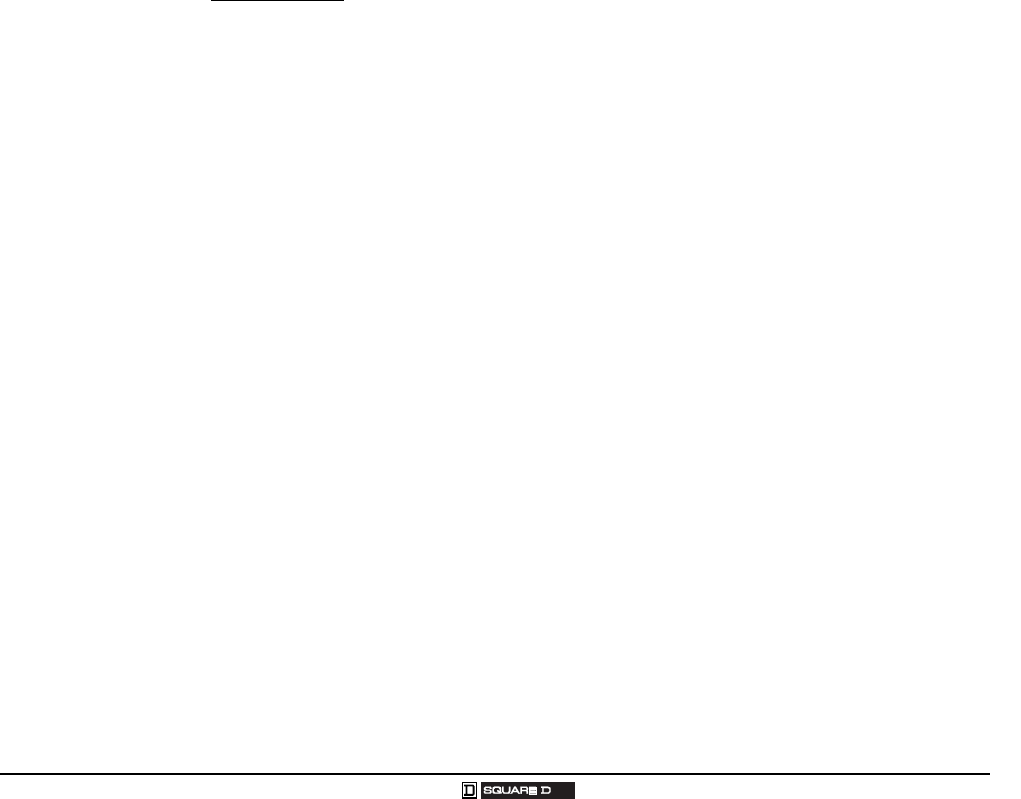
Class 8839 58M Enclosed AC Drives
Specifications
181
09/2003
© 2000–2003 Schneider Electric All Rights Reserved
Netscape Navigator. No additional
software should be required.
2. The embedded web-pages shall be
secured by use of a customizable user
name and password.
3. Standard Ethernet hubs, switches and
routers can be used, although industrial
grade devices are recommended if the
environmental conditions warrant.
4. The Ethernet Communications Card shall
support the following services via the
standard Ethernet Port 502:
a) TCP/Modbus Client, with support for
periodic I/O Scanning
b) HTTP Server for drive configuration,
control, and monitoring.
c) ICMP client to support certain IP
services such as the “ping” command.
d) BOOTP client to assign an IP Address
via an address server.
5. The Ethernet Communications card shall
have diagnostic LED that monitor
communication
Note to Specifier
: One of the following
communication cards can be specified lieu of
Ethernet Communication:
Modbus / Unitelway, Modbus Plus, LonWorks,
Device Net, Johnson Controls METASYS N2,
FIP I/O
2.14 MESSAGE DISPLAY CENTER
REQUIREMENTS
a. The message display center / keypad display
shall be menu based and offer the
modification of AC Drive adjustments via a
touch keypad. All electrical values,
configuration parameters, I/O assignments,
application and activity function access, faults,
local keypad control, and adjustment storage
will be in plain English.
b. The display will be a high-resolution,
backlighted LCD screen capable of displaying
4 lines of 20 alphanumeric characters.
c. The AC Drive model number, torque type,
software revision number, horsepower, output
current, motor frequency and motor voltage
shall all be listed on the drive identification
display as viewed on the LCD display.
d. The keypad interface shall be configured to
display selectable outputs such as speed
reference, output frequency, output current,
motor torque, output power, output voltage,
line voltage, DC voltage, motor thermal state,
drive thermal state, elapsed time, motor
speed, machine speed reference and
machine speed.
e. The operator terminal shall provide a main
menu consisting of status, programming, drive
configuration, and keypad operation. A
hardware jumper lock shall protect drive setup
from unauthorized personnel by limiting
access to the programming and drive
configuration menus. A software password
shall be configured to limit access to all menus
except status. The status menu shall show
meters, I/O map, fault history and drive
identification.
f. There will be arrow keys that will provide the
ability to scroll through menus and screens,
select or activate functions or increase the
value of a selected parameter.
g. A data entry key will allow the user to confirm
a selected menu, numeric value or allow
selection between multiple choices.
h. An escape key will allow a parameter to return
the existing value if adjustment is not required
and the value is displayed. The escape
function will also return to a previous menu
display.
i. A RUN key and a STOP key will command a
normal starting and stopping as programmed
when the AC Drive is in keypad control mode.
The STOP key must be programmable for
active in all control modes.
j. The keypad interface shall have three
backlight colors to indicate functional status. A
green color backlight will verify that the AC
Drive is running. A red color backlight will
indicate an AC Drive fault. An orange color
backlight color will designate and idle or drive
ready status.
k. The keypad and all door mounted controls
must be [Type 1,Type 12] rated.
2.15 EMERGENCY FULL SPEED
REQUIREMENTS
a. The AC Drive shall include fully rated isolation
and bypass contactors complete with Class 20
thermal overload relay protection for
emergency full speed capability. Bypass and
isolation contactor shall be mechanical and
electrical interlocked. Emergency full speed
bypass shall be [full voltage cross the line,
solid state reduced voltage soft starter,
reduced voltage autotransformer type.]
Bypass and isolation contactors shall be in
[Integrated, Barriered] construction.
1. Integrated bypass shall consist of
integrating bypass and isolation contactors
into the same enclosure compartment as
the AC drive controller if space permits.