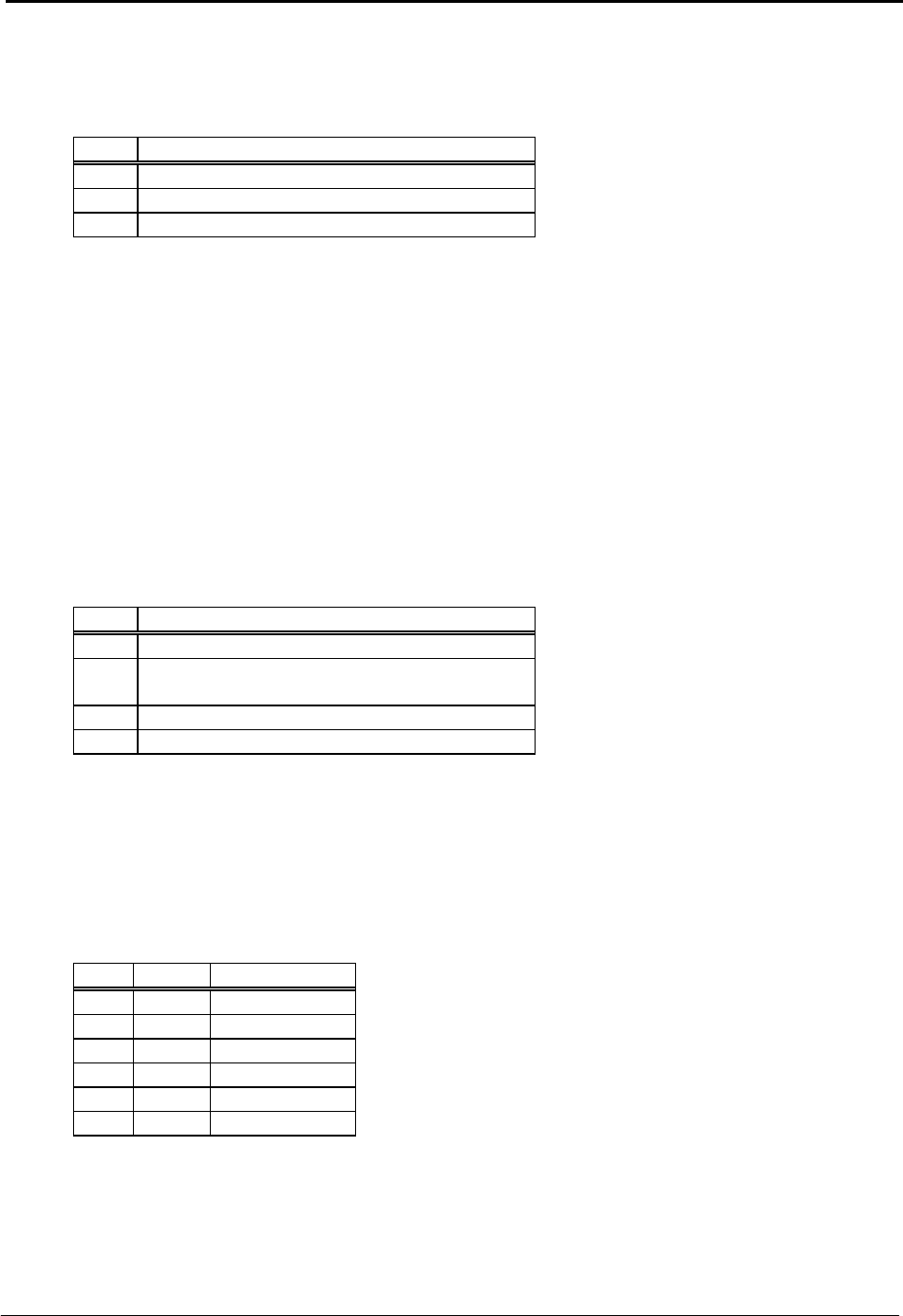
ADVANCED MICRO SYSTEMS, INC. HARDWARE
11
Step and Direction Inputs (J1)
A 10k pull-up resistor allows open-collector circuits to be used. The inputs will withstand in excess of 24
volts.
Pin Signal
6 Ground, common with the power supply input
11 Step pulse input
12 Direction input
The recommended step input is a negative going pulse 5 volt TTL or CMOS.
Encoder Inputs (J1)
Optional encoder circuitry can be specified with the DCB-274-E option. With this option the step input pins
11 and 12 change to industry standard quadrature A and B inputs. The quadrature clocks derived from
optical or magnetic encoders, when applied to the A and B inputs are converted to step and direction
signals. The number of steps per encoder revolution is equal to four times the number of “slots” on the
encoder. The motor will directly follow any changes in the encoder position.
Note: If the encoder produces steps too fast, the step motor can stall if it is physically unable to follow the
abrupt changes in rate and/or direction.
A 10k pull-up resistor allows open-collector circuits to be used. The inputs will withstand in excess of 24
volts.
Pin Signal
6 Ground, common with the power supply input
7 5 volts. Can be used to power an encoder with
low current requirements.
11 Encoder Phase A
12 Encoder Phase B
Power Supply and Motor Connection (J5)
Connector J5 provides the power supply input and motor phase drive outputs. The recommended power
supply is an unregulated DC design with voltage and current ratings, appropriate for the driver. The on-
board 5-volt is for logic power.
For maximum motor speed performance the motor should have a low voltage (higher current, low
inductance) and the power supply voltage as high as possible NEVER exceeding the DCB-274 input ratings.
Pin Signal Type
1 Gnd Ground
2 VMM +24 to 40Vdc
3 PH-3 Phase 2-B
4 PH-2 Phase 2-A
5 PH-1 Phase 1-B
6 PH-0 Phase 1-A