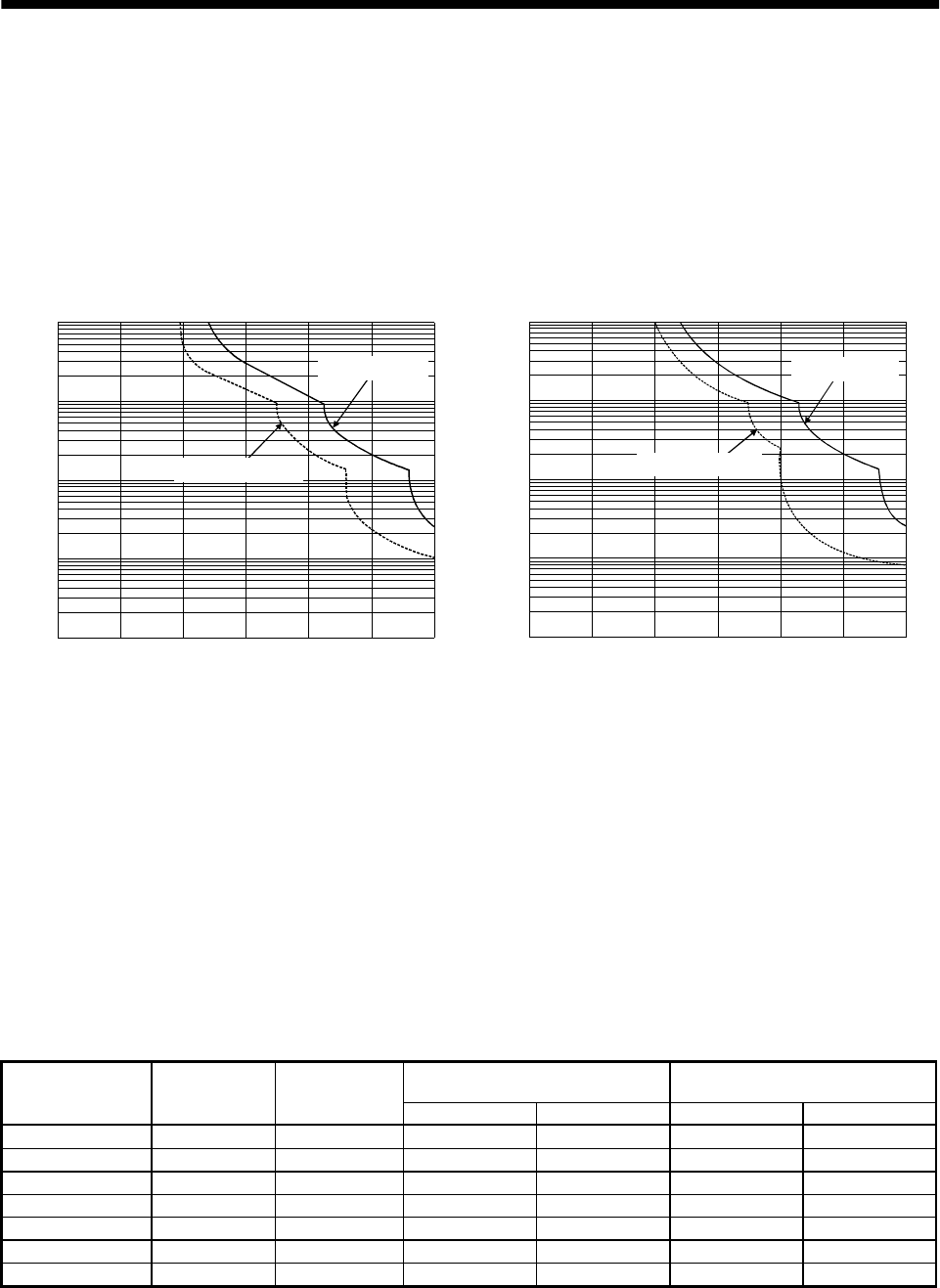
12 - 1
12. CHARACTERISTICS
12. CHARACTERISTICS
12.1 Overload protection characteristics
An electronic thermal relay is built in the servo amplifier to protect the servo motor and servo amplifier
from overloads. Overload 1 alarm (AL.50) occurs if overload operation performed is above the electronic
thermal relay protection curve shown in any of Figs 12.1, Overload 2 alarm (AL.51) occurs if the
maximum current flew continuously for several seconds due to machine collision, etc. Use the equipment
on the left-hand side area of the continuous or broken line in the graph.
In a machine like the one for vertical lift application where unbalanced torque will be produced, it is
recommended to use the machine so that the unbalanced torque is 70% or less of the rated torque.
1000
100
10
1
0.1
0
50
150
200
250
300
(Note) Load ratio [%]
Operation time[s]
100
During rotation
During servo lock
a. MR-E-10A to MR-E-100A
1000
100
10
1
0.1
0
50
150
200
250
300
(Note) Load ratio [%]
Operation time[s]
100
During rotation
During servo lock
b. MR-E-200A
Note: If the servo motor is stopped or low-speed (30r/min or less) operation is performed at an abnormally high duty with torque more
than 100% of the rating being generated, the servo amplifier may fail even in a status where the electronic thermal relay
protection is not activated.
Fig 12.1 Electronic thermal relay protection characteristics
12.2 Power supply equipment capacity and generated loss
(1) Amount of heat generated by the servo amplifier
Table 12.1 indicates servo amplifiers' power supply capacities and losses generated under rated load.
For thermal design of an enclosure, use the values in Table 12.1 in consideration for the worst
operating conditions. The actual amount of generated heat will be intermediate between values at
rated torque and zero torque according to the duty used during operation. When the servo motor is run
at less than the maximum speed, the power supply capacity will be smaller than the value in the
table, but the servo amplifier's generated heat will not change.
Table 12.1 Power supply capacity and generated heat per servo amplifier at rated output
(Note 2)
Servo amplifier-generated heat[W]
Area required for heat dissipation
Servo amplifier Servo motor
(Note 1)
Power supply
capacity[kVA]
At rated torque With servo off [m
2
] [ft
2
]
MR-E-10A(1) HC-KFE13 0.3 25 15 0.5 5.4
MR-E-20A(1) HC-KFE23 0.5 25 15 0.5 5.4
MR-E-40A(1) HC-KFE43 0.9 35 15 0.7 7.5
MR-E-60A HC-SFE52 1.0 40 15 0.8 8.6
MR-E-70A HC-KFE73 1.3 50 15 1.0 10.8
MR-E-100A HC-SFE102 1.7 50 15 1.0 10.8
MR-E-200A HC-SFE202 3.5 90 20 1.8 19.4
Note:1. Note that the power supply capacity will vary according to the power supply impedance. This value assumes that the power
factor improving reactor is not used.
2. Heat generated during regeneration is not included in the servo amplifier-generated heat. To calculate heat generated by the
regenerative brake option, use Equation 13.1 in Section 13.1.1.