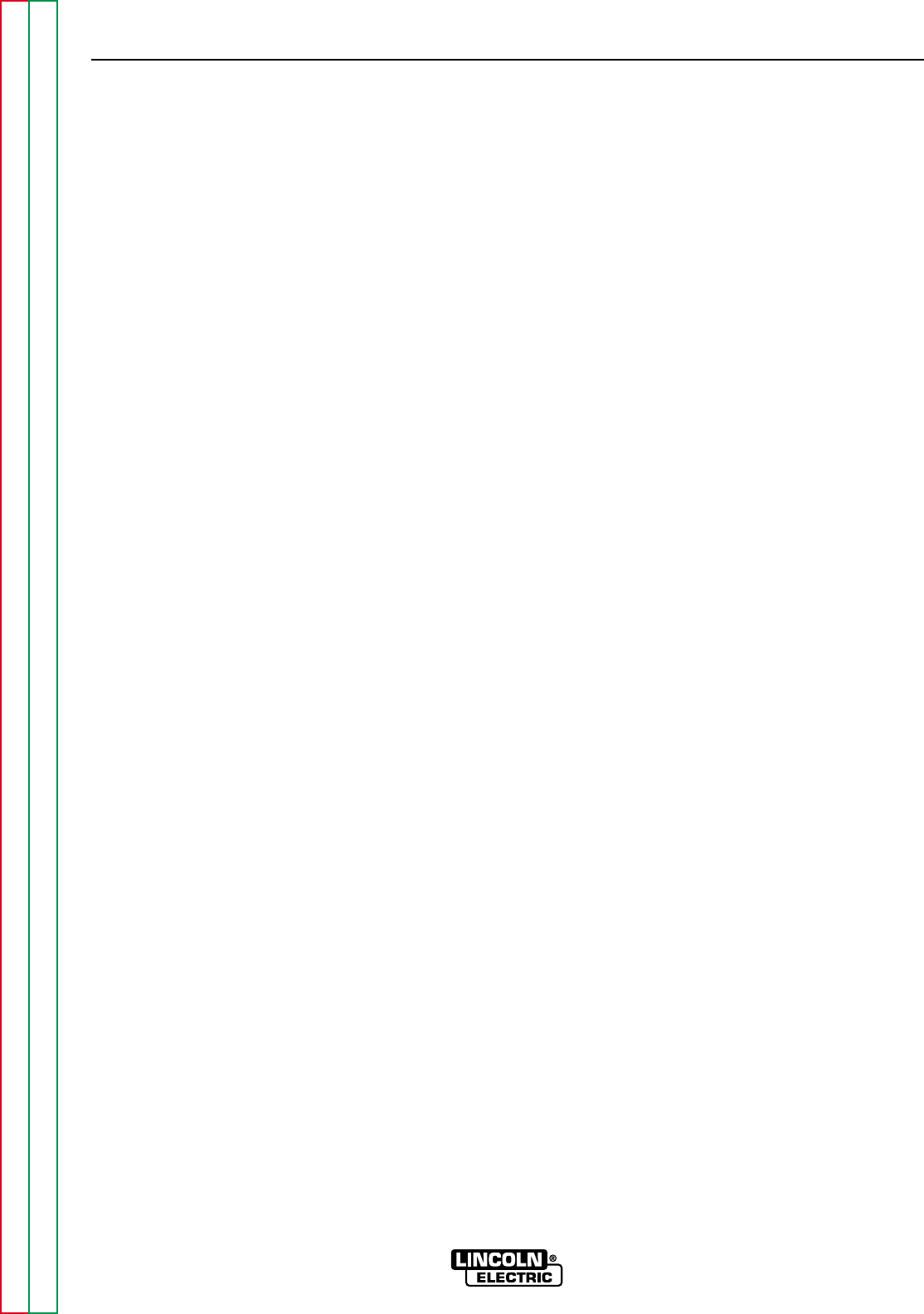
In Pulse processes:
The wave control adjustment allows the frequency set-
ting to vary. Increasing the wave control allows the fre-
quency setting to increase, and decreasing the wave
control allows the frequency setting to decrease.
