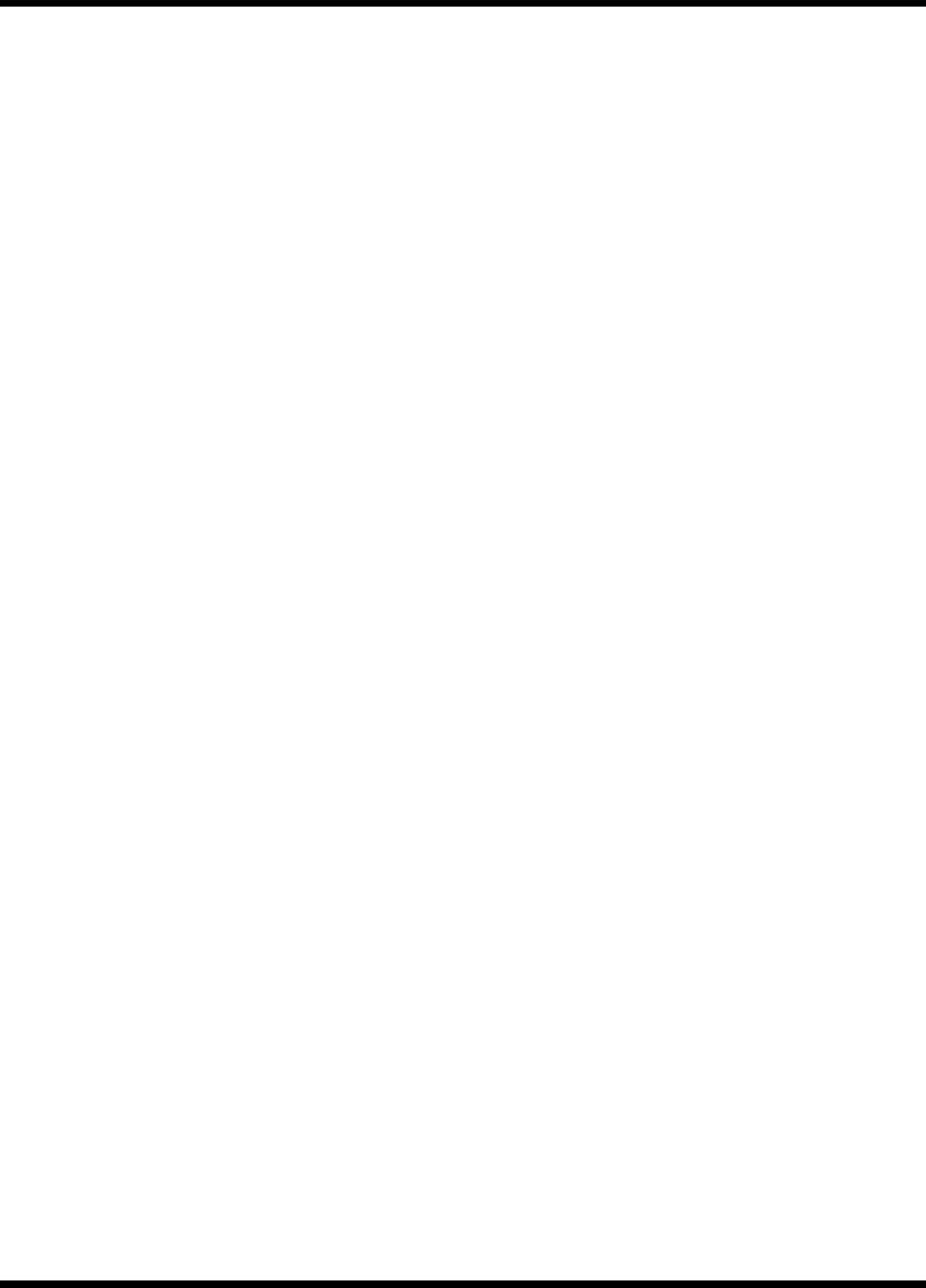
Page 6 - 1
MaintenanceOrca 80-99 Operation and Maintenance Manual
© GBC Films Group June 2000
MAINTENANCE
Introduction
WARNING:
Some maintenance procedures require opening the
cabinets while the power and air are still
connected to the machine.
Because of the potential for electrical shock from
wiring and crushing of fingers or arms in rotating
apparatus, only properly trained personnel should
perform these tasks.
CAUTION:
Never attempt maintenance on an operating
machine unless the instructions specifically call for
it.
GBC Pro-Tech laminators require minimal
maintenance. However, regular maintenance is
essential to keep any piece of precision machinery
at peak performance. The following procedures
are segmented into daily, monthly, biannual, and
as-required procedures.
Daily
1. Clean the Laminating Rolls:
The silicone laminating rolls can be cleaned of dust and
dirt by passing an adhesive-coated board through the
nip. (Of course, the nip should be set for the thickness
of the board used). A mild dishwashing detergent can
also be used to clean the rolls. However a better
procedure is to use isopropyl alcohol and a 100-
percent cotton terry rag.
Samples of these two items were supplied in the
accessory kit shipped with the machine.
Monthly
Setting the Nip:
The gap between the two laminator rolls and the
secondary drive rollers is called the nip or roll nip. It
should be checked once a month. They should be
adjusted according to the following procedures.
Main Roll Nip Setting Procedure:
1. Make sure that the machine has both power and air.
It is also necessary to make sure that the up/down rates
of the upper main roll are even prior to setting the nip; if
not follow the rate adjusting procedure on page 4-2.
Please note that the main rolls have to be cold (room
temperature) when performing this procedure.
2. Remove the shims and set the main roll pressure to
40 psi. Note that this must be done with the upper
main roll in its fully up position.
3. Loosen main roll air cylinder caps and spin them to
their fully up position.
4. Lower the upper main roll and spin down the main
roll air cylinder caps until they are finger tight and
secure.
5. Raise the upper main roll. The main roll nip is now
set.
Pull Roll Nip Setting Procedure:
1. Make sure that the machine has both power and air
and that both cabinets are open. It is also necessary to
make sure that the up/down rates of the upper pull roll
are even prior to setting the nip; if not follow the rate
adjusting procedure on the adjacent column.
2. Remove the shims and set the pull roll pressure to
40 psi. The upper pull roll should be in the fully up
position when making these adjustments.