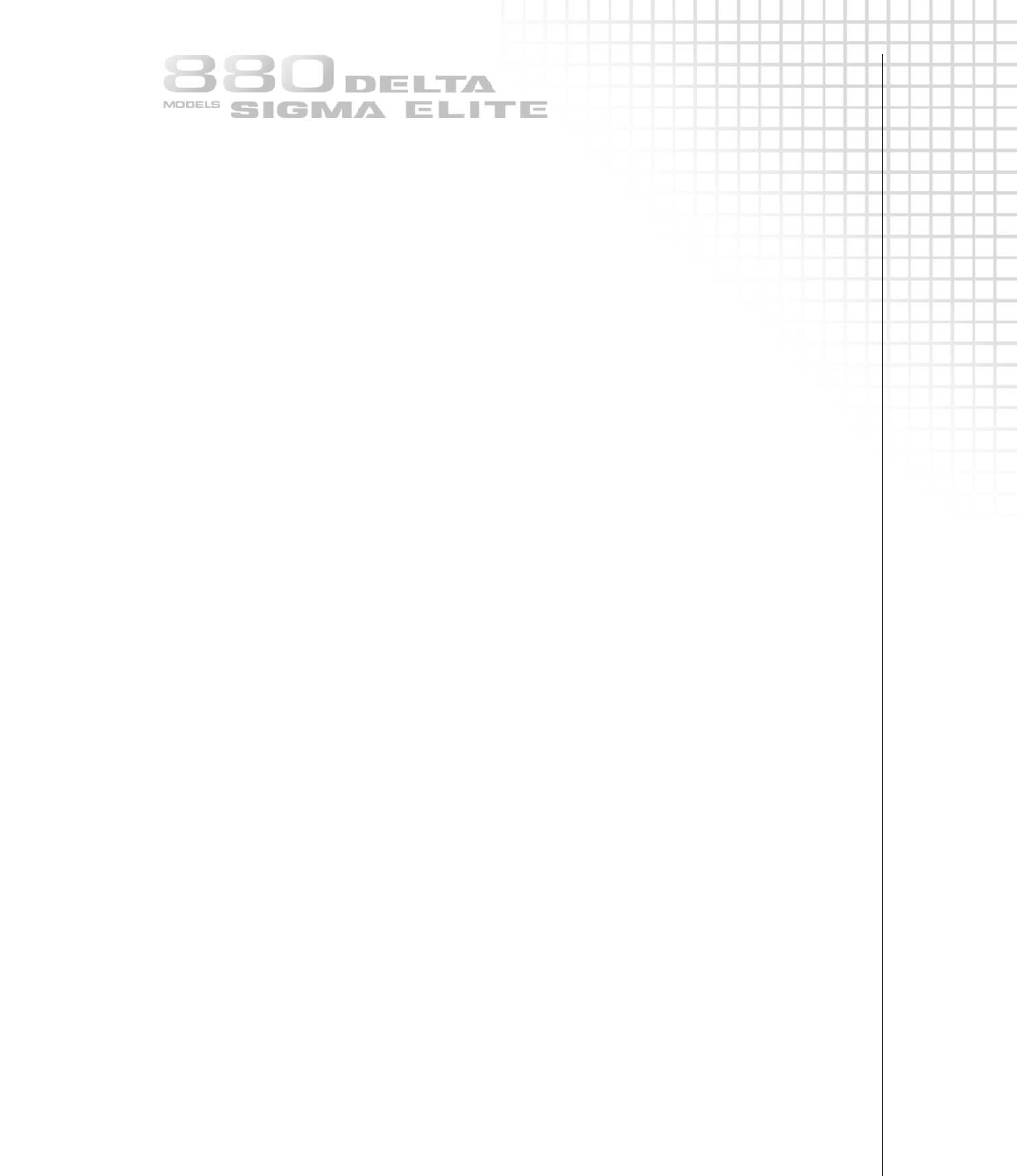
4.15
MAINTENANCE INSTRUCTIONS
Misconnect test after reloading sealed source into the exposure device
After performing the annual maintenance, the complete locking system should be tested
by the maintenance program administrator or Radiation Safety Officer. A misconnect test
on the exposure device including the radioactive source assembly effectively tests the
integrity of the entire locking system. This procedure detects long-term wear (or damage)
of control and locking mechanism components including the control cable and sealed source
connectors simultaneously.
The test should only be performed by personnel that are formally trained, authorized and
thoroughly familiar with annual maintenance procedures. This test is performed by engaging
the remote control connecting plug assembly into the exposure device's locking mechanism
without first engaging the control cable connector within the source assembly connector.
The ability to then rotate the locking mechanism from the CONNECT position towards the
LOCK position indicates critical dimensions of the locking system are excessively worn
to a unsafe condition. Extreme care should be exercised to prevent rotating the locking
mechanism's selector ring beyond the LOCK position. If the locking mechanism and remote
controls fail a misconnect test the equipment must be removed from radiographic
operations. The equipment must not be used until repairs are performed and misconnect
test results are satisfactory.
During the performance of the misconnect test there is a risk of losing control of the
radioactive source assembly if:
●
the components are excessively worn or damaged
●
the person performing the test intentionally or inadvertently rotates the selector ring
from the CONNECT position to the OPERATE position
●
the person performing the test intentionally or inadvertently pushes the lock slide into
the EXPOSURE mode.
Contact an QSA Global service center if you have questions regarding the
misconnect test.
Annual maintenance records
Records of all equipment inspected and maintained during the annual maintenance must
be recorded. Records should indicate:
●
the date of the inspection and maintenance.
●
name of the qualified individual performing the required inspections.
●
problems found and maintenance or repairs performed.
●
model number and serial number of the exposure device.
●
associated equipment that was inspected and maintained.
●
part numbers and associated lot numbers or serial numbers of replacement
parts installed.