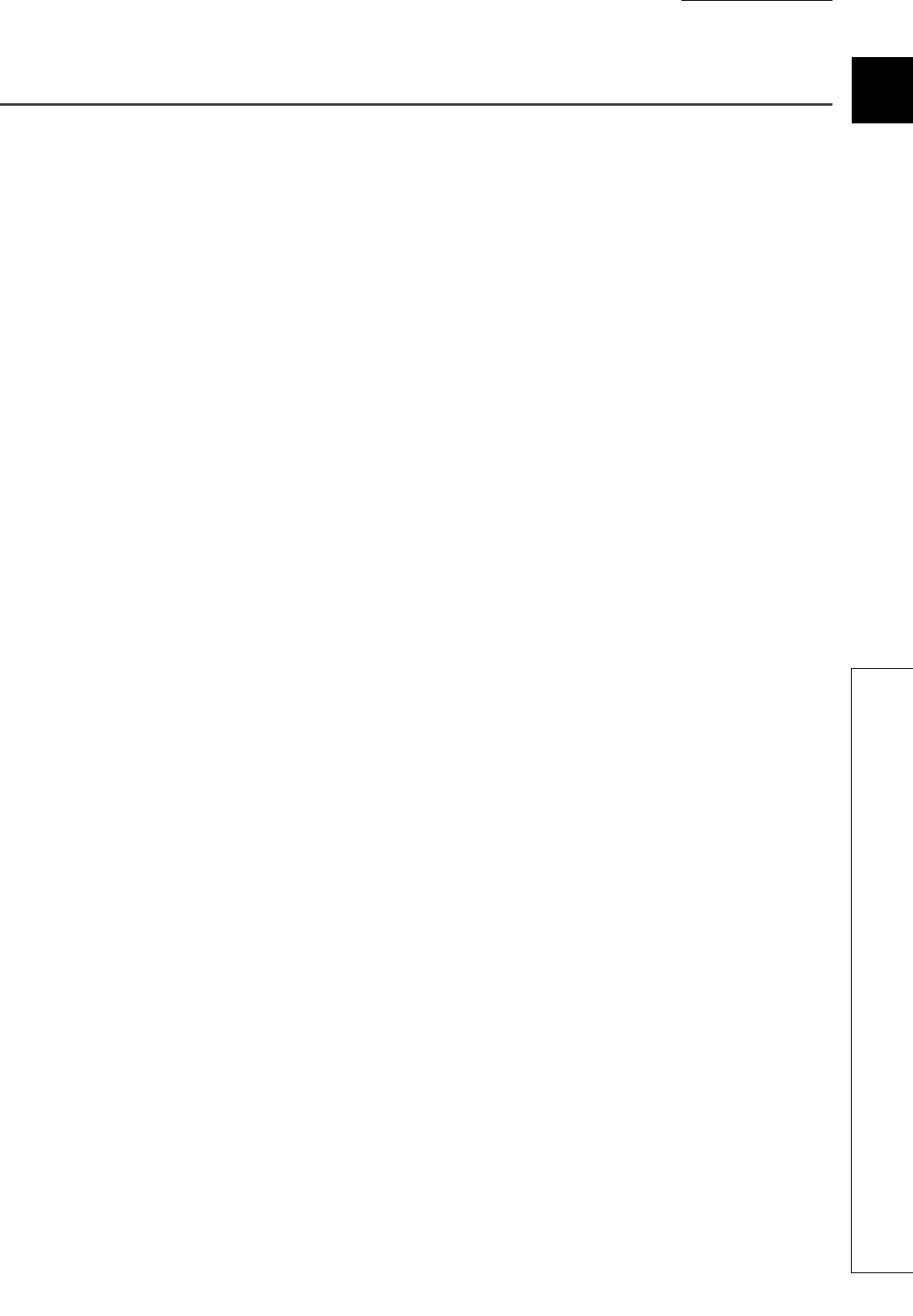
19
CHAPTER 1 OVERVIEW
1
1.1 Features
1.1 Features
(1) Optimum temperature adjustment control (PID control)
• The Q64TCN performs temperature adjustment control automatically when the user simply sets PID
constants necessary for PID operation: proportional band (P), integral time (I), derivative time (D), and
temperature set value (SV). No special instruction is necessary to perform PID control.
• Using the auto tuning function or self-tuning function enables the PID constants to be set automatically.
Complicated PID operational expressions to determine PID constants are not necessary.
(2) Selection of control mode
A control mode can be selected from the standard control (heating or cooling), heating-cooling control (heating
and cooling), or mix control (combination of the standard control and heating-cooling control).
(3) Four loops on one module
The maximum of four loops of temperature adjustment control can be performed simultaneously. In addition, loop
control can be performed using analog modules on the base unit or the network; input from an A/D converter
module or output to a D/A converter module can be processed.
(4) Simultaneous temperature rise of multiple loops
Temperatures of multiple loops can be adjusted to simultaneously reach the set value of each; temperatures are
controlled evenly without any partial heat exaggeration. This function saves energy and cost.
(5) Suppression of peak current
Current flows into a heater can be suppressed by controlling output so that each channel's output does not turn
on at the same time as other channels.
This function saves energy and cost.
(6) RFB limiter function
The RFB (Reset feed back) limiter suppresses overshoot which is liable to occur at a startup or when a
temperature process value (PV) is increased.
(7) Correction of temperature process value (PV)
The difference between the temperature process value (PV) and actual temperature can be corrected easily
using the following functions.
• Normal sensor correction (one-point correction) function: Corrects the difference by setting the rate of
correction value to the full scale of the input range.
• Sensor two-point correction function: Corrects the difference based on the inclination of the line on the two
points set in advance.
• Primary delay digital filter setting: Smoothens transient noise, and absorbs drastic change.
(8) E
2
PROM for backing up set values
The set values in the buffer memory, such as the setting related to PID control, can be stored into E
2
PROM for
data backup. The values do not need to be reset after turning the power on from off or releasing the CPU module
from its reset status.
Using the test function of the programming tool to write data directly to the buffer memory, the minimum
sequence program required is "LD**" + "OUT Yn1".