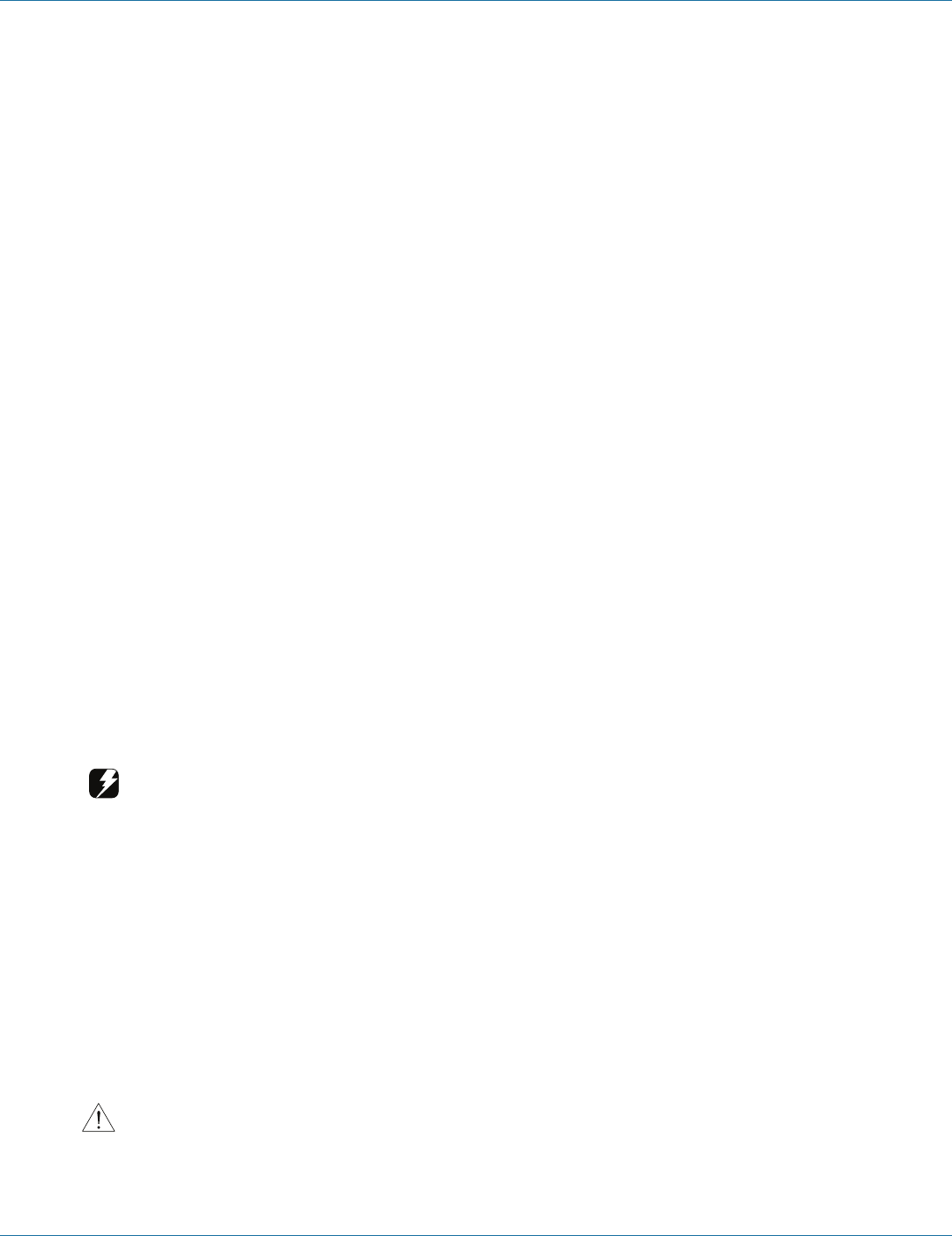
724-746-5500 | blackbox.com
724-746-5500 | blackbox.com
Page 39
Chapter 2: Installation
NOTE: When pulling a vacuum, the Schrader valves will unnecessarily restrict the openings, increasing the evacuation time. During
the evacuation process, we recommend that you remove the Schrader valve cores with a Schrader valve removal tool and
draw the vacuum through the port on the removal tool.
4. If you cannot evacuate the system below 1500 microns, close the vacuum pump isolation valve and perform a rate-of-rise test
by observing the standing pressure over time. If the pressure rises slowly (up to 200 microns in 15 minutes), there is moisture in
the system that still needs to be boiled off. Proceed to Step #5. If the pressure rises rapidly up to atmospheric pressure (more
than 50 microns per minute), there is a leak that wasn’t detected during Step #2. In this case, troubleshoot the entire system
for leaks and repair them. Then begin the initial evacuation process again starting at Step #3.
5. If no leaks are detected after the initial vacuum, release the vacuum and pressurize the system with 2–3 pounds of dry
nitrogen. Allow the system to stand for two hours with the dry nitrogen charge. This gives time for the nitrogen molecules to
disperse in the system and absorb moisture.
6. After two hours, release the pressure. Then turn on the vacuum pump and evacuate the system a second time down to 1500
microns or less. Close the vacuum pump isolation valve and pressurize the system again with dry nitrogen and allow the system
to stand for two hours as in Step #5.
7. After two hours, release the pressure. Turn on the vacuum pump and complete the process of evacuating the system, this time
with a goal of achieving a 250-micron vacuum or less. Close the vacuum pump isolation valve. When you can hold the vacuum
at 500 microns or lower for at least 2 hours with no significant rise in pressure, the system is ready to charge.
8. Replace the Schrader valve cores if you removed them during the evacuation steps. You may now introduce the refrigerant
charge through the Schrader valves.
2.10.2.3 Refrigerant Charging Procedures
R410A refrigerant must be weighed in when performing the charge. Referring to Section 2.10.2.1, calculate the estimated amount
of refrigerant needed for your system.
When charging a system using a blended refrigerant, it is essential that the composition of the refrigerant is maintained. To ensure
correct composition, introduce the refrigerant (R410A) into the system in liquid form rather than vapor form. Cylinders that do not
have dip tubes should be inverted to allow only liquid refrigerant to charge the system. Keeping the temperature of the cylinder
below 85° F will help maintain the correct refrigerant composition while the cylinder is emptied.
WARNING
If refrigerant gas is released in an enclosed area, it may accumulate in low areas and near the floor, displacing
available oxygen. If a major leak occurs, there is a risk of asphyxiation. In such case, the area should be immediately
evacuated and ventilated. Personnel should remain away from the area until it is determined to be safe.
Initial System Charge
Follow the step-by-step instructions below to charge systems using R410A refrigerant. The initial charge will be performed by
introducing liquid refrigerant to the discharge side of the compressor or an available liquid line port with the A/C unit turned Off.
1. Bleed air from hoses and break the vacuum by supplying liquid refrigerant (R410A) to the discharge port near the compressor
until the pressure is equalized. This holding charge allows the low pressure switch to “hold,” enabling the compressor to
operate throughout the process of charging the system.
Fine-Tuning the System Charge
Once the initial charge is completed, refrigerant will need to be added with the unit running.
CAUTION
An adequate heat load must be supplied to ensure a proper charge.
2. Disconnect the refrigerant cylinder from the discharge side of the compressor and connect it to the suction side.