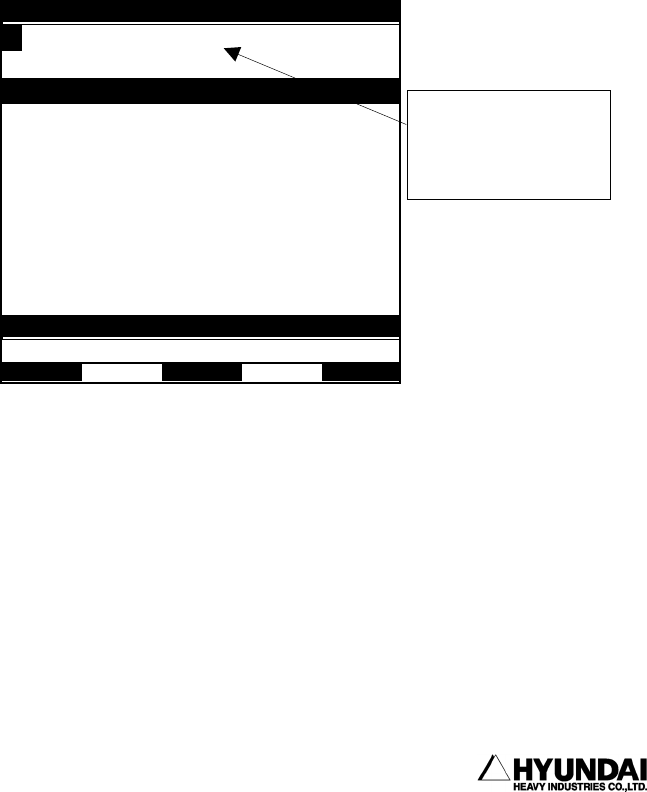
5. Application condition
------------------------------------------------------------------------------------------------
----------------------------------------------------------------------------------------
5 - 3
5.1 Conveyor operation
Outline
It determines the movement of robot when robot handles workpiece on conveyor,
① Normal : Robot moves synchronously according to actual movement of workpiece on
conveyor.
② Simulation : Without operating conveyor, user can operated robot movement by
entering conveyor speed. It is useful to check cycle time after teaching.
③ Test : Like plat test, it is the condition where conveyor is not operated and robot
movement can be checked. Different aspects from plan test is that teaching
point can be checked at stop condition of workpiece as pulse count is not
reset even though executing Program END
Reference
Depending on setting condition for conveyor movement, the following is displayed
in manual or auto mode.
Conveyor pulse count not to related move type is only counted by activation of limit
switch.
In simulation, value calculated from distant is not always correct because pulse
counter of conveyor is separated from registry
Normally, in playback mode, conveyor speed has actual movement speed of conveyor,
but, in plan test operation, plan test speed entered from user is always 0 value.
14:39:38 *** A U T O *** A:0 S:4
T0 C-N SR:100% 1Cycl
PN:100[*]__ S/F:4/0
Robot:H120, 6axes, 10 steps
S1 MOVE P,S=100%,A=0,T=1
S2 MOVE P,S=100%,A=0,T=1
S3 MOVE P,S=100%,A=0,T=1
S4 MOVE P,S=100%,A=0,T=1
S5 MOVE P,S=100%,A=0,T=1
S6 MOVE P,S=100%,A=0,T=1
S7 MOVE P,S=100%,A=0,T=1
S8 END
>
Service Rel WAIT Cond Set
According to the
Mode,“C-N","C-S","
C-T" are displayed.