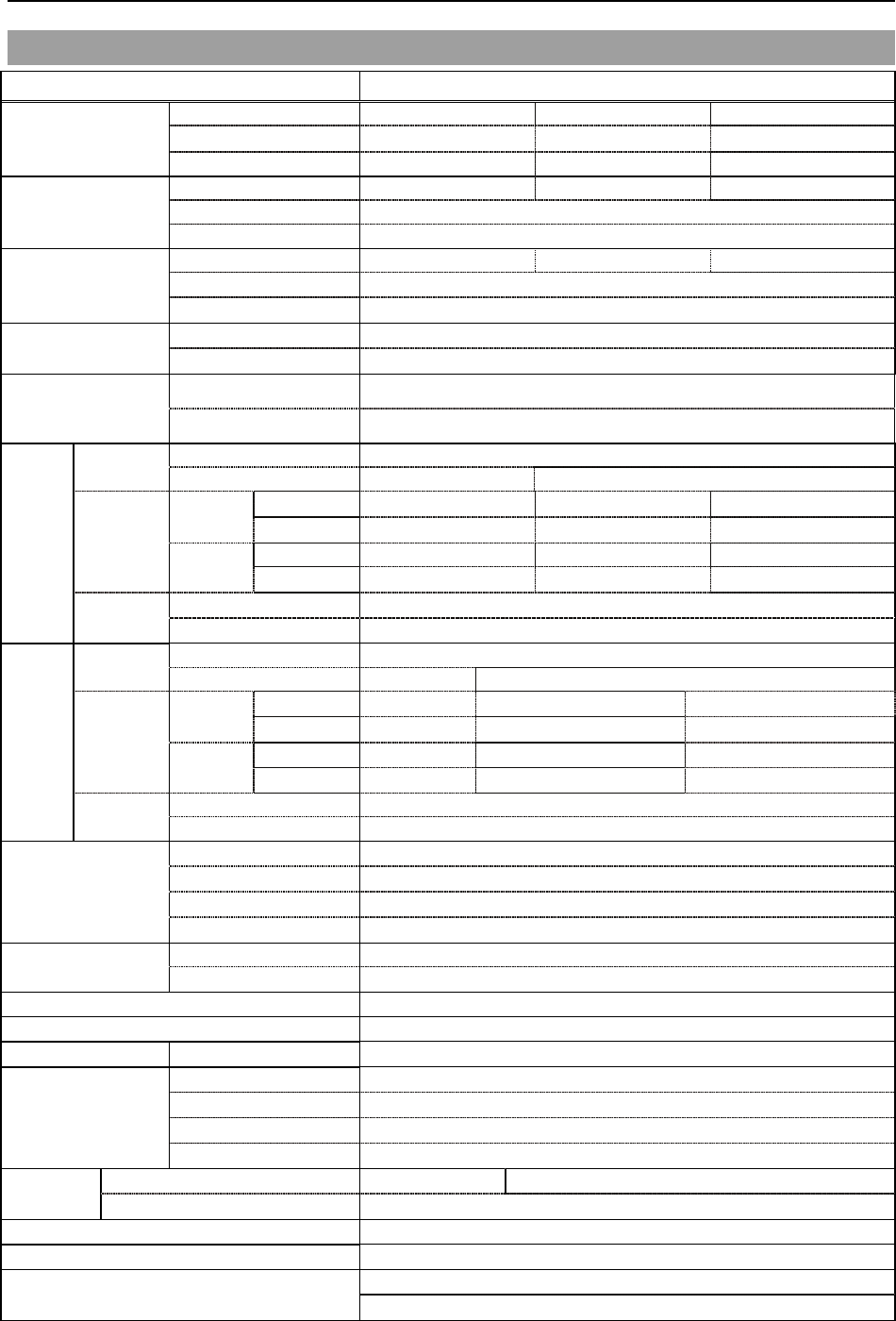
Setup & Operation 2. Specifications
20 G3 Rev.1
2.4 Specifications
Item G3 series Manipulator
Arm #1, #2 250 mm 300 mm 350 mm
Arm #1 120 mm 170 mm 220 mm
Arm length
Arm #2 130 mm 130 mm 130 mm
Joints #1, #2 3550 mm/s 3950 mm/s 4350 mm/s
Joint #3 1100 mm/s
Max. operating
speed *1
Joint #4 3000 deg/s
Joints #1, #2 ± 0.008 mm ± 0.01 mm ± 0.01 mm
Joint #3 ± 0.001 mm Repeatability
Joint #4 ± 0.005 deg
Rated 1 kg
Payload (Load)
Max. 3 kg
Rated 0.005 kg·m
2
Joint #4 allowable
moment of inertia
*2
Max. 0.05 kg·m
2
Joint #1 ± 140
Straight
Joint #2 ± 141 ± 142
Right hand - − 115 to 150 − 105 to 160
Joint #1
Left hand - − 150 to 115 − 160 to 105
Right hand - − 135 to 150 − 120 to 165
Curved
Joint #2
Left hand - − 150 to 135 − 165 to 120
Joint #3 150
Max.
motion
range
Common
Joint #4 ± 360
Joint #1 − 9786710 to 51729750
Straight
Joint #2 ± 20534614 ± 20680249
Right hand - − 5825423 to 55924054 − 3495254 to 58254223
Joint #1
Left hand - − 13981014 to 47768463 − 16311183 to 45438294
Right hand - − 19660800 to 21845334 − 17476267 to 24029867
Curved
Joint #2
Left hand - − 21845334 to 19660800 − 24029867 to 17476267
Joint #3 −13653338 to 0
Max.
pulse
range
Common
Joint #4 ± 23907534
Joints #1
0.00000377134 deg/pulse
Joint #2
0.00000686645 deg/pulse
Joint #3
0.00001098632 mm/pulse
Resolution
Joint #4
0.0001560107deg/pulse
Shaft diameter ø 16 mm
Hand
Through hole ø 11mm
Mounting hole 120 × 120 mm (4-M8)
Weight (cables not included)
14 kg : 31 lb.
Driving method All joints AC servo motor
Joint #1
200 W
Joint #2
150 W
Joint #3
150 W
Motor
energy
consumption
Joint #4
150 W
Installation method
- Multiple Mounting
Option
Installation environment
Cleanroom *3 & ESD
Joint #3 down force 150 N
Installed wire for customer use
15 (15 pin: D-sub) 15 cores
2 pneumatic tubes (ø6 mm) : 0.59 Mpa (6 kgf/cm
2
: 86 psi)
Installed pneumatic
ube for customer use t
1 pneumatic tubes (ø4 mm) : 0.59 Mpa (6 kgf/cm
2
: 86 psi)