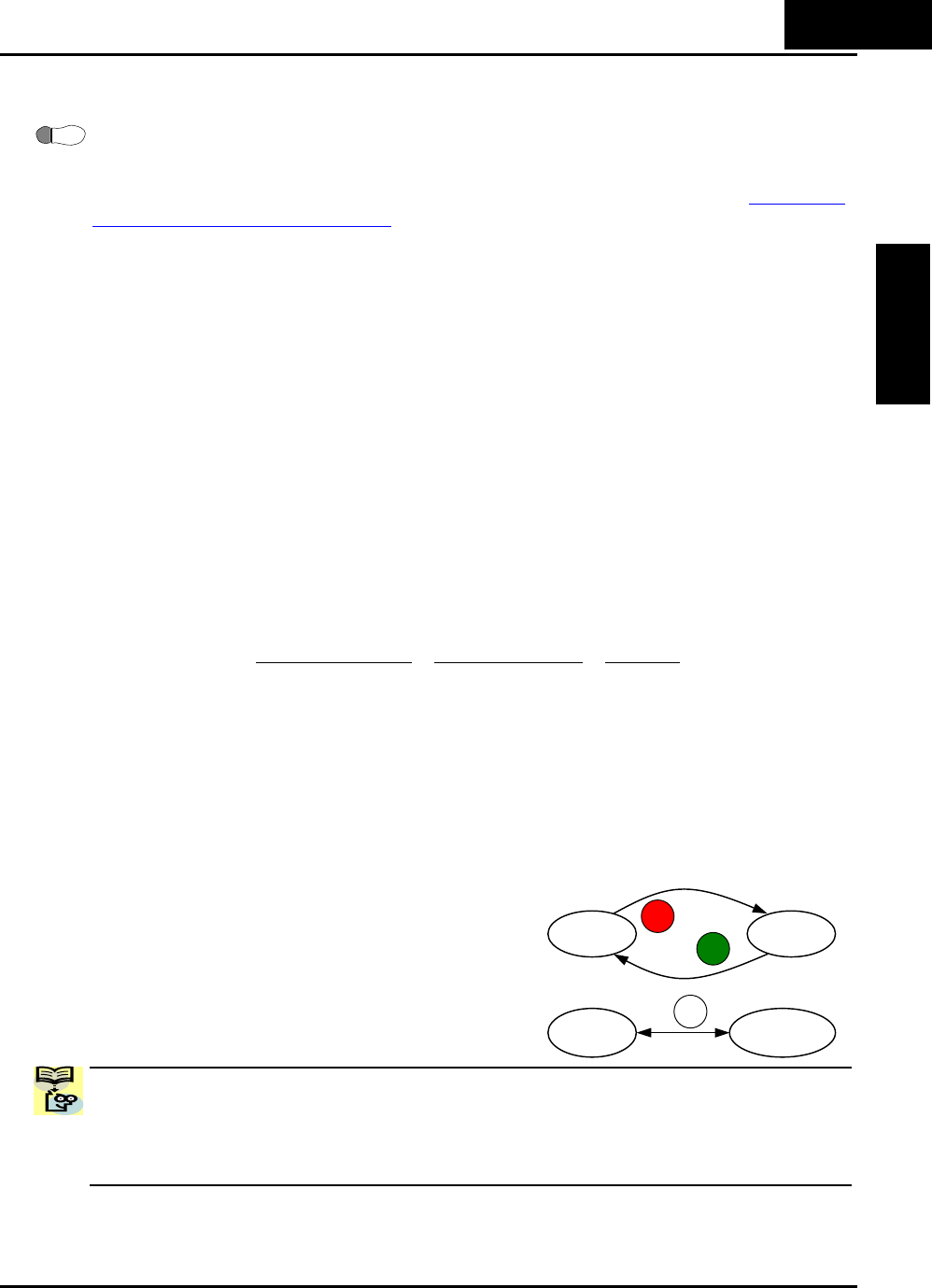
Powerup Test Observations and Summary
Step 10: Reading this section will help you make some useful observations when first
running the motor.
Error Codes – If the inverter displays an error code (format is “E xx”), see “Monitoring
Trip Events, History, & Conditions” on page 6-5 to interpret and clear the error.
Acceleration and Deceleration – The X200 inverter has programmable acceleration and
deceleration value. The test procedure left these at the default value, 10 seconds. You
can observe this by setting the potentiometer at about half speed before running the
motor. Then press RUN, and the motor will take 5 seconds to reach a steady speed.
Press the STOP key to see a 5 second deceleration to a STOP.
State of Inverter at Stop – If you adjust the motor’s speed to zero, the motor will slow to
a near stop, and the inverter turns the outputs OFF. The high-performance X200 can
rotate at a very slow speed with high torque output, but not zero (must use servo
systems with position feedback for that feature). This characteristic means you must
use a mechanical brake for some applications.
Interpreting the Display – First, refer to the output frequency display readout. The
maximum frequency setting (parameter A044) defaults to 50 Hz or 60 Hz (Europe and
United States, respectively) for your application.
Example: Suppose a 4-pole motor is rated for 60 Hz operation, so the inverter is
configured to output 60 Hz at full scale. Use the following formula to calculate the rpm.
Speed in RPM
RPM
polesof
Frequency
polesofPairs
Frequency
1800
4
12060
#
12060
=
×
=
×
=
×
=
The theoretical speed for the motor is 1800 RPM (speed of torque vector rotation).
However, the motor cannot generate torque unless its shaft turns at a slightly different
speed. This difference is called
slip
. So it’s common to see a rated speed of
approximately 1750 RPM on a 60 Hz, 4-pole motor. Using a tachometer to measure
shaft speed, you can see the difference between the inverter output frequency and the
actual motor speed. The slip increases slightly as the motor’s load increases. This is
why the inverter output value is called “frequency”, since it is not exactly equal to
motor speed.
Run/Stop Versus Monitor/Program Modes – The
Run LED on the inverter is ON in Run Mode, and
OFF in Stop Mode. The Program LED is ON
when the inverter is in Program Mode, and OFF
for Monitor Mode. All four mode combinations
are possible. The diagram to the right depicts the
modes and the mode transitions via keypad.
NOTE: Some factory automation devices such as PLCs have alternative Run/Program
modes; the device is in either one mode or the other. In the Hitachi inverter, however,
Run Mode alternates with Stop Mode, and Program Mode alternates with Monitor Mode.
This arrangement lets you program some value while the inverter is operating –
providing flexibility for maintenance personnel.
Run Stop
RUN
STOP
RESET
Monitor Program
FUNC
10
2
−
35
Inverter Mounting
and installation