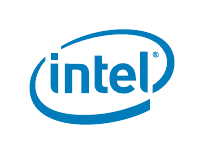
Sensor Based Thermal Specification Design Guidance
68 Thermal/Mechanical Specifications and Design Guidelines
Note: This graph is provided as a reference, the complete thermal specification is in
Chapter 6.
8.2.2 Specification When DTS value is Greater than T
CONTROL
The product specification provides a table of Ψ
CA
values at DTS = T
CONTROL
and
DTS = -1 as a function of T
AMBIENT
(inlet to heatsink). Between these two defined
points, a linear interpolation can be done for any DTS value reported by the processor.
The fan speed control algorithm has enough information using only the DTS value and
T
AMBIENT
to command the thermal solution to provide just enough cooling to keep the
part on the thermal profile.
In the prior thermal specifications this region, DTS values greater than T
CONTROL
, was
defined by the processor thermal profile. This required the user to estimate the
processor power and case temperature. Neither of these two data points are accessible
in real time for the fan speed control system. As a result, the designer had to assume
the worst case T
AMBIENT
and drive the fans to accommodate that boundary condition.
8.3 Thermal Solution Design Process
Thermal solution design guidance for this specification is the same as with previous
products. The initial design needs to take into account the target market and overall
product requirements for the system. This can be broken down into several steps:
• Boundary condition definition
• Thermal design / modelling
•Thermal testing.
8.3.1 Boundary Condition Definition
Using the knowledge of the system boundary conditions (such as inlet air temperature,
acoustic requirements, cost, design for manufacturing, package and socket mechanical
specifications and chassis environmental test limits) the designer can make informed
thermal solution design decisions.
For the thermal boundary conditions for system are as follows:
•T
EXTERNAL
= 35 °C. This is typical of a maximum system operating environment
•T
RISE
= 5 °C.
•T
AMBIENT
= 40 °C (T
AMBIENT
= T
EXTERNAL
+ T
RISE
)
Based on the system boundary conditions, the designer can select a T
AMBIENT
and Ψ
CA
to use in thermal modelling. The assumption of a T
AMBIENT
has a significant impact on
the required Ψ
CA
needed to meet TTV T
CASEMAX
at TDP. A system that can deliver lower
assumed T
AMBIENT
can utilize a design with a higher Ψ
CA
, which can have a lower cost.
Note: If the assumed T
AMBIENT
is inappropriate for the intended system environment, the
thermal solution performance may not be sufficient to meet the product requirements.
The results may be excessive noise from fans having to operate at a speed higher than
intended. In the worst case this can lead to performance loss with excessive activation
of the Thermal Control Circuit (TCC).