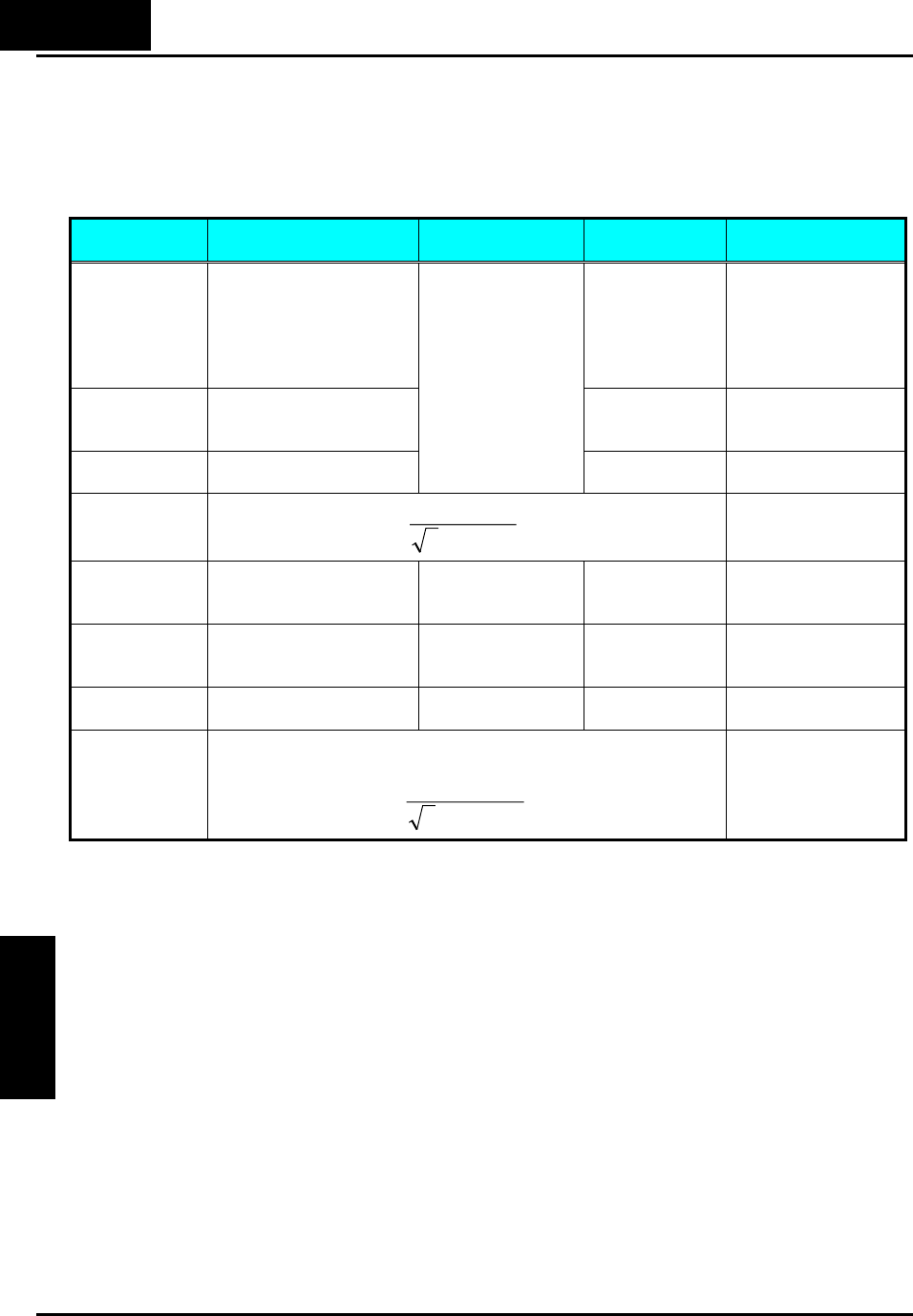
General Inverter Electrical Measurements
The following table specifies how to measure key system electrical parameters. The
diagrams on the next page show inverter-motor systems and the location of
measurement points for these parameters.
Parameter
Circuit location of
measurement
Measuring
instrument
Notes Reference Value
Supply voltage
E
1
E
R
– across L1 and L2
E
S
– across L2 and L3
E
T
– across L3 and L1
Fundamental
wave effective
value
Commercial supply
voltage
200V class:
200–240V, 50/60 Hz
400V class:
380–460V, 50/60 Hz
Supply current
I
1
I
r
– L1
I
s
– L2
I
t
– L3
Total effective
value
—
Supply power
W
1
W
11
– across L1 and L2
W
12
– across L2 and L3
Moving-coil type
voltmeter or
rectifier type
voltmeter
Total effective
value
—
Supply power
factor Pf
1
%100
3
11
1
1
×
××
=
IE
W
Pf
—
Output voltage
E
O
E
U
– across U and V
E
V
– across V and W
E
W
– across W and U
Rectifier type
voltmeter
Total effective
value
—
Output current
I
O
I
U
– U
I
V
– V
I
W
– W
Moving-coil type
ammeter
Total effective
value
—
Output power
W
O
W
O1
– across U and V
W
O2
– across V and W
Electronic type
wattmeter
Total effective
value
—
Output power
factor Pf
O
Calculate the output power factor from the output voltage E,
output current I, and output power W.
%100
3
1
×
××
=
OO
O
IE
W
Pf
—
Note 1: Use a meter indicating a fundamental wave effective value for voltage, and meters
indicating total effective values for current and power.
Note 2: The inverter output has a distorted waveform, and low frequencies may cause
erroneous readings. However, the measuring instruments and methods listed above
provide comparably accurate results.
Note 3: A general-purpose digital volt meter (DVM) is not usually suitable to measure a
distorted waveform (not pure sinusoid).
6−12
Troubleshooting and
Maintenance