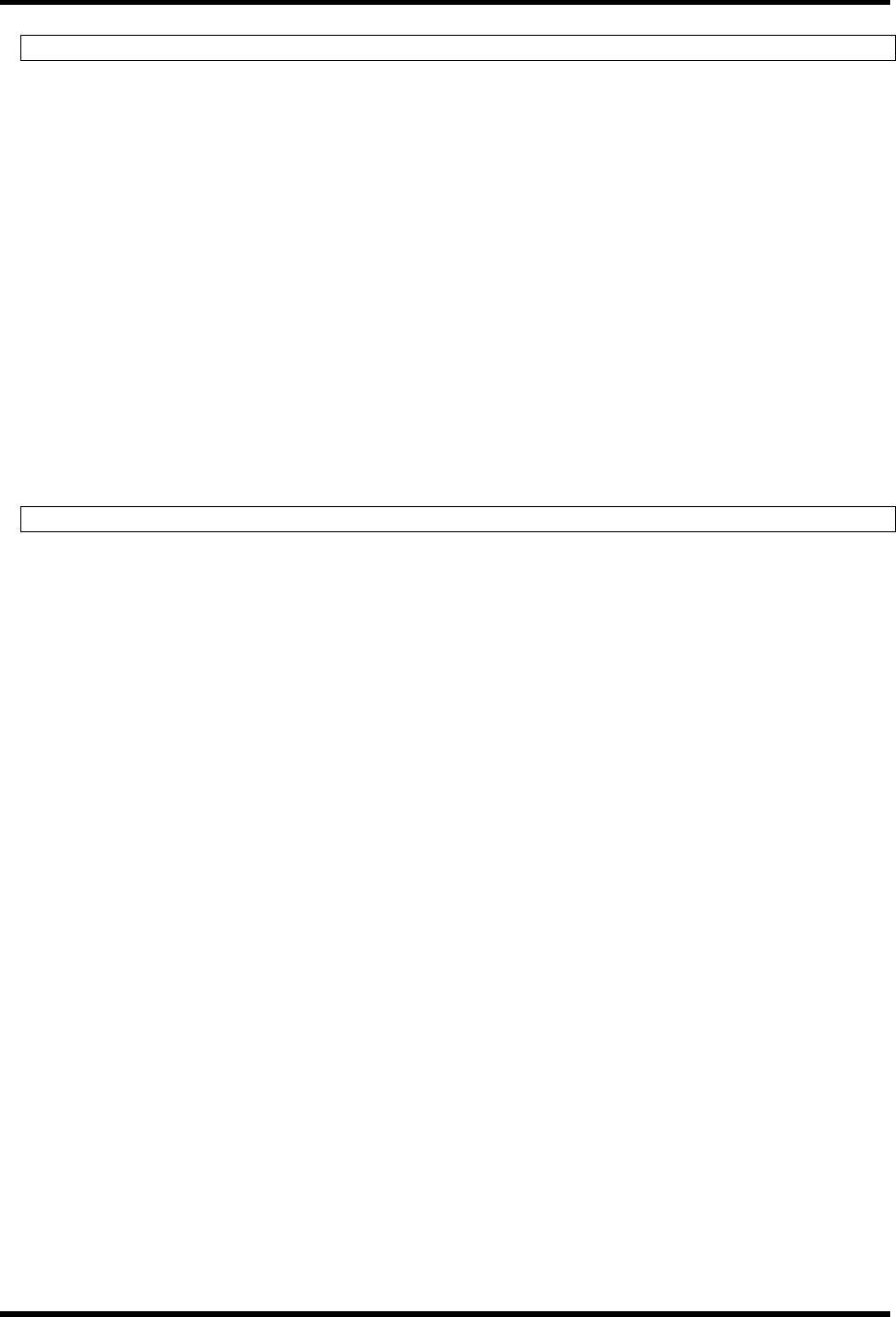
GBC 1264WF/1244WF Operation Manual
© 2006 General Binding Corporation Page 35
SPEED / TEMPERATURE CONTROL
This is only a general reference guide. Different settings may be suitable as the warm up time, lamination time and materials
change.
Factors that may affect the speed and temperature parameters;
1. Image length
2. Image width and ink coverage.
3. Ink coverage
4. Paper type
5. Laminate thickness
6. Operating environment
7. Condition of the rollers
8. Line voltage (effects heaters)
9. Using cooling features.
You may have to adjust temperature or speed depending on stock finish, thickness *Turn heat off when not in use.
THE ART OF LAMINATION
BASIC RULES
Do not attempt to laminate abrasive or metal Objects such as staples, paper clips and glitter, as they may damage the
heat or pull rollers.
Do not force items into the nip area of the heat rollers. An item that is not easily drawn into the laminator by the heat
rollers is probably too thick to laminate.
Wrinkles may result if an attempt is made to reposition an item once it has been grasped by the heat rollers.
Do not stop the laminator before an item has completely exited the pull rollers. Even a momentary stop will cause a
mark (heat line) on the laminated item.
Good, consistent lamination is a result of combining proper heat, tension and dwell time. Dwell time is controlled by the speed of
the motor and is defined as the amount of time the material to be laminated is compressed between the heat rollers.
As a general rule, thicker items and film need to run at slower speeds because they extract more heat from the rollers at a quicker
rate. Setting the speed control at slower settings gives the laminator longer dwell time thus allowing proper lamination of thick
items. Thinner items, such as standard copier paper (20 lb. bond) and tissue paper, extract less heat from the rollers and can be
run at faster speeds.
FILM TENSION
Proper film tension, known as brake tension, is the minimum amount required to eliminate wrinkles in the finished item. The film
should be taut. A properly adjusted roll of film should not require excessive force to turn by hand.
Film tension should be enough to introduce a minor amount of drag as the film unrolls. Insufficient tension causes wrinkles,
while too much tension causes stretching (necking). Uneven tensions between the top and bottom rolls create curl. Too much
upper tension creates upward curl while too much bottom tension causes downward curl.
Adjustment of the pull roller clutch may be necessary if after adjusting unwind and rewind brake tensions do not improve your
output quality.