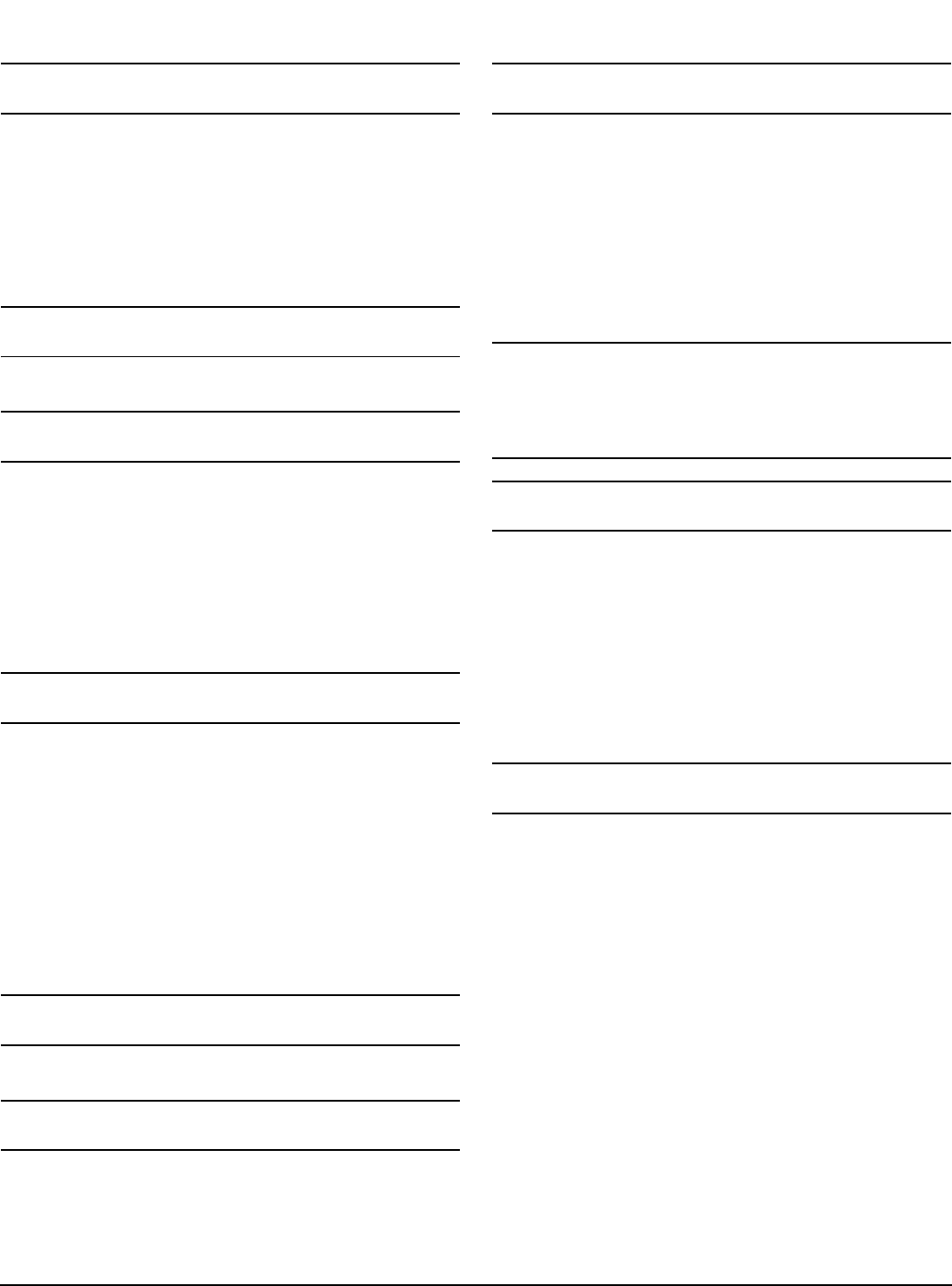
Parameter Descriptions www.emersonct.com 97
Master Axis Feedback Selector
MasterAxis.SpeedFeedbackSelector
The MasterAxis.Speed Feedback Selector parameter
determines where the feedback device for the master
signal is connected to. Early releases of the SM-EZMotion
module only support a value of Slots 1, 2, or 3 (and NOT
Drive). The master encoder feedback signal must be
connected to a SM-Universal Encoder Plus module fitted
into one of the Unidrive SP option slots. This parameter is
read-only from within a user program.
