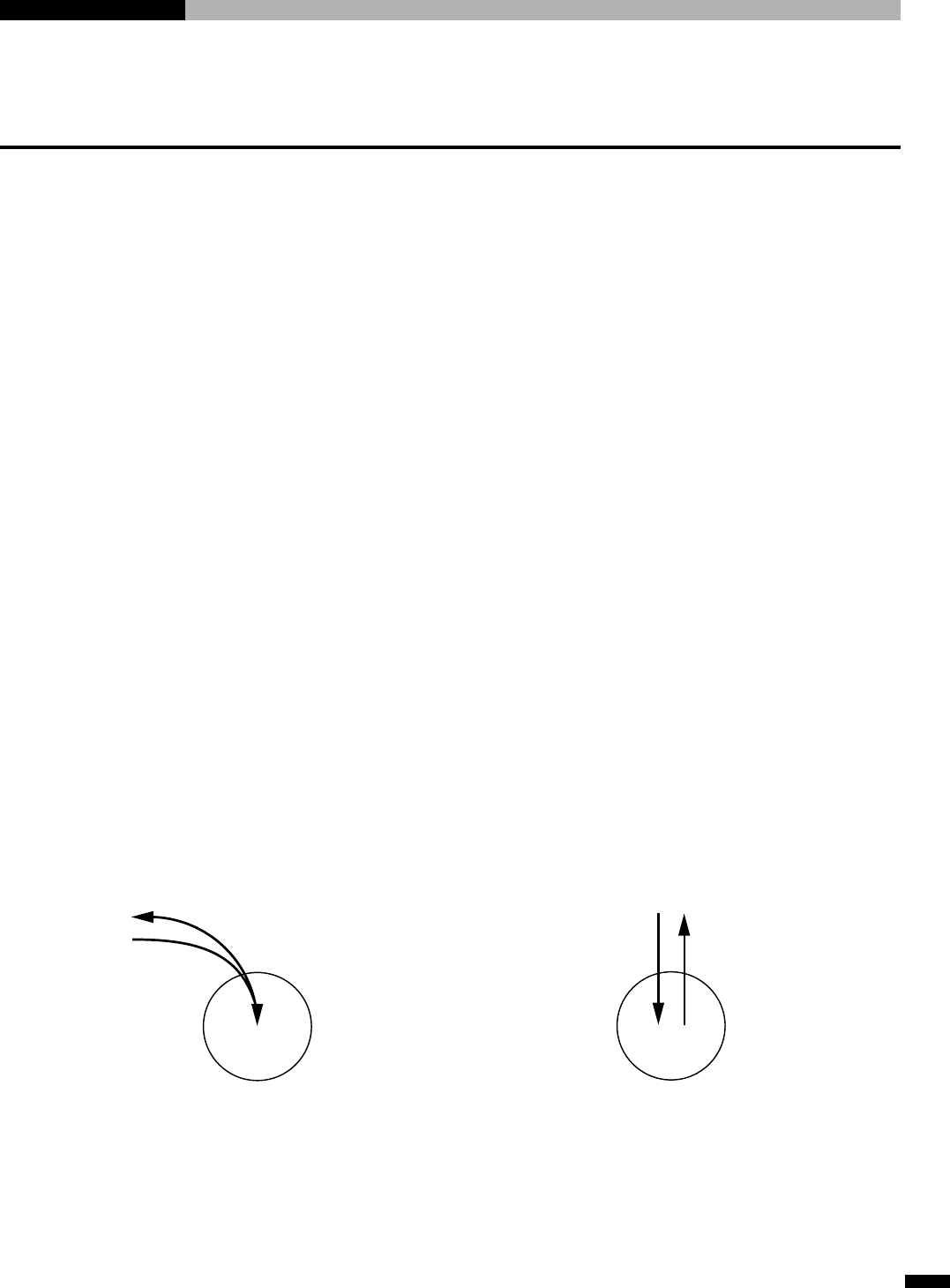
4-1
4. Troubleshooting
CAST-AU4/B2521E
4. Troubleshooting
4-1 Common Items
4-1-1 Stepping Out (Note 1)
The machine performs open loop servo control using a pulse motor (stepping motor) without positional
feedback. The machine thus continues to operate with positional error even if it steps out due to overloading
of the retaining torque of the motor.
When the base machine steps out, or when it operates with positional errors, check the
following items first.
(1) Overloaded
The base machine has a limited carrying loading. Check whether the load exceeds the maximum payload
that the respective axes can carry by referring to page 1-6, section 1-3, “Specifications.”
The payload with which the machine can operate at 100% speed is smaller than the maximum payload, and
varies for each axis. Check the actual load weight before operating the machine.
(2) External force
External forces from cables and pipes are normally larger than anticipated, and can easily exceed the
retaining torque of the motor. Be careful of unexpected external forces when using stiff wires or pipes that
cannot be easily bent.
(3) Rapid speed change
When a rapid speed change occurs such as an immediate returning movement while an interpolation
operation is being performed, the load inertia may exceed the retaining torque of the motor, causing the
motor to step out.
Before performing such a movement, reduce the operating speed.
Example : Returning movement of the circular Example : Returning movement of the Z-axis
interpolation operation operation
(Movements are synthesized sometimes.)
Note 1 : What is “stepping out”?
When the drive shaft of a motor is overloaded beyond the torque of the motor, the drive shaft spins (revolves
swiftly without control) regardless of the control that is applied to the motor.
This is called “stepping out”.
This term is sometimes used incorrectly for tooth-skipping (between pulley and belt), but stepping out and
tooth-skipping are actually entirely different phenomena.