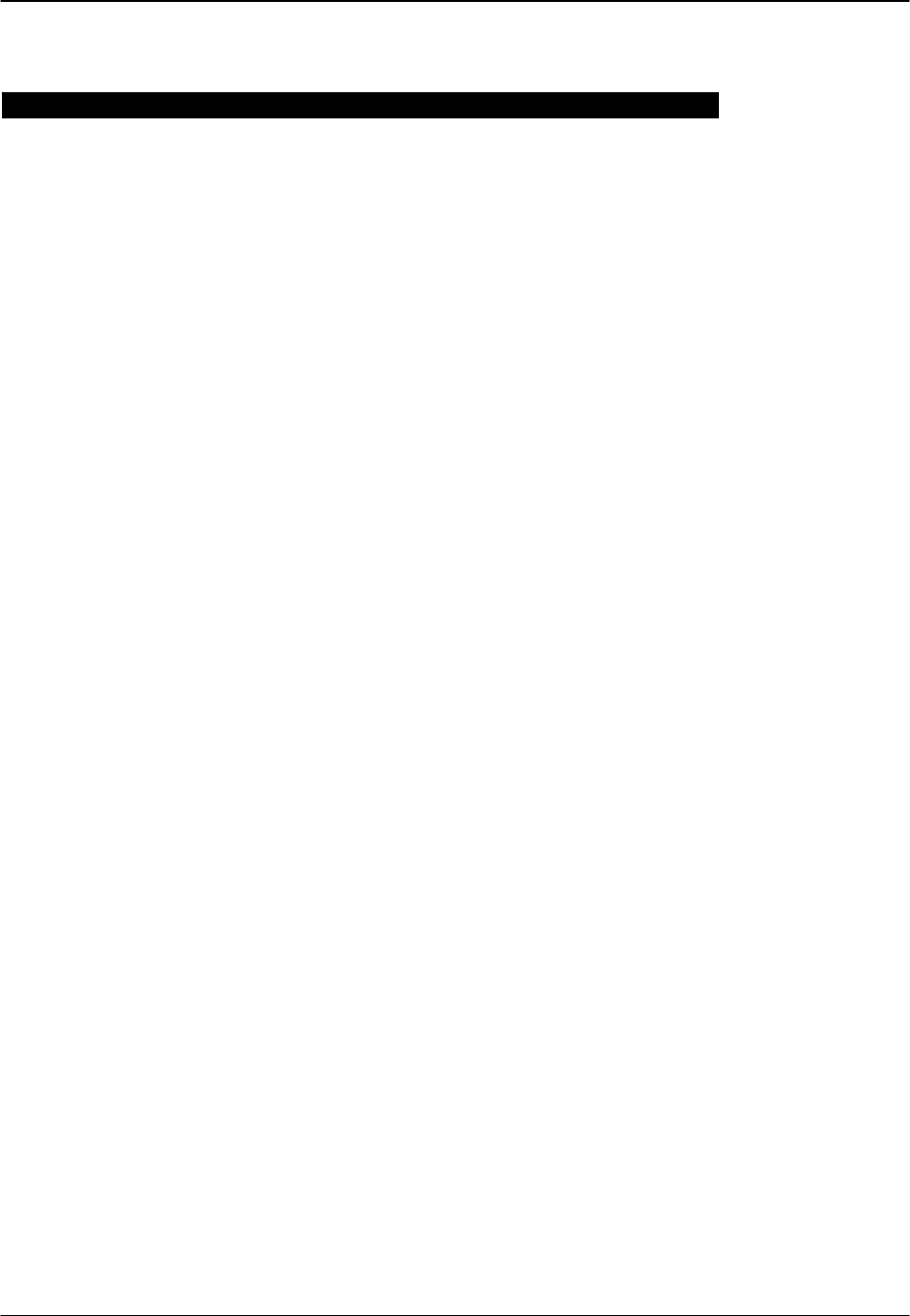
Pressure Systems, Inc. 98RK-1 & 9816 User’s Manual©
Page 100 www.PressureSystems.com
Chapter 4
Calibration
4.1 Introduction
Each individual DH200 transducer within the NetScanner
™
System Intelligent Pressure
Scanner contains nonvolatile read/write memory capable of storing the transducer’s full thermal
and pressure calibration data. The internal firmware of each module reads all of these
calibration data from each transducer upon power up and then dynamically calculates
conversion coefficients that convert transducer output into pressure at the current measured
temperature. The firmware uses these coefficients for all subsequent engineering-unit data
conversions performed.
All NetScanner
™
System Intelligent Pressure Scanner modules use a third-order polynomial to
convert transducer output voltage to pressure. All calculations are carried out internally using
high precision math. The following formula is used for all pressure output calculations.
P
T
(V) = [C
0
(T) + C
1
(T)*V + C
2
(T)*V
2
+ C
3
(T)*V
3
] * C
SPAN
+ C
RZ
where:
P
T
= Calculated applied pressure
V = Transducer output voltage
C
0
(T) .. C
3
(T) = Conversion coefficients generated from calibration data at
temperature T.
C
RZ
= Re-zero adjustment’s “offset" correction coefficient
C
SPAN
= Span adjustment’s “gain” correction coefficient
Since the polynomial’s coefficients are a function of the current temperature, they are
dynamically re-calculated by the module firmware (with other equations) to compensate for each
transducer’s measured temperature change.
Each model 9816 Intelligent Pressure Scanner contains an integral purge/leak check calibration
manifold. Through software commands to each 9816, this valve may be placed in one of four
positions: RUN, CAL, PURGE, or LEAK-CHARGE. (See the Set/Do Operating
Options/Functions (‘w’) command (ii=0C & 12) in Chapter 3, and in particular the Valve
Position Chart at the end of command’s description.) The 98RK-1 contains pneumatic
backplane inputs for CAL (CAL 1-8) and CAL REF. When each module’s internal calibration
valve is placed in the CAL/RE-ZERO position (through software commands), all DH200
transducer pressure inputs are pneumatically connected to the CAL input ports. All DH200
reference inputs are pneumatically connected to the CAL REF input port. The CAL input may
be used to perform on-line zero adjustment of the transducers. This capability virtually
eliminates sensor zero drift error and ensures the highest possible data accuracy. The CAL
input may also be used for DH200 span adjustment calibrations. Span calibration of multi-range
scanners may also utilize the CAL 1-8 ports if the highest applied pressure does not exceed the
proof pressure rating of any installed transducer.