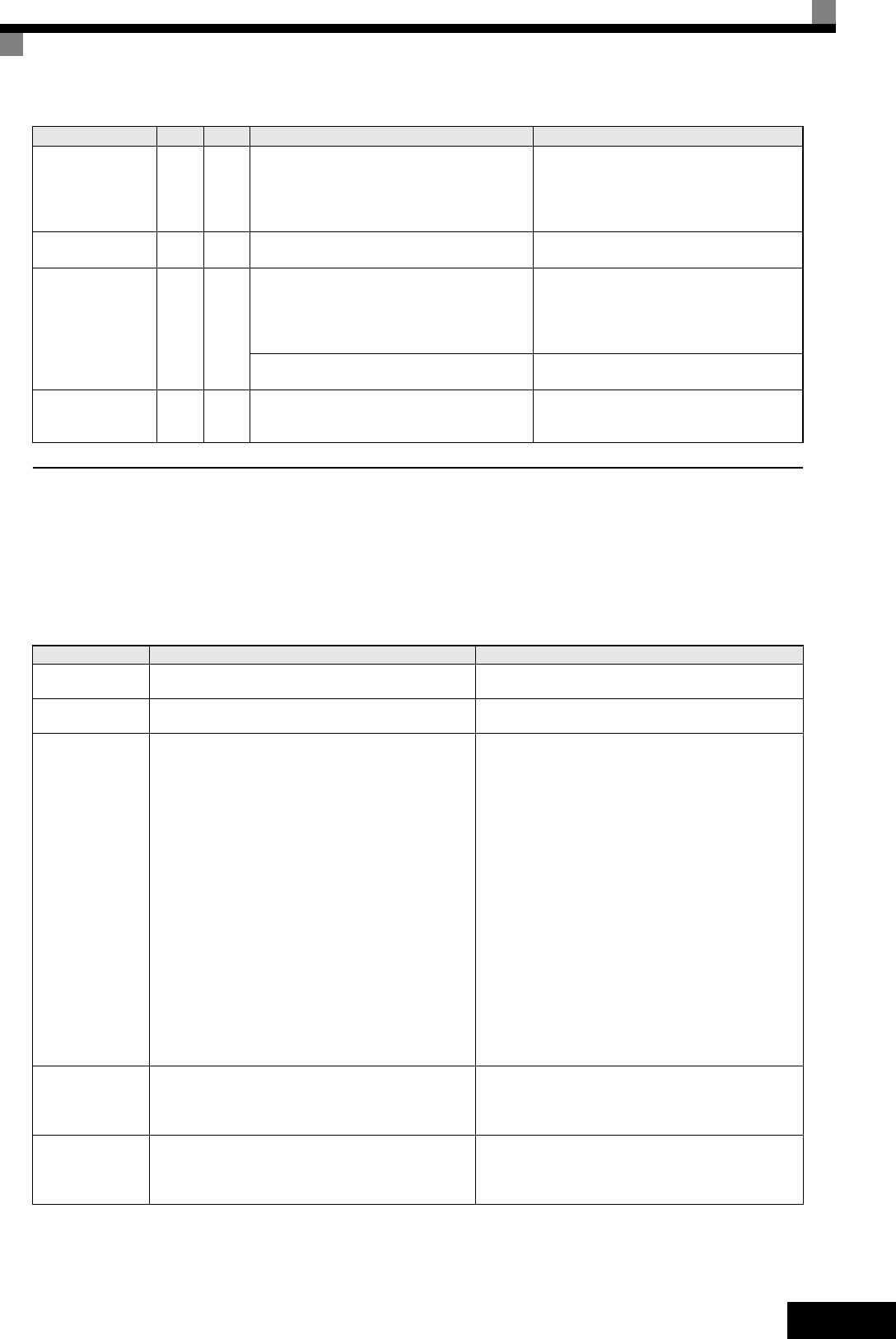
EN-23
Operator Programming Errors
An Operator Programming Error (OPE) occurs when two or more parameter related to each other
are set inappropriately or an individual parameter setting is incorrect. The Inverter does not operate
until the parameter setting is corrected; however, no other alarm or fault output will occur. If an OPE
occurs, change the related parameter by checking the cause shown in the table below. When an
OPE error is displayed, press the ENTER key to see U1-34 (OPE Detected). This monitor displays
the parameter that is causing the OPE error.
PUF
DC Bus Fuse Open
DC Bus Fuse Open
The fuse in the main circuit is blown.
Warning:
PG (encoder) pulses have not been received for
a time longer than the setting in F1-14.
• Check the motor and the motor cables for
short circuits or insulation failures (phase-
to-phase).
• Replace the inverter after correcting the
fault.
RR
DynBrk Transistr
Dynamic Braking Transistor
The built-in dynamic braking transistor failed
• Cycle power to the inverter.
• Replace the inverter.
UV1
DC Bus Undervolt
(only in
stop
condi-
tio)
The DC bus voltage is below the Undervoltage
Detection Level
(L2-05). The default settings are:
200V class: 190 VDC
400 V class: 380 VDC
• Check the input voltage.
• Check the wiring of the input terminals.
• Check the input voltage and the wiring of
the input terminals.
• Extend the settings in C1-01/03
Main Circuit MC Operation Failure
No MC response during Inverter operation.
Replace the Inverter.
UV2
CTL PS Undervolt
Control Power Supply Undervoltage
Undervoltage of the control circuit while the
Inverter was running.
• Remove all connection to the control termi-
nals and cycle the power to the Inverter.
• Replace the Inverter.
Display Meaning Corrective Actions
OPE01
kVA Selection
Inverter kVA Setting Error Enter the correct kVA setting in o2-04.
OPE02
Limit
Parameter setting is out of its range Verify the parameter settings.
OPE03
Terminal
One of the following errors has been made in the multi-
function input (H1-01 to H1-05) settings:
• Duplicate functions were selected.
• UP/DOWN Command(10 and 11) were not selected
simultaneously.
• The up/down commands (10 and 11) and Accel/
Decel Ramp Hold (A) were selected at the same
time.
• More than one of the Speed Search inputs (61, 62,
64) were set simultaneously.
• External Baseblock NO (8) and External Baseblock
NC (9) were selected at the same time.
• The up/down commands (10 and 11) were selected
while PID Control was enabled.
• The Emergency Stop Command NO (15) and NC(17)
are set simultaneously.
• PID is enabled and UP and/or DOWN (10 / 11) com-
mand are set.
• HSB (68) and KEB (65/66) command are set simulta-
neously.
Verify the parameter settings in H1-
OPE05
Sequence Select
RUN/Reference Command Selection Error
The Reference Source Selection b1-01 and/or the RUN
Source Selection parameter b1-02 are set to 3 (option
board) but no option board is installed.
• Verify that the board is installed. Remove the power
supply and re-install the option board again
• Recheck the setting of b1-01 and b1-02
OPE06
PG Opt Missing
Control Method Selection Error
One of the control methods needing a PG feedback
was selected (A1-02 = 1 or 3), but a PG option board is
not installed.
Verify the control method selection in parameter A1-02
and/or the installation of the PG option board.
Display
Alarm Fault
Meaning Corrective Actions