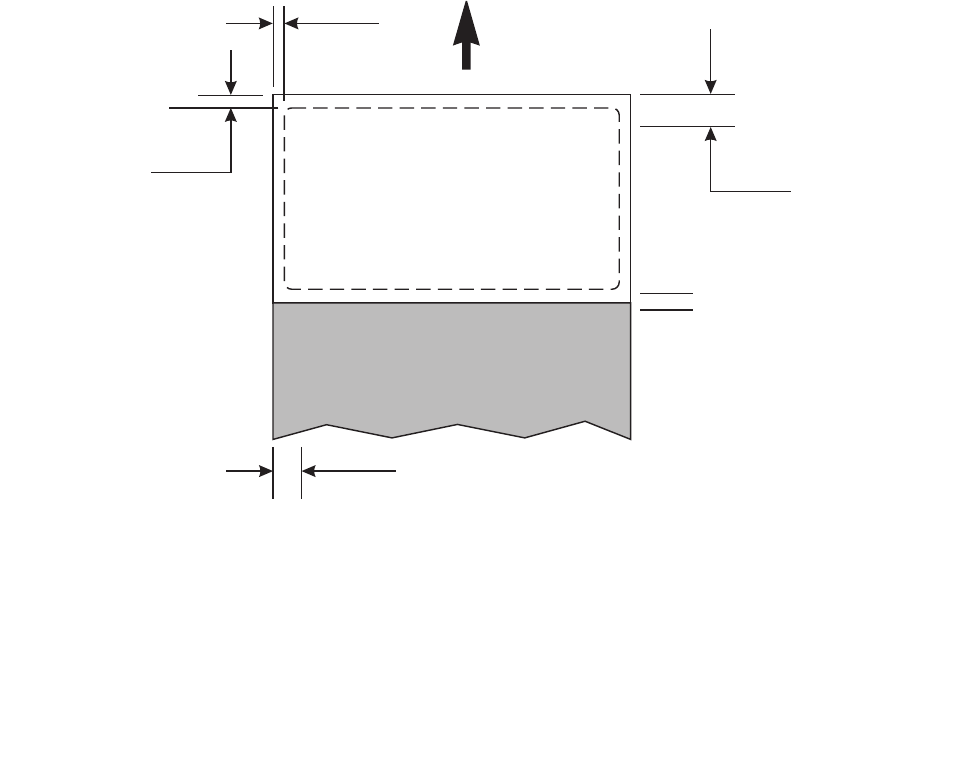
Label Design Guidelines
24
Dual Web Forms
Constructing dual web forms involves joining together rolls of two different materials (usually
pressure sensitive paper and bond paper) and then converting to a cut sheet product. This
construction requires a stripped edge matrix. The liner must be rigid enough to withstand the pick
force of the printer.
The two materials must be thin enough for the sheet to lie flat in the paper tray. Orient the form in the
tray so that the pressure sensitive area feeds into the printer first. The form should have no adhesive
exposed in the overlay area or anywhere along the front or back of the form. We recommend
designing a non-adhesive strip with a minimum width of 1 mm (0.04 in.) along the edges of the
overlay.
To help prevent material from slipping in the fuser, we recommend “knurling,” which roughens up the
exposed silicon area at the glue joint.
See “Figure 5” on page 24 for an illustration of the recommended dual web form design. The
Non-Print Area may vary, depending on the printer model.
The face sheet of a dual web form is usually a paper pressure sensitive product; therefore, the
guidelines for paper labels are applicable to dual web forms.
Figure 5. Design Guidelines, Dual Web Form
1.6 mm
1.6 mm
Leading Edge
(8.5 in.)
0.33 in.
Non-Print Area
Liner Edge
Stripped Edge
0.0625 in.
Reference Edge
(11 in.)
0.0625 in.
Pressure Sensitive
Paper
8.38 mm
Overlay
Non-Print Area
0.25 in.
6.35 mm
(Not drawn to scale)