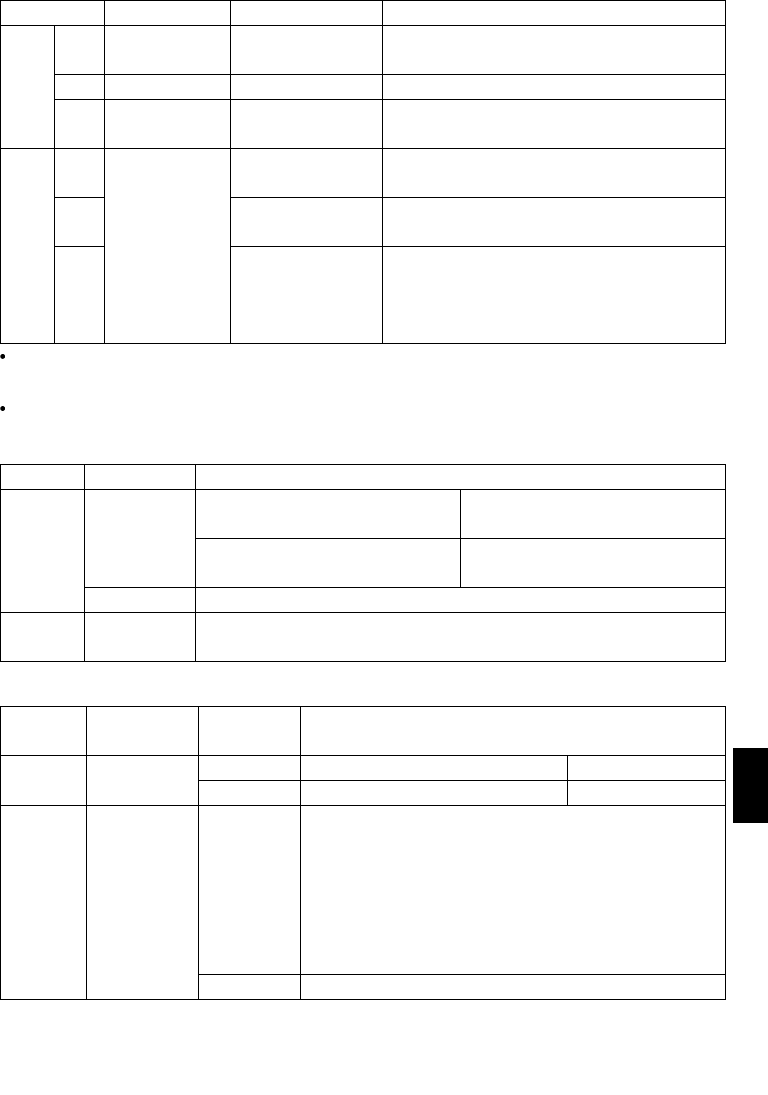
105
2
(4) I/O signals
Signal Terminal Used Function Description
X14
Depending on
Pr. 60 to Pr. 63
PID control
selection
Turn on X14 to exercise PID control.
2 2 Set point input Enter the set point for PID control.Input
44
Process value
input
Enter the 4 to 20mADC process value
signal from the detector.
FUP Upper limit output
Output to indicate that the process value
signal exceeded the upper limit value.
FDN Lower limit output
Output to indicate that the process value
signal exceeded the lower limit value.
Output
RL
Depending on
Pr. 64, Pr. 65
Forward (reverse)
rotation direction
output
"Hi" is output to indicate that the output
indication of the parameter unit is forward
rotation (FWD) or "Low" to indicate that it is
reverse rotation (REV) or stop (STOP).
Enter the set point across inverter terminals 2-5 or in Pr. 93 and enter the process
value signal across inverter terminals 4-5.
To exercise PID control, turn on the X14 signal. When this signal is off, PID control is
not exercised.
Item Entry Description
Set 0V as 0% and 5V as 100%.
When "0" is set in Pr. 73 (5V
selected for terminal 2).
Across
terminals 2-5
Set 0V as 0% and 10V as 100%.
When "1" is set in Pr. 73 (10V
selected for terminal 2).
Set point
Pr. 93 Set the set point (%) in Pr. 93.
Process
value
Across
terminals 4-5
4mA DC is equivalent to 0% and 20mA DC to 100%.
(5) Parameter setting
Parameter
Number
Name Setting Description
20 For heating, pressure control, etc. PID reverse action
88
PID action
selection
21 For cooling, etc. PID forward action
0.1 to 999%
If the proportional band is narrow (parameter setting is
small), the manipulated variable varies greatly with a
slight change of the process value. Hence, as the
proportional band narrows, the response sensitivity
(gain) improves but the stability deteriorates, e.g.
hunting occurs.
Gain K = 1/proportional band
89
PID
proportional
band
- - - No proportional control