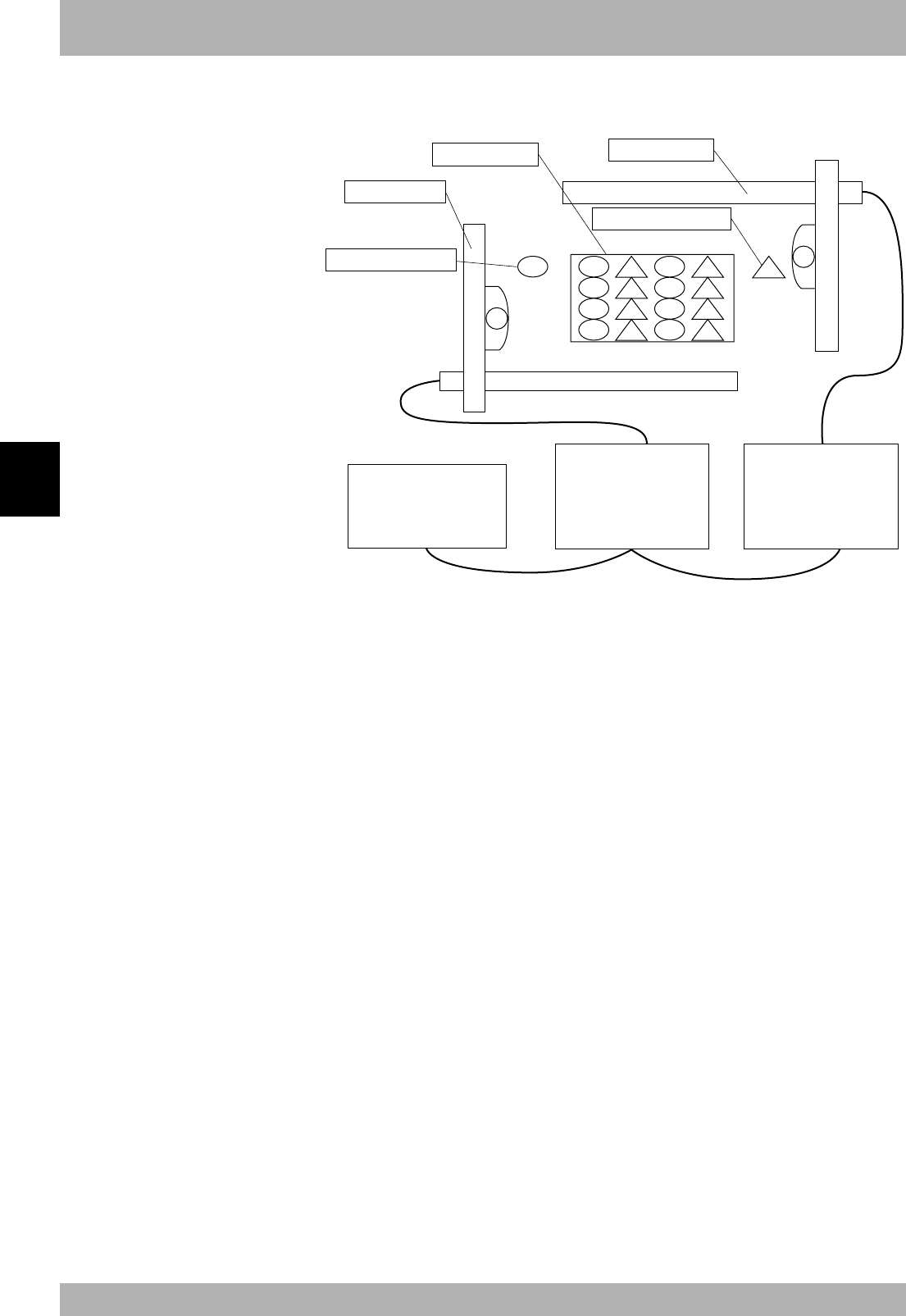
5-10
Specifications
5
4. Sample program
An example for the following type of hardware configuration has been prepared for this
section.
P100
MXYx
2nd unit supply position
Pallet
SXYx
1st unit supply position
Master station
A1SHCPU
+A1SJ61BT11
Remote device station
RCX40 (1st unit)
+ SXYx (3 axes)
(Station No. 1, 4
stations occupied)
Remote device station
RCX142 (2nd unit)
+ MXYx (3 axes)
(Station No. 5, 4
stations occupied)
P101
P102
P103
P104
P201
P202
P203
P204
P105
P106
P107
P108
P205
P206
P207
P208
P200
[Details of sample]
• Pick & place work is carried out using the PLC and RCX40 + SXYx (3 axes),
RCX142+MXYx (3 axes).
• The workpieces supplied to each robot are arranged on one pallet.
• The workpiece is supplied at a rate faster than the robot operation.
• The two robots will interfere above the pallet, so data is exchanged to prevent interfer-
ence.
• When handling the workpiece, the robot moves at a low speed.
• The robot controller directly exchanges the pallet.
* Refer to the robot programming manual for details on the robot program language.
* The PLC circuit is a simple circuit that executes the selected robot program when
emergency stop is canceled.