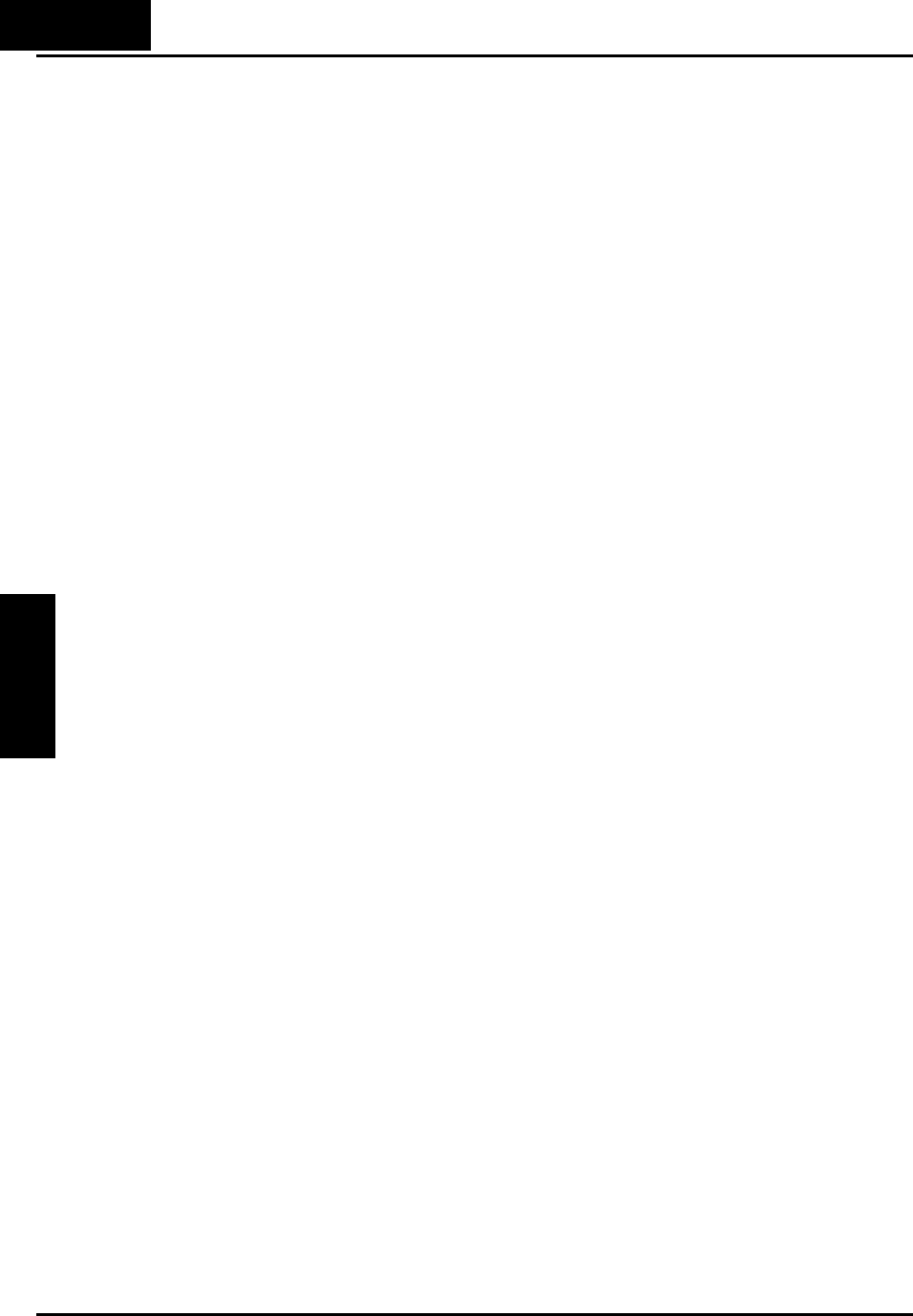
CE-EMC Installation Guidelines
You are required to satisfy the EMC directive (89/336/EEC) when using an X200
inverter in an EU country. To satisfy the EMC directive and to comply with standard,
follow the guidelines in this section.
1. As user you must ensure that the HF (high frequency) impedance between
adjustable frequency inverter, filter, and ground is as small as possible.
• Ensure that the connections are metallic and have the largest possible contact
areas (zinc-plated mounting plates).
2. Avoid conductor loops that act like antennas, especially loops that encompass large
areas.
• Avoid unnecessary conductor loops.
• Avoid parallel arrangement of low-level signal wiring and power-carrying or
noise-prone conductors.
3. Use shielded wiring for the motor cable and all analog and digital control lines.
• Allow the effective shield area of these lines to remain as large as possible; i.e.,
do not strip away the shield (screen) further away from the cable end than
absolutely necessary.
• With integrated systems (for example, when the adjustable frequency inverter is
communicating with some type of supervisory controller or host computer in the
same control cabinet and they are connected at the same ground + PE-potential),
connect the shields of the control lines to ground + PE (protective earth) at both
ends. With distributed systems (for example the communicating supervisory
controller or host computer is not in the same control cabinet and there is a
distance between the systems), we recommend connecting the shield of the
control lines only at the end connecting to the adjustable frequency inverter. If
possible, route the other end of the control lines directly to the cable entry
section of the supervisory controller or host computer. The shield conductor of
the motor cables always must connected to ground + PE at both ends.
• To achieve a large area contact between shield and ground + PE-potential, use a
PG screw with a metallic shell, or use a metallic mounting clip.
• Use only cable with braided, tinned copper mesh shield (type “CY”) with 85%
coverage.
• The shielding continuity should not be broken at any point in the cable. If the
use of reactors, contactors, terminals, or safety switches in the motor output is
necessary, the unshielded section should be kept as short as possible.
• Some motors have a rubber gasket between terminal box and motor housing.
Very often, the terminal boxes, and particularly the threads for the metal PG
screw connections, are painted. Make sure there is always a good metallic
connection between the shielding of the motor cable, the metal PG screw
connection, the terminal box, and the motor housing. If necessary, carefully
remove paint between conducting surfaces.
D−2
Appendix D