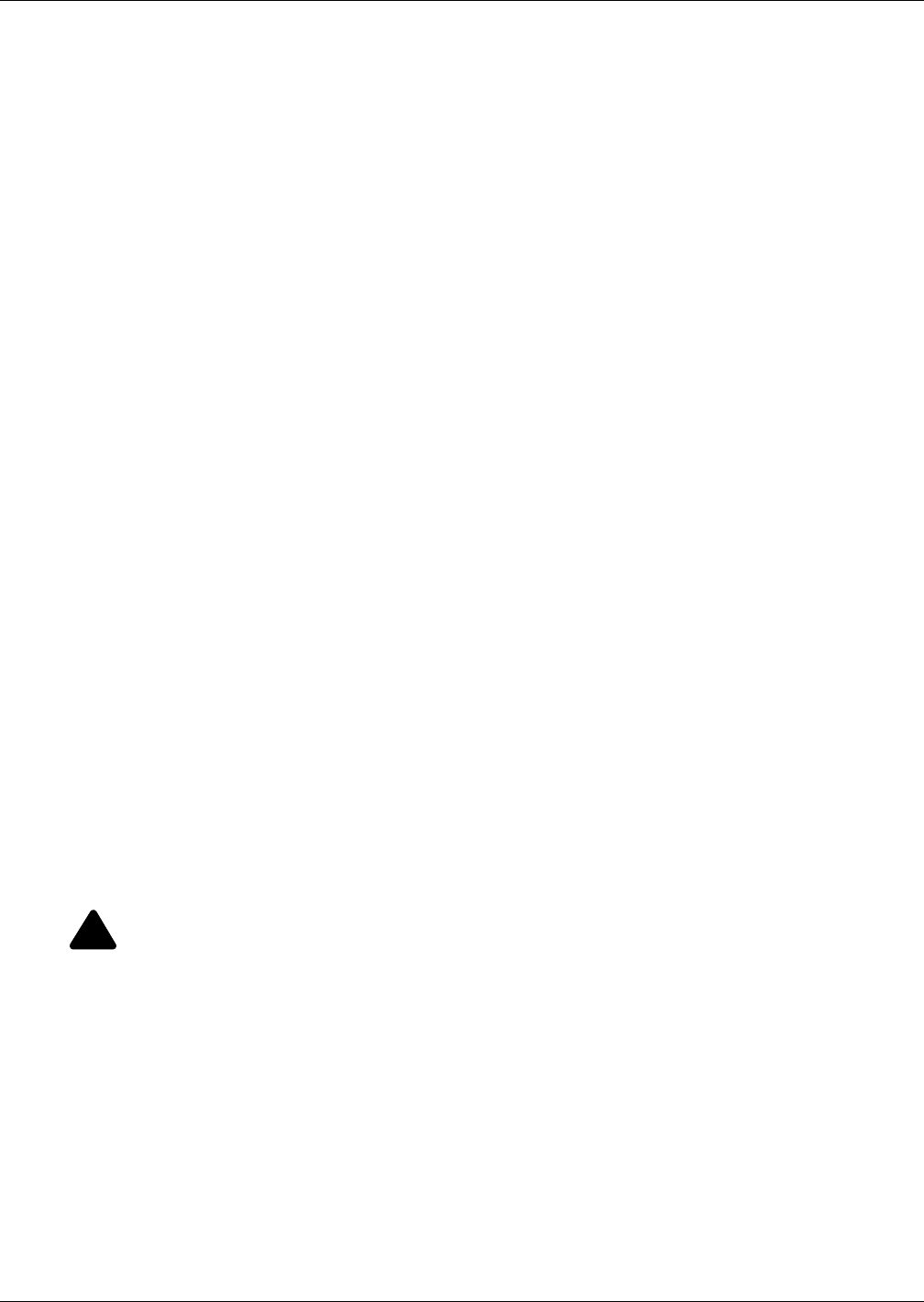
Maintenance
118
12.8 Compressor Replacement
Replacement compressors are available through your local Emerson office. Compressors are shipped
in reusable packaging. If unit is under warranty, complete and include Liebert Service Credit Appli-
cation (LSCA) with the compressor that is being returned. The original compressor should be
returned in the same packaging.
12.8.1 Compressor Motor Burnout
If a burnout has occurred, a full system clean-out is required; if not, compressor and system problems
will continue.
For clean-out warnings and procedures, see Copeland Application Engineering Bulletin 24-1105
“Principles of Cleaning Refrigeration Systems” or Carlyle Service Guide, Literature # 020-611.
12.8.2 Digital Compressor Unloading Solenoid(s)
Models 028, 035 and 042
When replacing a digital scroll compressor, digital solenoid valve and coil must be replaced. Compres-
sor and valve kit are shipped separately. Valve kit must be field-brazed to top of compressor in proper
orientation and supported with original factory bracket.
Models 053, 070 and 077
When replacing a digital scroll compressor, digital solenoid coil must be replaced. Compressor and coil
kit are shipped separately.
12.8.3 Compressor Replacement Procedure
1. Disconnect power and follow all warnings at front of this manual.
2. Attach suction and discharge gauges to access fittings.
3. Front-seat service valves to isolate the compressor. Reclaim charge from compressor.
4. Remove marked pressure transducer and discharge pressure switch. Disconnect all electrical
connections.
5. Detach service valves from compressor.
6. Remove failed compressor.
7. If required, follow compressor manufacturer’s suggested clean-out procedures.
8. Install replacement compressor and make all connections. Replace gaskets or seals on service
valves. Replace unloading solenoid.
9. Evacuate, charge and operate per 8.3 - Dehydration/Leak Test and Charging Procedures
for R-407C and R-22.
10. Semi-hermetic only: see 5.3 - Semi-Hermetic Compressor Spring Isolation System for
compressor spring adjustment.
12.9 Facility Fluid and Piping Maintenance
Facility water and glycol quality remain a requirement throughout the life of the piping system. Fluid
and piping system maintenance schedules must be established and performed. A local fluid mainte-
nance program must be established that will evaluate fluid chemistry and apply necessary treatment.
A periodic leak inspection of facility and unit fluid piping is recommended. Refer to 8.1.3 - Require-
ments of Systems Using Water or Glycol.
!
CAUTION
Risk of improper component reinstallation. Can cause equipment damage.
Identify and mark location of suction pressure transducer and discharge pressure switch.
These devices look similar and they must be reinstalled in their original location.