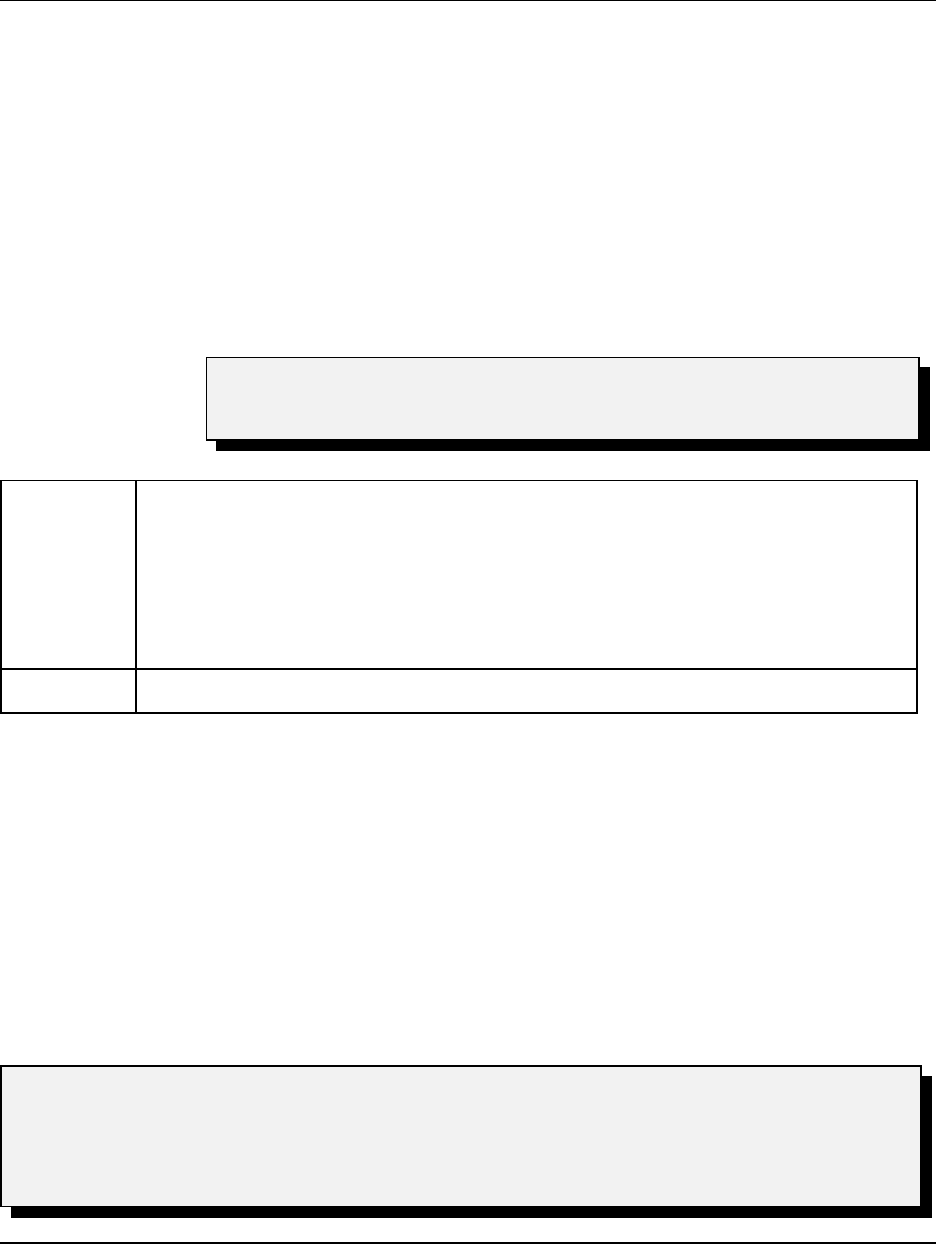
Pressure Systems, Inc. NetScanner™ System (9016, 9021, & 9022) User’s Manual
www.PressureSystems.com
3 - 16
This ‘C’ command (with sub-commands) is available only in
modules that have upgraded to firmware Version 2.24 or later.
NOTE: Avoid confusing this Calibrate command ‘C’ (upper case C) with the
Configure/Control Autonomous Host Streams command ‘c’ (lower case c). Like “c,”
but unlike most other module commands, all sub-commands of this command require a
space between the command id (‘C’) and the first parameter (ii).
CONFIGURE/CONTROL MULTI-POINT CALIBRATION (Command ‘C’)
Purpose: This command is actually four (4) sub-commands. The first configures and starts
a Multi-Point Calibration adjustment function for selected channels in the module.
Another is repeated multiple times to collect data for each defined calibration point.
Another ends the calibration function normally by calculating new offset and gain
adjustment coefficients from the collected data. It then returns the module to its
normal state, but with improved accuracy. A final sub-command is used only if it
becomes necessary to abort the calibration function while in progress. The general
form of all sub-commands is described in the table below. Subsequent pages
separately describe each individual sub-command and give examples of each.
Command “C ii[ dddd]... ”
‘C’ is the command letter.
‘ ii’ is a required sub-command index preceded by a space character.
‘ dddd’ are zero or more optional datum (or parameter) fields, each preceded
by a space character. These vary with the sub-command used.
Response
Depends upon the particular sub-command (ii) used.
Description: The four ‘C’ sub-commands configure and control operation of a Multi-Point
Calibration function that is similar to the simpler re-zero and span calibration
adjustment functions (see separate ‘h’ and ‘Z’ commands). However, ‘C’ adjusts
both the offset and gain correction coefficients of each affected transducer at the
same time, using two or more calibration points. Thus, instead of simply
calculating a new linear (i.e., straight line) adjustment function that passes through
the supplied zero and span calibration points, it calculates a best-fit straight line,
using the least squares method, that comes “as close as possible” to all the
supplied calibration points. This correction method provides the very best
adjustment throughout the entire range (negative to positive) of a differential
transducer.