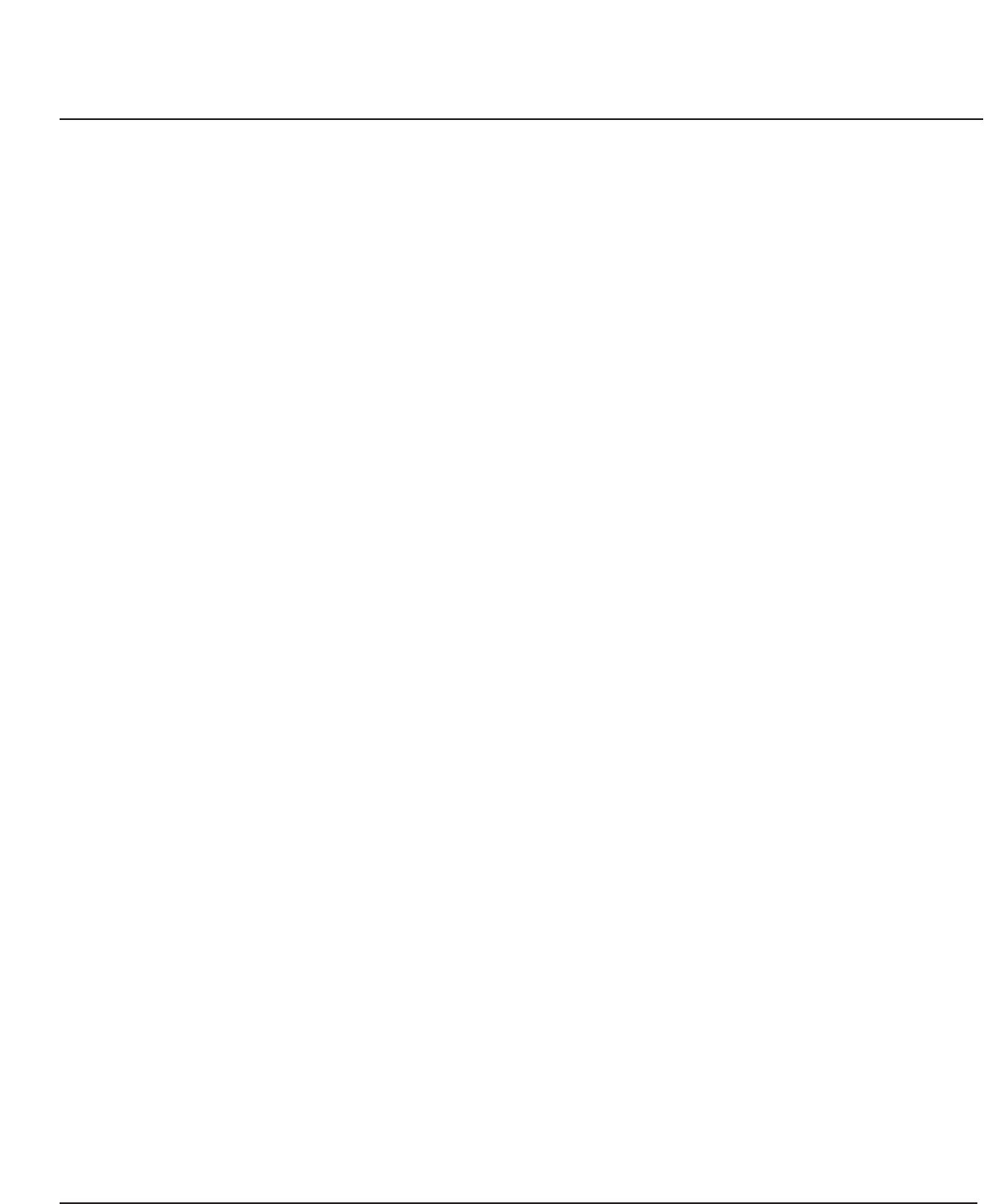
A microprocessor is used in the Inverter system to generate
a reference sine wave via one of its three PWM outputs. The
PWM signal is filtered to make a clean sine wave. This sine
wave is applied to a voltage error amplifier. The other input
to the voltage error amplifier is the output of one of the
inverters, called the master inverter. The voltage error
amplifier controls the amount of current the inverter supplies
to its output filter capacitor and output load. A second
amplifier (current error amplifier) compares the current
command (voltage error amplifier output) to the choke
current (voltage from another DC current transformer) and
produces an error signal which is applied to a motor control
PWM chip which completes the loop. Operating frequency of
the Inverter is 33kHz, generated by the motor control chips
oscillator.
The microprocessor is used to enable and disable the
battery booster, generate the sine wave reference signal,
enable and disable the Inverter, measure battery
current/voltage, Utility current/voltage/frequency, Output
current/voltage/frequency, provide LCD metering data, and
communicate with other equipment. Selection of the
Inverter’s output voltage and frequency (as set by the DIP
switch) is accessible through the side of the inverter module.
Isolation between DC input electronics and AC output (Line
side) electronics is via high speed optical couplers. If Utility
voltage is present and its frequency is close to the setting on
the DIP switch, then the sine wave reference signal will
become phase locked to the Utility. Frequency slew rate is
less than 1 Hz per second, phase error will be less than 6
degrees. The microprocessor is supplied by power from the
DC input side and the sine wave reference must be provided
to the Inverter, located on the secondary (AC output) side. A
high speed optical coupler is used to get the PWM signal to
the Inverter electronics. This PWM signal is filtered by a two
stage R-C filter and then buffered before it is applied to the
voltage error amplifier. Enable/disable of the Inverter by the
microprocessor is also via this same optical coupler.
Feedback of the input and output AC voltage is
accomplished by using the motor control PWM oscillator
(triangle wave shape, ramping linearly between +4 and -4
volts at 33 kHz rate) to make a PWM signal. This signal is
applied to an optical coupler, buffered, and filtered to
produce an isolated replica of the AC voltages. The
microprocessor has eight analogue inputs, two of which are
used to measure the AC signals. Other inputs to the micro
are: Inverter output current, Utility current (for back feed
protection), battery voltage, battery current, and two heat
sink temperatures.
3.1.2.2 Reference Sine
Wave and Control
3.1.2.1 Average Current
Mode
3 — 6 Theory of Operation 86-153061-00
Topaz S3 Inverters 0.5 kVA, 1 kVA, & 2 kVA