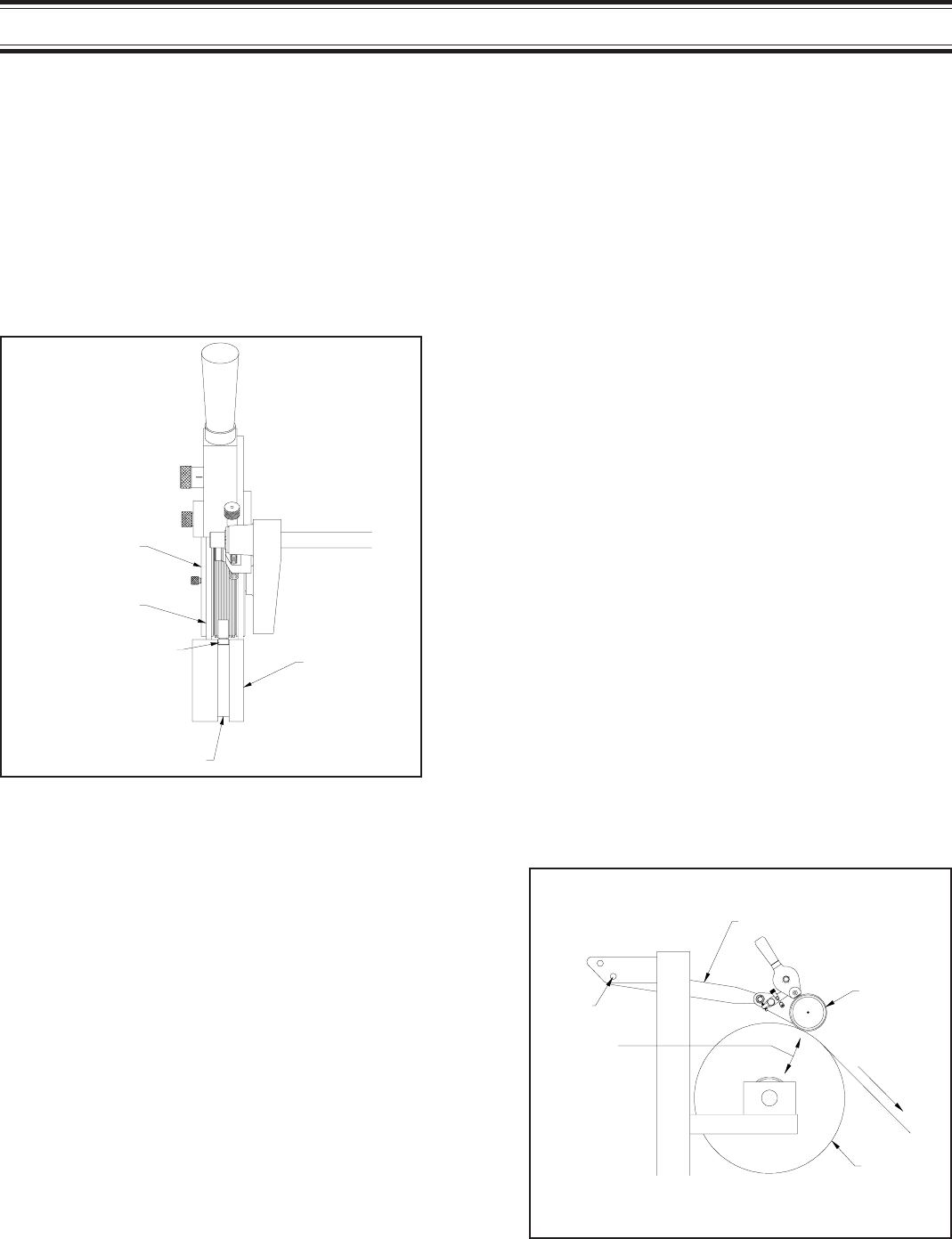
21
WEB PRINTING
Universal Non-Porous Conveyor Line Printers can also be
mounted on custom designed extension arms which will
enable them to print directly on the surface of a master roll
of web material as it is unwound. This technique is fre-
quently used when conveniently positioned idler rolls are
not available. In these applications, as the master roll of
web material decreases in size, the mounting arm pivots
and keeps the print drum in constant contact with the sur-
face of the roll as shown in Figure 37. In these installa-
tions, the weight of the coder is used to supply printing
pressure and typically the standard spring tension mecha-
nism and mounting column are removed. Custom mount-
ing brackets and extension arms should be carefully de-
signed to keep the coder in an acceptable attitude when
printing on a full roll of film all the way down to the smaller
diameter of the core. For more details on custom mount-
ing systems, contact our engineering department.
DO NOT INSTALL A 4 oz. RESERVOIR INK CARTRIDGE AT THIS TIME. The coder is designed to print using
the ink contained in the pre-inked ink roll. Since a freshly saturated Ink Roll was just installed on the coder, the
system will have plenty of ink. Installing a 4 oz. Reservoir Ink Cartridge immediately will result in over saturation
of the ink roll and flooding of the Inking System. The 4 oz. Reservoir Ink Cartridge should not be installed until
most of the ink is consumed from the ink roll and the print quality shows signs that more ink is needed.
SPECIAL WEB PRINTING APPLICATIONS
In applications where the web material is too narrow for both friction drive bearers to contact the surface of the
web, contact with one friction bearer is acceptable. When the web is too narrow for even one friction bearer to
contact the web and still position the print as necessary, a custom made guide roller can often be utilized.
PRINTING ON NARROW WEB MATERIALS
Using this approach, the guide roll must be machined with
a groove which will not only accurately guide the web mate-
rial and drive the guide roll but it must also keep the surface
of the web material flush with the surface of the guide roll
where the friction bearers make contact. (See Figure 36.)
This method of mounting is generally more appropriate when
the web material is extruded rubber or some similar mate-
rial which has a high coefficient of friction since it must drive
both the guide roll and the print drum. Using a custom guide
roller which is driven by an external power source is cer-
tainly acceptable but it is generally rather costly since the
surface speed of the guide roller must precisely match the
speed of the web or smeared prints will result.
PRINTING DIRECTLY ON MASTER ROLLS
FIGURE 36
FRICTION
BEARER
NARROW
WEB MATERIAL
GROOVE
MODIFIED
GUIDE
ROLLER
PRINT
DRUM
AL
FIGURE 37
PIVOT
POST
EXTENSION ARM
CODER
MASTER
ROLL
WEB TRAVEL
CODER
TRAVEL