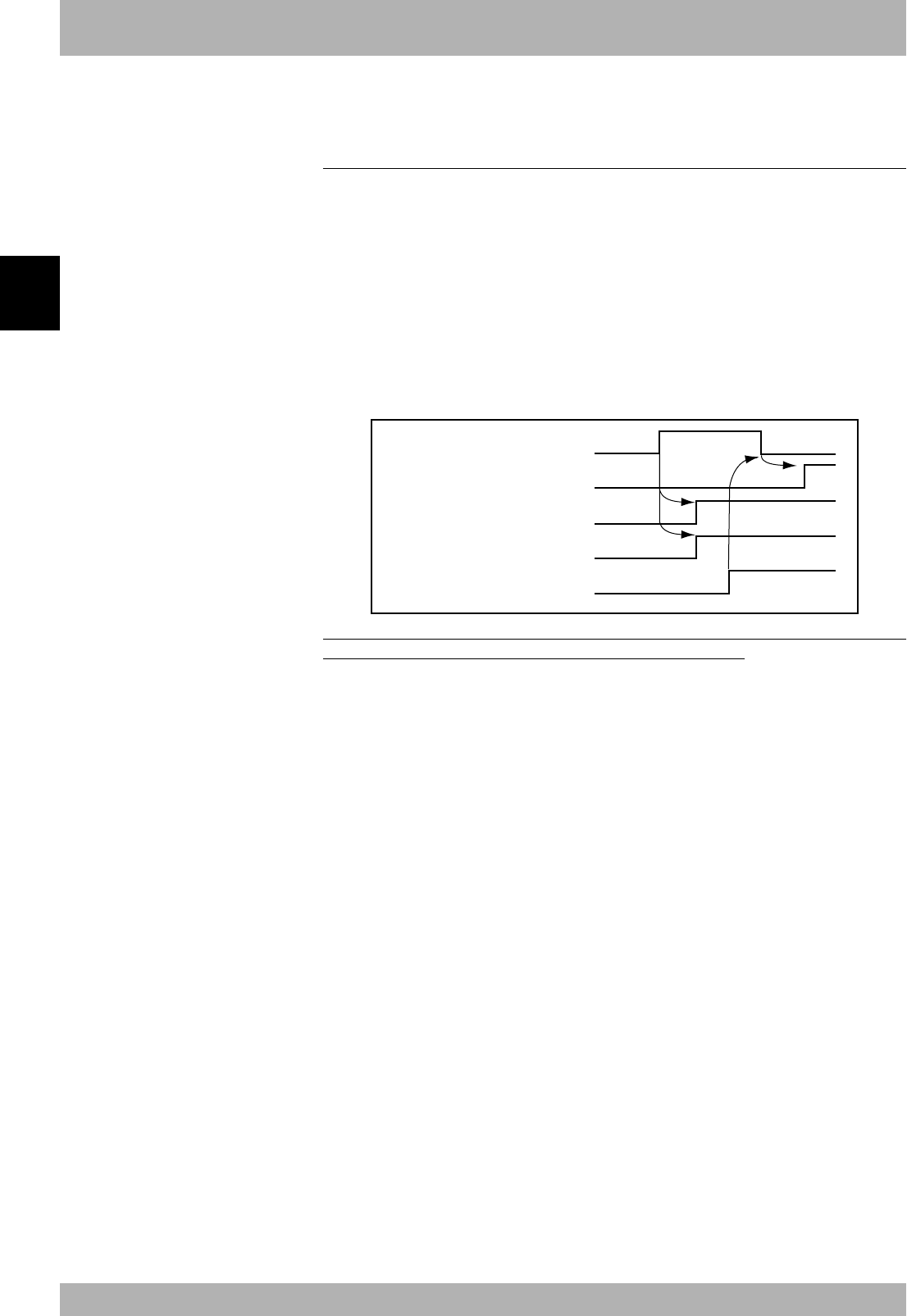
3-2
Communication
3
2. Initial process for connecting to CC-Link system
The initial data process must be carried out to correctly connect to the CC-Link system.
2.1 Initial data process
The initial data process is carried out to confirm that the robot controller is correctly
connected to the CC-Link system. Prepare the process on the master station PLC side so
that the following type of process is always carried out before data is exchanged.
Initial data process (master station PLC side)
q Confirm that RX(n+7)8 (initial data process request flag) is ON.
w Turn RYn0 (emergency stop input) and RYn9 (interlock input) ON.
e Turn RY(n+7)8 (initial data process completion flag) ON.
r Confirm that RX(n+7)8 (initial data process request flag) is OFF.
t Confirm that RX(n+7)B (remote station Ready) is ON.
RX (n+7) 8
on
off
on
off
on
off
on
off
on
off
RYn0
RYn9
RY (n+7) 8
RX (n+7) B
The robot controller internal process will automatically start when the power is
turned ON and the system is returned from an error state.
c
CAUTION
• RX(n+7) B (remote station
Ready) must always be used on
the master station PLC side as the
flag to indicate whether the robot
controller is operating correctly.
• When starting up the system in
the emergency stop state using
RYn0 (emergency stop input),
carry out the initial data process
first, and then turn RYn0
(emergency stop input) OFF. The
robot controller will start up in
the servo OFF state when the
power is turned ON.