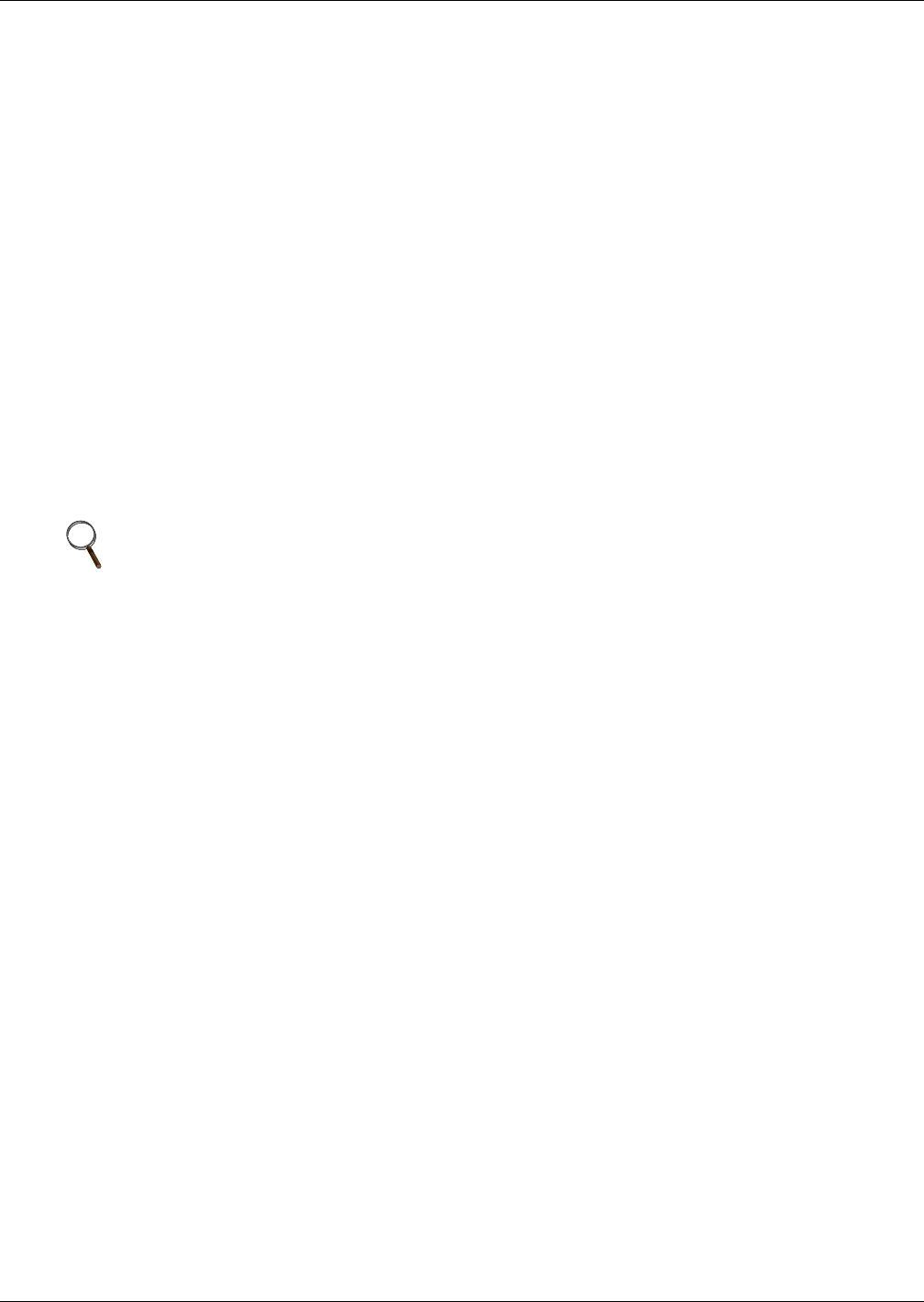
Piping
78
8.3 Dehydration/Leak Test and Charging Procedures for R-407C and R-22
8.3.1 Air-Cooled Condenser with Fan Speed Head Pressure Control System
The Fan Speed Control system uses a pressure activated electronic fan speed control system and
remotely located thermostat(s) to ensure operation at ambient temperatures as low as 0°F (-18°C).
Fan Speed Control Piping
Two discharge lines and two liquid lines must be field-installed between the indoor unit and the out-
door condenser. See Figures 57 and 59 for details.
Fan Speed Control Materials Supplied
•Built-in, pre-wired condenser control box
• Air-Cooled condenser
• Piping access cover to be reinstalled when piping is complete
• Bolts—four per leg (3/8" x 5/8")
• Terminal block for two-wire, 24V interlock connection between unit and condenser
• Condenser legs—four with 1-fan, 2-fan and 3-fan models; six with 4-fan models
Fan Speed Control Leak Check and Evacuation Procedure
Proper leak check and evacuation can be accomplished only with all system solenoid valves open and
check valves accounted for.
1. If unit power is available, open the unit liquid line solenoid valves using the evacuation function
for System #1 and System #2 in the diagnostic section of the iCOM control (refer to the iCOM user
manual, SL-18835). If unit power is not available, a field-supplied 24VAC / 75VA power source
must be directly connected to each of the unit solenoid valves.
2. For semi-hermetic compressors, connect refrigeration gauges to the suction and discharge service
valves of both compressors.
3. For scroll and digital scroll compressors, connect refrigerant gauges to the suction rotalock valves
and discharge line Schrader valves (see Note above) on both compressors.
4. Starting with Circuit #1, open the service valves and place a 150 PSIG (1034 kPa) of dry nitrogen
with a tracer of refrigerant. Check system for leaks with a suitable leak detector.
5. With pressure still in Circuit #1, open the compressor service valves in Circuit #2. If pressure
increases in Circuit #2, the system is cross-circuited and must be rechecked for proper piping. If
there is no pressure increase, repeat the leak check procedure for Circuit #2.
6. After completion of leak testing, release the test pressure (per local code) and pull an initial deep
vacuum on the system with a suitable pump.
7. After four hours, check the pressure readings and, if they have not changed, break vacuum with
dry nitrogen. Pull a second (R-407C and R-22) and third (R407C only) vacuum to 250 microns or
less. Recheck the pressure after two hours. After completing this step, proceed to Fan Speed
Charging.
NOTE
Systems with scroll or digital scroll compressors include a factory-installed check valve and an
additional downstream Schrader valve with core in the compressor discharge line. Proper
evacuation of the condenser side of the compressor can be accomplished only using the
downstream Schrader valve. See piping schematic (Figures 57 and 59).