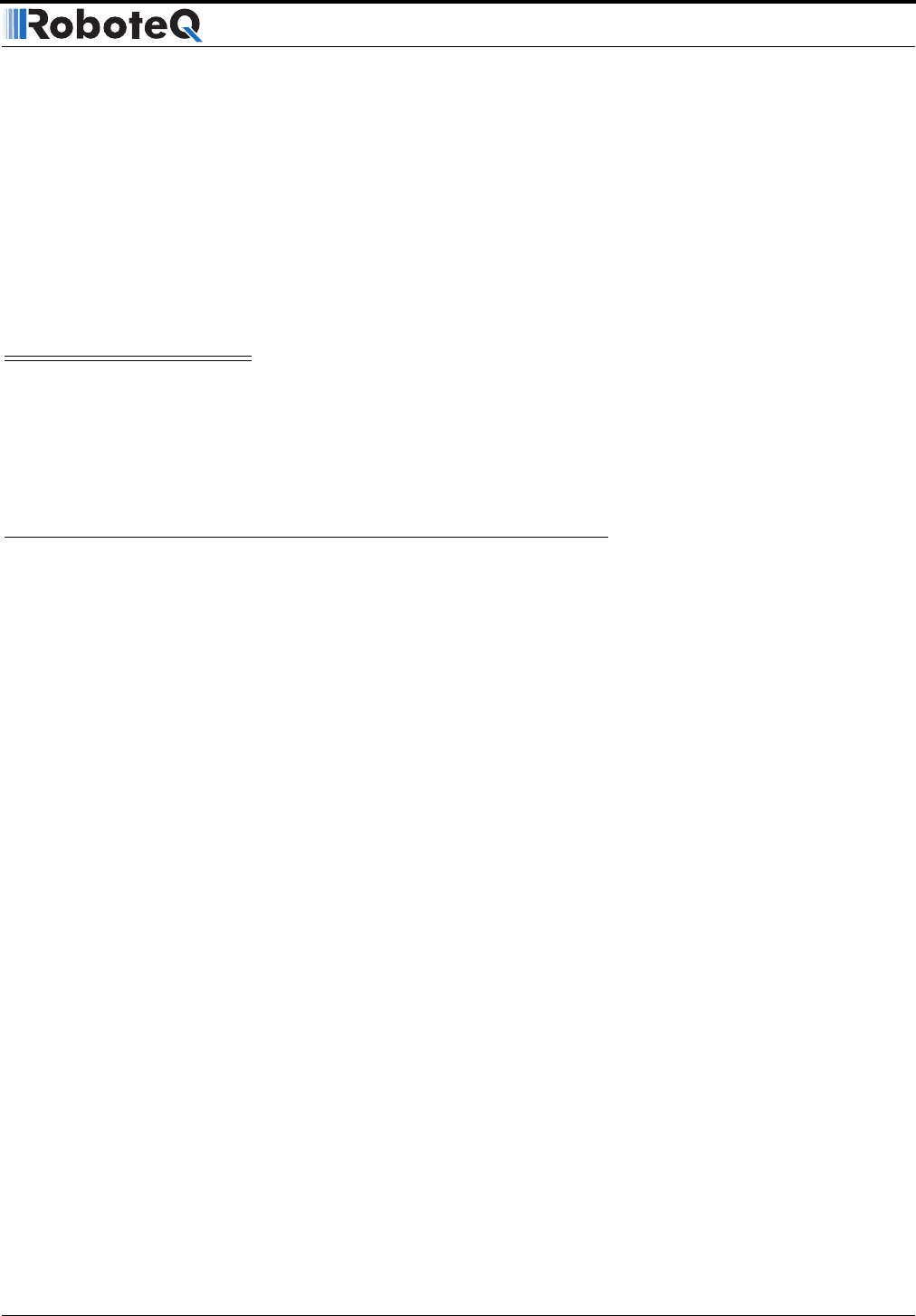
AX1500 Motor Controller User’s Manual 83
Feedback Potentiometer wiring
The mechanical coupling between the motor and the sensor must be as tight as possible.
If the gear box is loose, the positioning will not be accurate and will be unstable, potentially
causing the motor to oscillate.
Some sensor, such as potentiometers, have a limited rotation range of typically 270
degrees (3/4 of a turn), which will in turn limit the mechanical motion of the motor/potenti-
ometer assembly. Consider using a multi-turn potentiometer as long as it is mounted in a
manner that will allow it to turn throughout much of its range, when the mechanical
assembly travels from the minimum to maximum position.
Important Notice:
Potentiometers are mechanical devices subject to wear. Use better quality potenti-
ometers and make sure that they are protected from the elements. Consider using a
solid state hall position sensor in the most critical applications. Optical encoders
may also be used when operated as discussed in “Using the Encoder to Measure
Speed” on page 76
Feedback Potentiometer wiring
When using a potentiometer, it must be wired so that it creates a voltage that is propor-
tional to its angular position: 0V at one extreme, +5V at the other. A 10K potentiometer
value is recommended for this use.
Analog Feedback is normally connected to the Analog Inputs 1 and 2, except when the
controller is configured in Analog Mode. In Analog mode, Analog Inputs 1 and 2 are already
used to supply the command. Therefore Analog inputs 3 and 4 are used for feedback
Feedback Potentiometer wiring in RC or RS232 Mode
In RC or RS232 mode, feedback is connected to Analog Inputs 1 and 2. Connecting the
potentiometer to the controller is as simple as shown in the diagram on below.
Note that this wiring must not be used if the controller is configured in Analog mode but is
switched in RS232 after power up using the method discussed in “Entering RS232 from R/
C or Analog mode” on page 126. Instead, used the wiring for Analog mode discussed in
the next section.