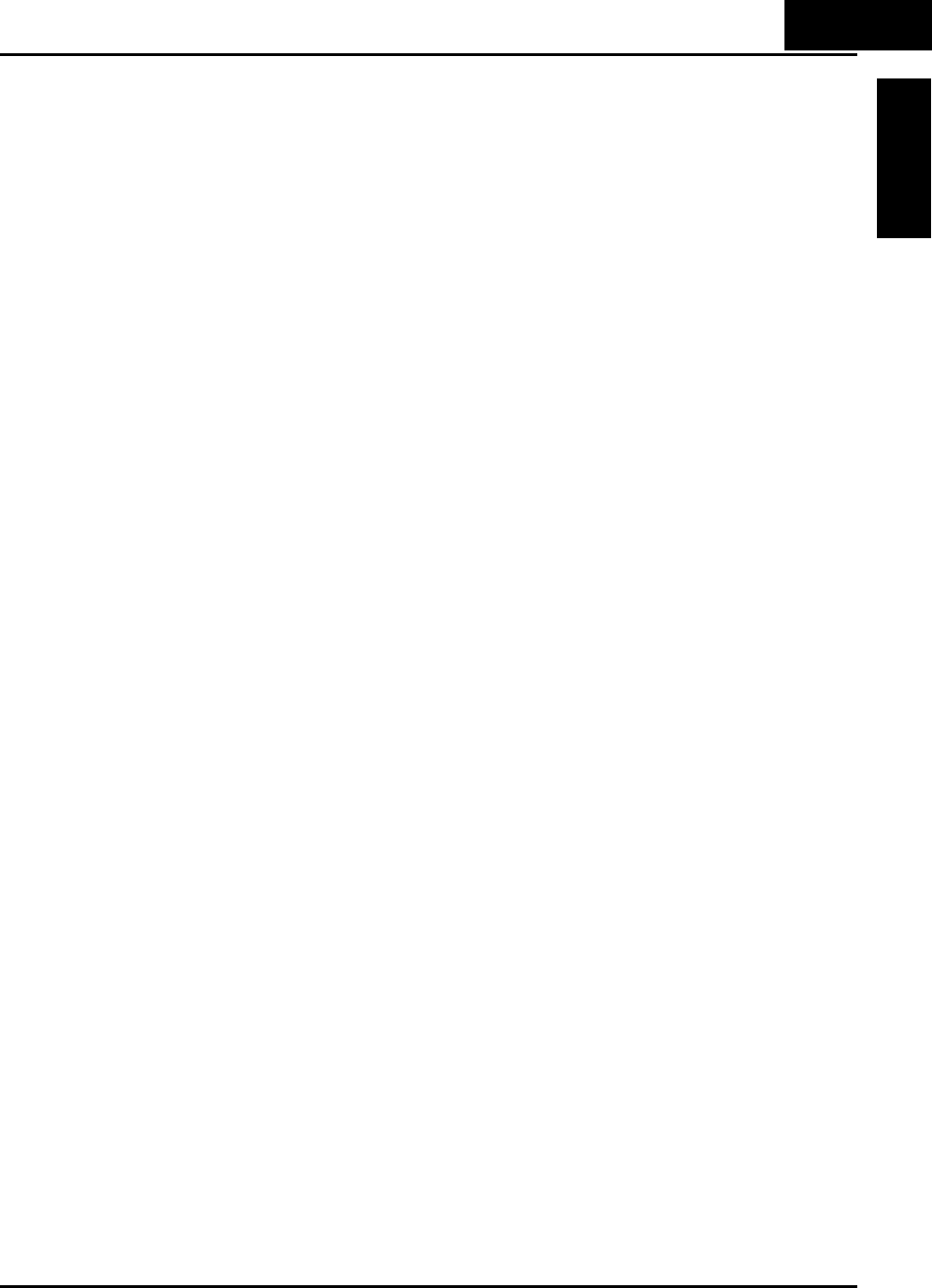
Q. How will I know if my application will require resistive braking?
A. For new applications, it may be difficult to tell before you actually test a
motor/drive solution. In general, some application can rely on system losses
such as friction to serve as the deceleration force, or otherwise can tolerate a
long decel time. These applications will not need dynamic braking.
However, applications with a combination of a high-inertia load and a required
short decel time will need dynamic braking. This is a physics question that
may be answered either empirically or through extensive calculations.
Q. Several options related to electrical noise suppression are available for the Hitachi
inverters. How can I know if my application require any of these options?
A. The purpose of these noise filters is to reduce the inverter electrical noise so
the operation of nearby electrical devices is not affected. Some applications are
governed by particular regulatory agencies, and noise suppression is
mandatory . in those cases, the inverter must have the corresponding noise
filter installed. Other applications may not need noise suppression, unless you
notice electrical interference with the operation of other devices.
Q. The X200 features a PID control. PID loops are usually associated with chemical
processes, heating, or process industries in general. How could the PID loop feature
be useful in my application?
A. You will need to determine the particular main variable in your application the
motor affects. That is the process variable (PV) for the motor. Over time, a
faster motor speed will cause a faster change in the PV than a slow motor
speed will. By using the PID loop feature, the inverter commands the motor to
run at the optimal speed required to maintain the PV at the desired value for
current conditions. Using the PID loop feature will require an additional
sensor and other wiring, and is considered an advanced application.
1
−
19
Getting started