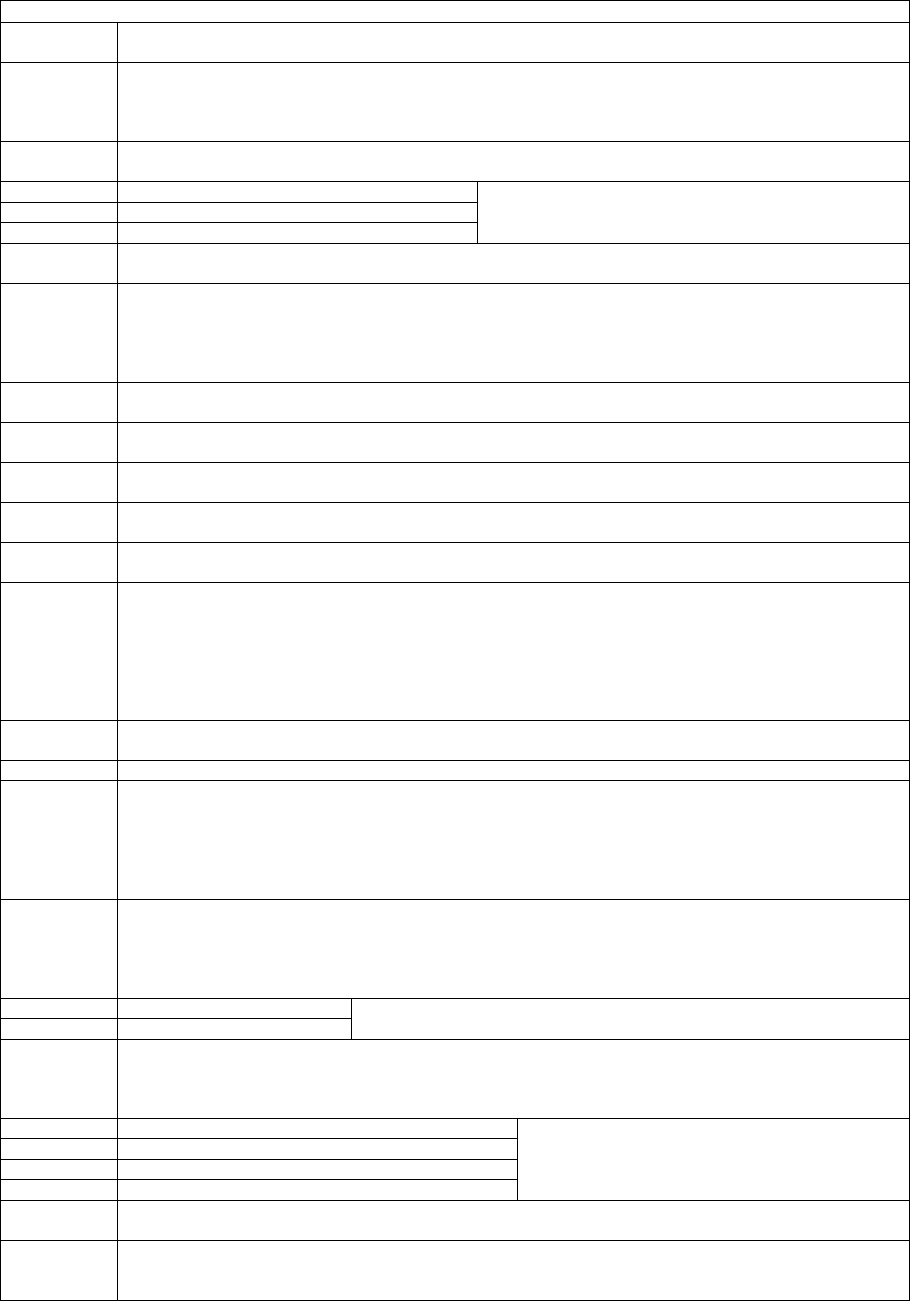
Quattro DC Logic Inputs C2 Submenu
choices
contact cfirm
(Contactor closed) Feedback from an auxiliary contact on the motor contactor. Default is that the drive
expects a normally closed contact to energize the input when the contactor is not pulled in.
ctr pwr sense
(Contactor Power Sensing) Energized when AC power is available to energize the motor contactor.
Power to this circuit is control by elevator relay logic. This circuit must be energized before the drive
will be allowed to start. If power is not available when told to start, or while running, a Fault will occur
for diagnostic purposes.
drive enable
(Drive Enable) Enables drive to run. This signal must be asserted to permit drive to run. This does not
initiate run, just permits initiation.
extrn fault 1 (External Fault 1) User input fault #1.
extrn fault 2 (External Fault 2) User input fault #2.
extrn fault 3 (External Fault 3) User input fault #3.
