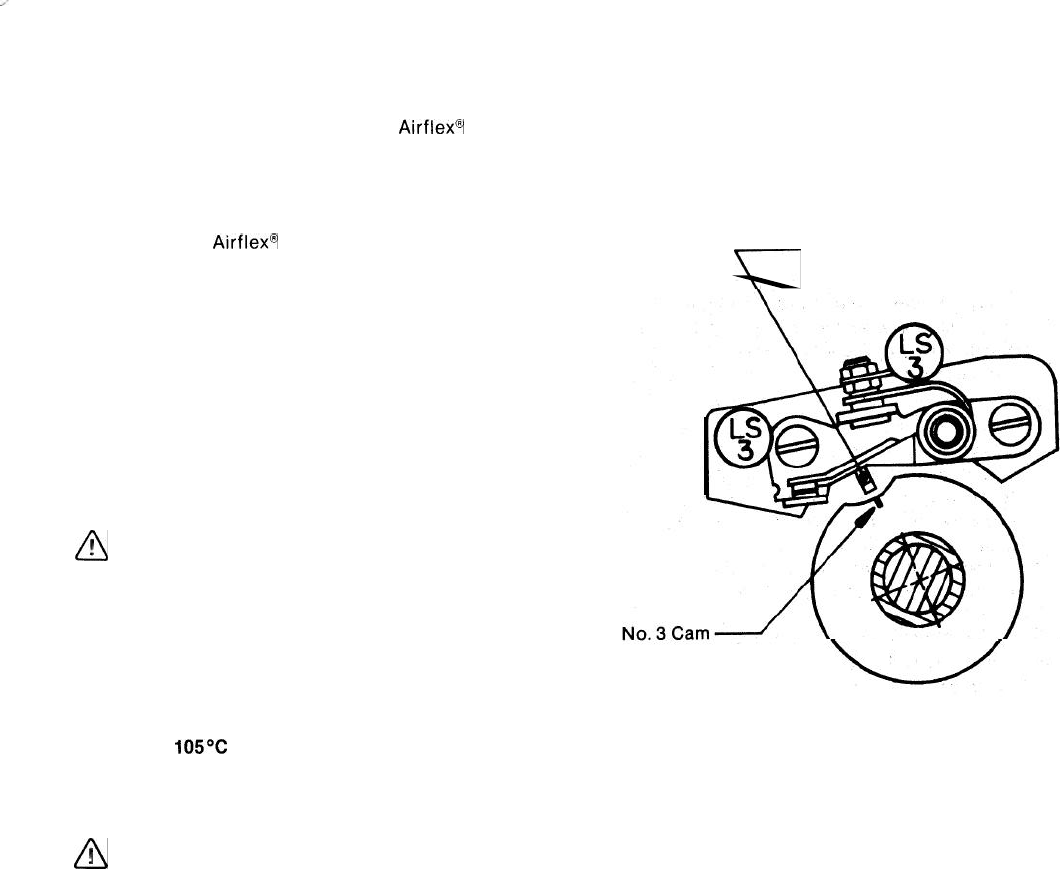
Before mounting the timer, check to be sure
its direction of rotation corresponds to that of
the shaft. Fasten the flange to the shaft with
lockwashers and cap screws.
Refer to appropriate paragraph and mount
second timer.
Wiring instructions are given in Paragraph 2.2.
2.2 Wiring:
Two rotary timers are required in the
Airflex@
press control system. The timers must be
appropriately labeled to identify them and the
functions they control. The timer that
monitors the brake’ should be labeled “A” to
agree with the
Airflex@
wiring diagrams.
Label the other timer “B”. “A” and “B” decals
are furnished on each timer end cap. Remove
the letter that is not used.
The timer is internally wired at the factory. All
leads have the breaker point number to which
they are wired printed on the insulation. Label
each lead with the corresponding schematic
wire number and “A” or “B” to identify the
timer to which the lead is connected.
An insulated straight connector fitting for 3/4
inch flexible conduit is furnished with the timer.
n
!
Caution:
A length of flexible conduit must be used be-
tween the timer and rigid conduit. This flexible
connection allows compensation for any
eccentricity between shafts for shaft mounted
timers and will permit chain tension ad-
justments
for the
foot mounted timers.
Use 16 gauge stranded machine tool wire,
U.L. listed,
105OC
temperature rating, voltage
rating 600 volts, minimum insulation thick-
ness 0.031”, oil resistant, for wiring the timers
to the control panel.
n
!
Caution:
No strain relief is provided internal to the
timer. Therefore, when wiring the timer into
the application, provide enough slack wire to
prevent wire breakage at the contact points.
2.3
Timer Adjustment:
Reread and follow the Hazard Warnings
stated under Paragraph 2.0.
Cams No. 1, 2, 3 insert, 4 and 5 (24, 26, 28, 33
and 33A, respectively) are dowelled together
and are adjusted as a unit. The outer part of
cam No. 3 (28A) in timer “A” is adjusted
separately. All the cams, once adjusted, are
clamped together by tightening of the two jam
nuts (30). See the illustrated parts list in
Section 4.0 for the relationship of these parts
and when making adjustments.
2.3.1. Top Stop and Brake Monitoring
For existing installations: proceed to Step “g”.
a)
Position the crankshaft at top dead center.
Make sure, it will remain in a safe position.
b)
Turn electrical power off to main control
panel.
c)
Remove end cap (31) from timer by remov-
ing the two socket head cap screws.
d)
Loosen jam nuts (30). Hold adjusting
knob (29) and align indicator groove on
cam No. 3 (28A) in timer “A” with fiber
cam follower of LS3 as shown in Figure 4.
No. 3 Breaker Point
Fiber Cam Follower
Indicator Groove
Figure 4. Brake monitoring cam alignment
e)
f)
g)
h)
i)
j)
k)
l)
Retighten the jam nuts (30).
Position felt seal (34), replace end cap
(31), install and tighten the two socket
head cap screws. Turn electrical power on.
Stroke press to check the stopping position.
Note the relationship between the desired
stopping position and the actual stopping
position.
If the stop is unsatisfactory, inch to the
top of the stroke. Secure the machine in a
safe manner to avoid possible injury.
Turn electrical power off and remove end
cap (31).
Loosen jam nuts (30) and rotate adjusting
knob (29) in opposite direction of cam
arrow to advance the stopping position,
or in same direction of cam arrow to retard
the stopping position.
Hold adjusting knob (29) from rotating
and align indicator groove on brake
monitoring cam No. 3 with fiber cam
follower of LS3 as shown in Figure 4.
6