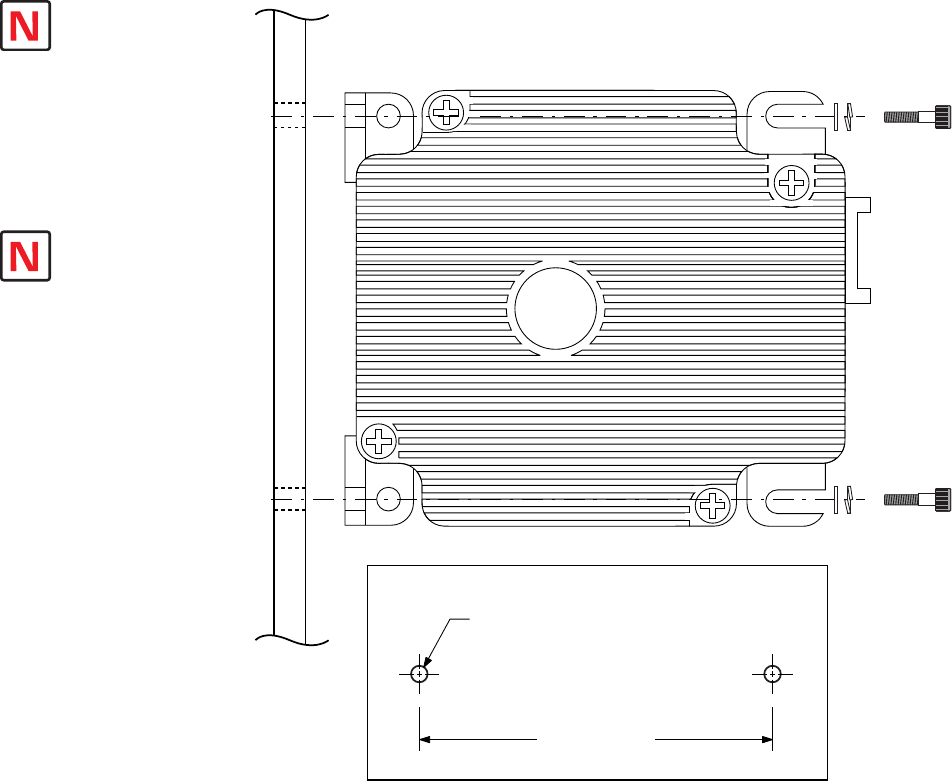
4
Microstepping MForce PowerDrive Manual Revision R040507
Figure 2.1.2: End Mounting the MForce PowerDrive
Securing Power Leads and Logic Leads
Some applications may require that the MForce and/or the connected motor to move with the axis motion. If this
is a requirement of your application, the motor leads must be properly anchored. This will prevent flexing and
tugging which can cause damage at critical connection points on the MForce connectors.
Layout and Interface Guidelines
Logic level cables must not run parallel to power cables. Power cables will introduce noise into the logic level
cables and make your system unreliable.
Logic level cables must be shielded to reduce the chance of EMI induced noise. The shield needs to be grounded at
the signal source to earth. The other end of the shield must not be tied to anything, but allowed to float. This allows
the shield to act as a drain.
Power supply leads to the MForce PowerDrive need to be twisted. If more than one driver is to be connected to
the same power supply, run separate power and ground leads from the supply to each driver.
2 x #8-32 Screw
2 x #8 Split Lockwasher
2 x #8 Flat Washer
Mounting Hardware
2 x M4 - 0.70 Screw
2 x M4 Split Lockwasher
2 x M4 Flat Washer
Mounting Hardware (Metric)
Mounting Surface
3.000 TYP
(76.20 TYP)
Use #29 Drill Size (3.3 mm)
Tap to #8-32 2 PL (M4 - 0.70)
Mounting Hole Pattern
Recommended Tightening Torque:
8 - 9 lb-in (89.6 - 100.8 N-cm)
NOTE: Ensure that
proper clearance is
allowed for wiring
and cabling.
Especially when end
mounting the device.
NOTE: Mounting
Hardware is not
supplied.