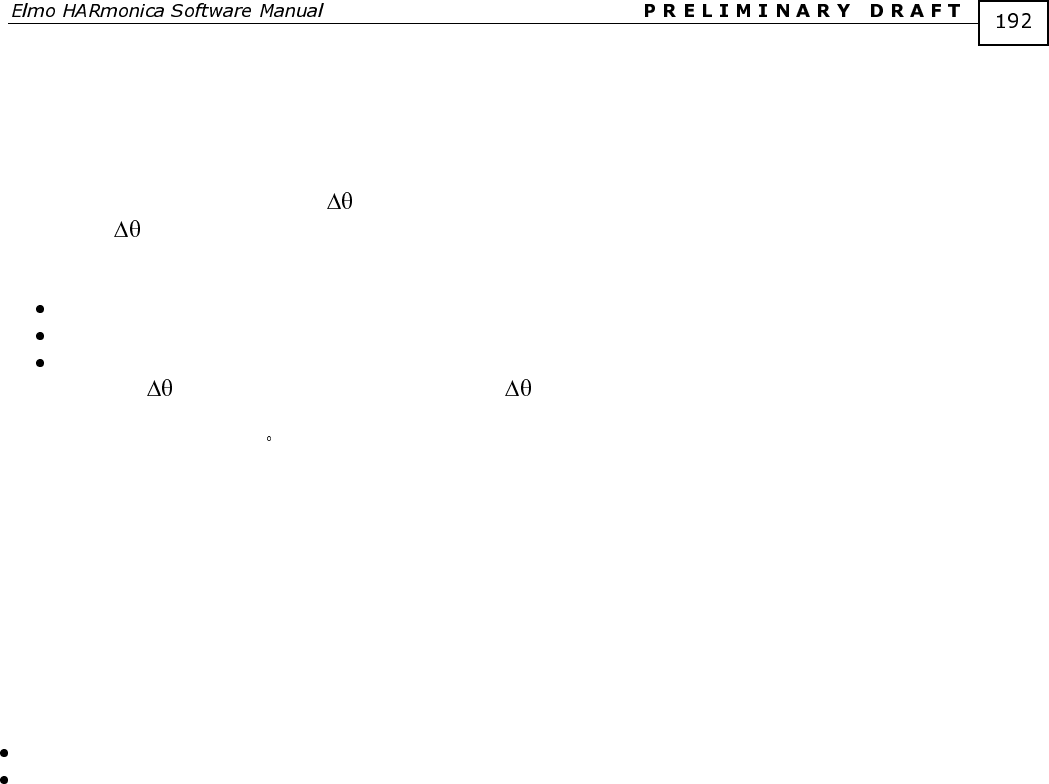
HARSFEN0602
In this situation, the direction of the stator field is constant, and if torque is commanded, the rotor seeks
equilibrium, aligned to the magnetic field.
If the motor is driven by an external speed or position controller, it will be commanded to full-torque, and
dissipate the corresponding heat, without generating any motion.
The commutation is drifting (i.e.
Changes in time):
Drifting in
occur in two forms:
Slow drift:
The following reasons:
Excessive noise on the encoder lines
Damaged or dirty encoder
Wrong encoder resolution setting
Usually drifts
slowly. When the motor is stopped, does not drift at all.
Slow drifting will cause the motor to lose torque gradually until fully stopped at the static
setting of
90±=θ∆ . At this point, the current in the motor will not produce any torque.
The motor shall overheat, but not move.
Fast drift:
Faulty resolver wires cause the resolver to digital converter to elude motion in its full
supported speed. The motor behavior becomes bizarre, normally producing oscillations
without much average torque.
14.11.3 Detection of Commutation Feedback Fault
The detection of commutation faults is according to the sensors present.
Three categories are dealt:
Double sensor systems
Resolver system
Double sensor systems
The situation is the easiest if there are two sensor systems, as happens in encoder + digital
hall systems. In this case, there is a rough commutation estimate available by the digital Hall
sensors, that measure the electrical angle of the motor directly.
Bad correlation between the encoder-accumulated commutation angle and the Hall sensors
angle is a sign of faulty commutation.
If the accumulated commutation angle differs by more than 15 electrical degrees than its
closest value that fits the Hall sensor reading, an error is to be declared. The motor is shut
(MO=0) and MF is set to 0x4. This way an error is decided when the commutation is 15 to
45 degrees wrong.
After the detection of a commutation fault, the motor must be shut down and a proper MF
code set active.
There is no point in trying to stop the motor under control, since we don’t know the
correlation between the motor currents and the resulting torque.
At the next motor starting attempt, the motor will seek commutation again.