Module Serial Number
ModuleSerialNumber
This is the SM-EZMotion module serial number.
SM-EZMotion Module Temperature
ModuleTemperature
This parameter displays the current temperature measured
on the SM-EZMotion module. A module error will be
generated if the module temperature reaches or exceeds
89ºC. Available only in "Too Much Mode".
When temperature reported by module reaches or
exceeds 84
ºC,the internal fan of the Unidrive SP will be
forced to full speed. The fan will remain at full speed until
the temperature drops below 79
ºC.
Motion Stop
MotionStop
This destination is used to stop all motion operating without
stopping programs. MotionStop can be activated through
an assignment, or in a user program. This function is level
sensitive, meaning that as long as MotionStop is active, all
motion will be prevented. If a program has a motion
statement, the program will wait on that line of code until
the MotionStop function has been deactivated. If motion is
in progress when MotionStop is activated, the profile will
decelerate to zero velocity at the deceleration rate
specified in the Stop.Decel parameter. All motion will stop
using a realtime deceleration, regardless of the motions
original timebase.
Motor Type
MotorType
This parameter is used to select the motor type.
Name
Name
User name for this SM-EZMotion axis can have a length up
to 12 characters. This can be used to help differentiate
setup files.
Unidrive SP Overload Accumulator
OverloadAccumulator
This parameter gives an indication of the motor
temperature based on a simple thermal model. The
formula for the thermal model is a function of the current
demand and a thermal time constant of the motor
(parameter 4.15 and found in .ddf file). This read-only
parameter gives an estimated motor temperature as a
percentage of maximum motor temperature. When the
calculated temperature reaches 100%, the drive will limit
the amount of current available to the motor until this
parameter falls below 95%.
Note
The overload accumulator is reset to zero on power-up.
Therefore, if a motor is already hot (near its thermal limit),
and power is cycled quickly, the accumulator is no longer
a good indicator of motor temperature.
PLS Direction
PLS.#.Direction
This parameter specifies the direction of motion that a
particular PLS output will function. If set to Both, the PLS
will activate regardless of whether the axis is moving in the
positive or negative direction. If set to Plus, the PLS will
activate only when the axis is moving in the positive
direction. If set to Minus, the PLS will activate only when
the axis is moving in the negative direction. A flying cutoff
or flying shear application may use this feature to activate
the PLS to fire the knife only when the axis is moving in the
positive direction.
PLS Off Point
PLS.#.OffPosn
PLS.#.Status will be active when the selected source
position is between the PLS.#.OnPosn and the
PLS.#.OffPosn. The terms On and Off assume you are
traveling in a positive direction. Assume that the
PLS.#.Direction is set to "Both". When traveling in the
positive direction and the position feedback reaches the
OnPosn, the PLS.#.Status will activate. As the motor
continues in the same direction, the PLS.#.Status will
deactivate when feedback position reaches or exceeds the
OffPosn. If motor travel changes to the negative direction,
the PLS.#.Status will activate when position feedback
reaches the OffPosn, and will deactivate when it continues
past the OnPosn. The important thing to remember is that
the PLS.#.Status will be active if between the PLS On and
Off points.
If using negative values for the OnPosn and OffPosn, the
most negative value should go in the OnPosn parameter,
and the least negative value should go in the OffPosn.
If the PLS has a rollover point, and the OnPosn is greater
than the OffPosn, the PLS will be active whenever the axis