Varying the wave control setting affects the droplet
transfer and allows fine-tuning for different welding
positions.
In GMAW and FCAW processes:
The wave control adjusts the inductance. (Inductance
is inversely proportional to pinch.) Increasing the wave
control setting decreases the inductance, which
results in the arc getting colder and pinched tighter.
Decreasing the wave control setting increases the
inductance, which results in the arc getting wider.
In Stick processes:
The wave control adjusts the arc force. Increasing the
wave control setting increases the arc force, making
the arc more harsh but less likely to stick. Decreasing
the wave control setting decreases the arc force, mak-
ing the arc softer and smoother.
PULSE WELDING
Some people have trouble getting used to the behav-
ior of the pulsing arc. The parameters programmed
into the Power Wave have been thoroughly tested for
their ability to deliver a sound weld with good appear-
ance. There are, however, a few things to keep in mind
when pulse welding.
Spatter levels are often very low with the pulse
welding process. Pulsing is often used to eliminate
cleaning operations necessary when using other weld-
ing processes.
Fume levels are sometimes lower with the pulsing
process. Whether or not you will get lower fume lev-
els depends on the pulsing programs used. Certain
waveform characteristics are necessary to get low
fume levels. Unfortunately, low fume procedures are
harder to weld with than procedures designed to opti-
mize the welding process.
The pulsing process is not slower than other
processes. The process is sometimes less forgiving
when the arc gets on or ahead of the puddle. More
attention must be paid to the weld to avoid losing the
puddle. Speed is a matter of deposition rate. All
things being equal regarding the joint being welded,
the speed will depend on the wire feed speed. The
travel speed is maximized by maintaining a very short
arc. Often the process is “trimmed” down until the arc
“crackles.” The spatter increases slightly, but many of
the advantages of pulsing are retained. When welding
steel, the Power Wave is designed to run well in this
region between pulse and short arc.
The pulsing process greatly affects the heat input
to the workpiece. This can be a valuable tool for
either increasing or decreasing the heat input with a
given process. For instance, it is possible to greatly
increase the heat input when welding steel at high
deposition rates. On the other hand, it is possible to
reduce the heat input using the pulsing process. For
example, heat input is reduced greatly with some of
the low current stainless steel procedures using the
processes programmed into the Power Wave. In all
cases, the Power Wave procedures have been
checked for their ability to deliver a sound weld.
However, the fusion of the weld metal into the work-
piece may be affected. It is the responsibility of the
user to determine if the welds produced are suitable
and sound.
The Power Wave 450 is optimized for use with a
0.75” (1.9 cm) stickout. The adaptive behavior is pro-
grammed to support a stickout range from 0.5” to
1.25” (1.3 to 3.2 cm). In the low and high end of the
wire feed speed ranges of most processes, the adap-
tive behavior may be restricted. This is a physical
restriction due to reaching the edge of the operating
range for the process. It is possible to achieve adap-
tive behavior for longer stickout lengths. However,
shielding gas is often lost when the stickout is too
long.
A longer electrical stickout is often used with the
pulsing process at higher deposition rates. A long
stickout will increase the melt-off rate of the wire. In
pulse welding, like other wire welding processes, the
arc length is determined by the voltage setting. This
voltage is programmed at the factory for each process
and wire feed speed. It may be changed using the
Voltage setting on the wire feeder.
When adaptive processes are used, the voltage will
vary with stickout. The machine must change the
voltage to keep a stable arc. It is very important to
recognize this. “Actual” arc voltage when welding will
vary because the stickout will seldom be held at the
nominal 1.9 cm value.
OPERATION
B-22 B-22
POWER WAVE 450
Return to Section TOC Return to Section TOC Return to Section TOC Return to Section TOC
Return to Master TOC Return to Master TOC Return to Master TOC Return to Master TOC