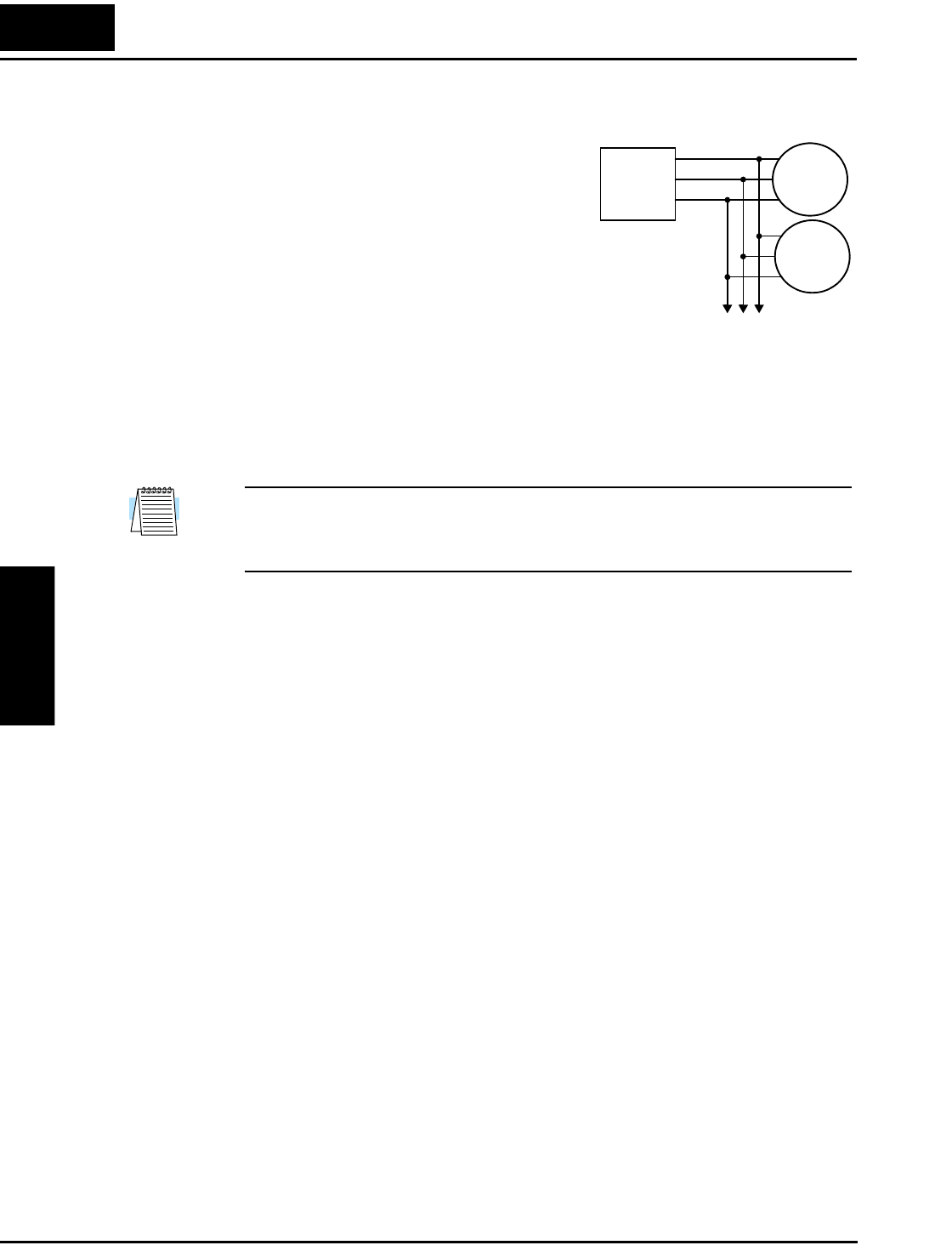
Configuring the Inverter for Multiple Motors
Operations
and Monitoring
4–72
Configuring the Inverter for Multiple Motors
Simultaneous
Connections
For some applications, you may need to connect two
or more motors (wired in parallel) to a single
inverter’s output. For example, this is common in
conveyor applications where two separate conveyors
need to have approximately the same speed. The use
of two motors may be less expensive than making the
mechanical link for one motor to drive multiple
conveyors.
Some of the requirements when using multiple
motors with one drive are:
• Use only V/F (variable-frequency) control; do not use SLV (sensorless vector control).
• The inverter output must be rated to handle the sum of the currents from the motors.
• You must use separate thermal protection switches or devices to protect each motor. Locate
the device for each motor inside the motor housing or as close to it as possible.
• The wiring for the motors must be permanently connected in parallel (do not remove one
motor from the circuit during operation).
NOTE: The motor speeds are identical only in theory. That is because slight differences in
their loads will cause one motor to slip a little more than another, even if the motors are identi-
cal. Therefore, do not use this technique for multi-axis machinery that must maintain a fixed
position reference between its axes.
Inverter
Configuration for
Multiple Motor
Types
Some equipment manufacturers may have a single type of machine that has to support three
different motor types—and only one motor will be connected at a time. For example, an OEM
may sell basically the same machine to the US market and the European market. Some reasons
why the OEM needs two motor profiles are:
• The inverter power input voltage is different for these markets.
• The required motor type is also different for each destination.
In other cases, the inverter needs two profiles because the machine characteristics vary accord-
ing to these situations:
• Sometimes the motor load is very light and can move fast. Other times the motor load is
heavy and must move slower. Using two profiles allows the motor speed, acceleration and
deceleration to be optimal for the load and avoid inverter trip (fault) events.
• Sometimes the slower version of the machine does not have special braking options, but a
higher performance version does have braking features.
Having multiple motor profiles lets you store several “personalities” for motors in one
inverter’s memory. The inverter allows the final selection between the three motor types to be
made in the field through the use of intelligent input terminal functions [SET] and [SET3]. This
provides an extra level of flexibility needed in particular situations. See the following page.
Inverter
to Nth motor
Motor 1
Motor 2
U/T1
V/T2
W/T3