Closure of this contact will cause the drive to declare a
fault and perform a fault shutdown.
extrn /flt 4
(External Fault 4) User input fault #4. Opening of this contact will cause the drive to declare a fault and
perform a fault shutdown.
fault reset
(Fault Reset) Asserting this input attempts to reset faults. If the FAULT RESET SRC (C1) switch is set
to EXTERNAL TB, the drive’s fault circuit will be reset when this signal is true. If the FAULT RESET
SRC (C1) switch is set to AUTOMATIC, the drive’s fault circuit will be reset when this signal is true and
the automatic fault reset counter (defined by FLT RESETS/HOUR) will be reset to zero. *This input is
edge sensitive and the fault is reset on the transition from false to true.
field enable
(Field Enable) If FIELD ENA SOURCE (C1) switch is set to EXTERNAL TB, the field is enabled when
this signal is true.
low gain sel
(Low Gain Select) If the HI/LO GAIN SRC (C1) switch is set to EXTERNAL TB, the low gain mode is
chosen for the speed regulator when this signal is true.
mech brk
hold
(Mechanical Brake Hold) Auxiliary contact closures confirming when the mechanical brake is in the hold
mode (engaged).
mech brk pick
(Mechanical Brake Pick) Closure of auxiliary contacts confirming the mechanical brake has been picked
(lifted).
no function
(No Function) When this setting is selected for one of the TB1 input terminals, any logic input
connected to that terminal will have no effect on drive operation.
ospd test src
(Overspeed Test Source) This function works only if the OVRSPEED TEST SRC (C1) switch is set to
EXTERNAL TB. A true signal on this input applies the OVERSPEED MULT to the speed command for
the next run. After the run command has dropped, the drive returns to ‘normal’ mode and must be re-
configured to perform the overspeed function again. The OVERSPEED FLT level is also increased by
the OVERSPEED MULT, allowing the elevator to overspeed without tripping out on an overspeed fault.
NOTE: This input must be taken false then true each time that an overspeed test is run. If the input is
left in the true, it is ignored after the first overspeed test.
pre-trq latch
(Pre-Torque Latch) Closing a contact between this input and ground latches the pre torque command
present on the analog channel #2.
run (Run) If drive is enabled through the DRIVE ENABLE logic input, this function will start drive operation.
run down
(Run Down) If drive is enabled through the DRIVE ENABLE logic input, this function will start drive
operation with negative speed commands.
Note: if both RUN UP and RUN DOWN are true then the run is not recognized.
Note: if DIR CONFIRM (C1) is enabled, this input will not change the polarity of the speed command
and will be used to confirm the polarity of the analog speed command as well as starting the operation
of the drive.
run up
(Run Up) If drive is enabled through the DRIVE ENABLE logic input, this function will start drive
operation with positive speed commands.
Note: if both RUN UP and RUN DOWN are true then the run is not recognized.
Note: if DIR CONFIRM (C1) is enabled, this input is also used to confirm the polarity of the analog
speed command as well as starting the operation of the drive.
s-curve sel 0 Bit 0 of S-curve selection
s-curve sel 1 Bit 1 of S-curve selection
These two bits are used to select one of four s-curve selections. For
more information, see S on page 39. -Curves A2 submenu
ser2 insp ena
(Serial Mode 2 Inspection Enable) Used only with custom serial protocol (mode 2)
Defines the logic input to be used as one of the two sources of inspection run command when using
serial mode 2. This input must be true as well as a comparable inspection run command sent serially
for the drive to run in inspection mode.
step ref b0 Bit 0 of multi-step speed command selection
step ref b1 Bit 1 of multi-step speed command selection
step ref b2 Bit 2 of multi-step speed command selection
step ref b3 Bit 3 of multi-step speed command selection
Four inputs, which must be used together as a 4-
bit command for multi-step speed selection. For
more information, see M
on page 41.
ultistep Ref A3 submenu
trq ramp
down
(Torque Ramp Down Signal) This function works only if the RAMP STOP SEL (C1) switch is set to
RAMP TO STOP and RAMP DOWN EN SRC (C1) is set to EXTERNAL TB.
up/dwn
(Up/Down Signal) This signal is used to change the sign of the speed command. Default is FALSE;
therefore, positive commands are for the up direction and negative speed command are for the down
direction. Making this input true reverses the car’s direction.
Table 1 : Logic Inputs C2 Submenu0
62